Hydraulic fittings are critical components in any hydraulic system, connecting hoses and components while ensuring fluid flow and system integrity. However, with a wide variety of fitting types available, accurate identification is crucial for proper installation, maintenance, and repair. This guide will provide you with the knowledge and techniques to confidently identify different types of hydraulic fittings.
By understanding the key characteristics of various fittings, such as their thread types, sealing mechanisms, and construction materials, you can ensure compatibility, prevent leaks, and optimize the performance of your hydraulic system.
Why Hydraulic Fitting Identification is Important
Accurate hydraulic fitting identification is paramount for several critical reasons. Firstly, it ensures compatibility. Using the wrong fitting can lead to leaks, pressure drops, and even system failure. Incorrectly sized or mismatched fittings may not create a proper seal, resulting in fluid leaks, which can cause damage to equipment, create safety hazards, and contaminate the work environment.
Secondly, proper identification facilitates efficient maintenance and repair. Knowing the exact type and size of a fitting allows for quick and easy sourcing of replacement parts, minimizing downtime and reducing repair costs.
Finally, accurate identification contributes to overall system safety and reliability. Using the correct fittings ensures that the hydraulic system operates as designed, minimizing the risk of unexpected failures and potential injuries.
By understanding the importance of accurate fitting identification and employing the appropriate identification techniques, you can significantly enhance the safety, reliability, and efficiency of your hydraulic systems.
Hydraulic Fitting Identification Tool
Hydraulic fitting identification tools are designed to simplify the process of determining the type and size of a fitting.
These tools often incorporate a combination of features to assist in accurate identification:
Thread Gauges:
- These gauges are designed to measure the thread diameter and pitch of a fitting.
- They typically include a set of precisely machined go/no-go gauges or a series of pins with varying diameters to match common thread sizes.
- This helps determine the thread size and pitch, which are crucial for fitting compatibility.
Fitting Identification Cards:
- These cards often feature diagrams and illustrations of various fitting types, including JIC, ORFS, NPT, BSP, and others.
- They may also include dimensional information and other relevant details to aid in identification.
Angle Gauges:
- For flared fittings (like JIC), angle gauges can be used to measure the flare angle.
- This helps to ensure compatibility with the corresponding female fitting.
O-Ring Groove Gauges:
- These gauges are specifically designed to measure the dimensions of O-ring grooves in ORFS fittings.
- They help ensure proper O-ring selection and installation.
Combination Tools:
Some tools combine multiple features, such as thread gauges, angle gauges, and fitting identification charts, in a single compact unit.
These tools can significantly streamline the fitting identification process, reducing the time and effort required while minimizing the risk of errors. By using these tools in conjunction with visual inspection and reference materials, technicians can quickly and accurately identify hydraulic fittings, ensuring proper selection, installation, and system performance.
How to Identify Hydraulic Fittings
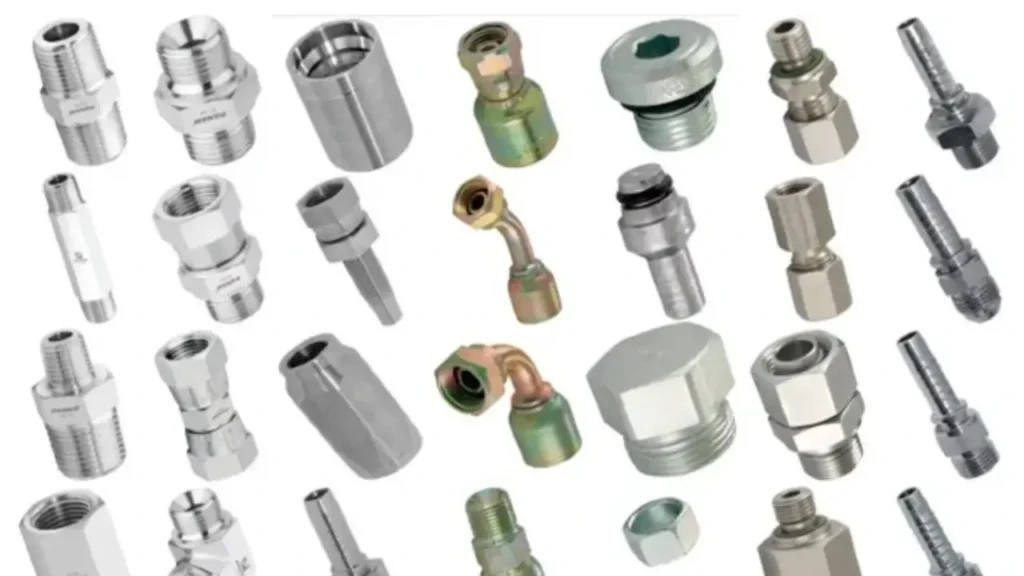
Here is a hydraulic fitting identification guide in the following for your conference:
Step 1. Visual Inspection
Begin by carefully examining the fitting visually. Scrutinize the thread profile. Are they straight (like NPT), tapered, or exhibit a specific angle (like JIC)?
Observe for sealing mechanisms such as O-ring grooves, flared surfaces, or flat faces. These features are crucial for identifying the fitting type. Note the fitting’s orientation: straight, elbow, tee, or other configurations. Check for any markings or stamps that might indicate the manufacturer or model number. These markings can provide valuable clues for further identification.
Step 2. Analyze Thread Characteristics
Carefully examine the thread characteristics. Determine the thread type, whether it’s NPT, BSP, metric, or another standard.
Measure the thread diameter using a caliper. Ensure accurate measurement by taking multiple readings at different points along the thread. Determine the thread pitch, either by using a thread pitch gauge or by manually counting the number of threads per inch (TPI). Note the thread direction (right-hand or left-hand).
Step 3. Identify Sealing Mechanisms
Observe any sealing mechanisms present on the fitting. Look for O-ring grooves, flared surfaces, flat faces, or other features designed to create a seal. The presence of these features can significantly narrow down the possible fitting types. For example, ORFS fittings are characterized by O-ring grooves, while JIC fittings have a specific 37-degree flare angle.
Step 4. Consult Reference Materials
Utilize fitting identification guides, charts, or manufacturer catalogs. These resources provide valuable information on various fitting types, their characteristics, and dimensional specifications. Cross-reference the visual observations and measured dimensions with the information provided in these resources. This comparison will help you narrow down the possible fitting types and identify the most likely match.
Step 5. Consider Application
The application of the fitting can provide valuable clues to its type. For example, high-pressure applications often utilize ORFS fittings, while automotive brake systems may employ banjo fittings. Consider the specific hydraulic system or equipment where the fitting is used. This information can help you make an educated guess about the fitting type and its intended purpose.
By carefully following these steps and utilizing available resources, you can effectively identify hydraulic fittings, ensuring compatibility, proper installation, and the safe and efficient operation of your hydraulic system.
How to Identify Hydraulic Fitting Size
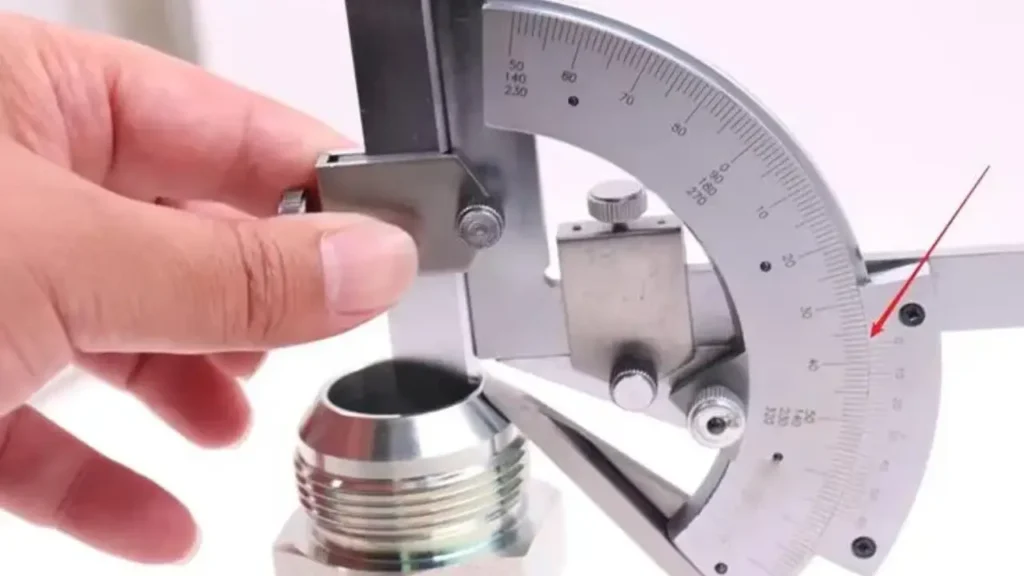
1. Determine the Thread Size:
- Measure the Outer Diameter (OD): For male threads, use a caliper to measure the outer diameter of the threads. Ensure the caliper jaws are perpendicular to the thread axis and take multiple measurements at different points along the thread length to average out any slight variations.
- Measure the Inner Diameter (ID): For female threads, measure the inner diameter of the threads using a caliper. Ensure the caliper jaws are parallel to the thread axis.
- Consult Thread Size Charts: Refer to thread size charts or tables that list common thread sizes and their corresponding dimensions. Compare your measured values to the chart to determine the closest match.
2. Determine the Thread Pitch:
- Use a Thread Pitch Gauge: This specialized tool accurately measures the distance between adjacent threads. Select the gauge with the appropriate thread pitch range. Place the gauge on the threads and find the matching pitch.
- Manual Calculation (for TPI): If a thread pitch gauge is unavailable, you can manually calculate the threads per inch (TPI). Measure the distance along the thread axis that covers a known number of threads. Divide the measured distance by the number of threads to determine the TPI.
3. Identify the Thread Standard:
- Observe Thread Profile: Examine the thread profile. Are they straight, tapered (like NPT), or have a specific angle (like JIC)?
- Consult Reference Materials: Refer to industry standards and manufacturer specifications to identify the specific thread standard (NPT, BSP, metric, etc.).
4. Cross-Reference Hydraulic Fitting Measurements:
- Compare with Fitting Charts: Utilize fitting charts and tables available online or in industry publications. These charts often list fitting sizes and their corresponding thread dimensions. Cross-reference your measured values with the dimensions listed in these resources to identify the fitting size.
- Consult Manufacturer Specifications: If possible, refer to the manufacturer‘s specifications for the specific fitting or hydraulic system. This will provide the most accurate and up-to-date information on fitting sizes and dimensions.
5. Consider Application Context:
- The intended application of the fitting can provide valuable clues to its size. For example, fittings used in high-pressure applications are typically larger than those used in low-pressure applications.
- Consider the size of the hoses or pipes that the fitting will connect to. This can provide an indication of the appropriate fitting size.
By carefully following these steps and utilizing appropriate tools and resources, you can accurately determine the size of hydraulic fittings, ensuring proper selection, installation, and the overall reliability of your hydraulic system.
Conclusion
Accurately identifying hydraulic fittings is crucial for ensuring compatibility, proper installation, and the safe and efficient operation of your hydraulic system. By carefully examining the fitting’s features, consulting reference materials, and utilizing the techniques outlined in this guide, you can confidently identify the type and size of any hydraulic fitting.
For high-quality, precision-engineered hydraulic fittings, choose Kingdaflex. We offer a wide range of fittings designed to meet the most stringent industry standards. Request a quote today to explore our comprehensive product offerings and discover how Kingdaflex can enhance your hydraulic system performance.