Hydraulic systems are the backbone of countless industrial and mechanical applications, from heavy machinery to precision instruments. The seamless flow of hydraulic fluid is crucial for optimal system performance, and this relies heavily on the selection and installation of the right hydraulic fittings.
This guide will explore the diverse world of hydraulic fitting types, providing valuable insights into their characteristics, applications, and the key factors to consider when choosing the perfect fittings for your specific project.
What Are Hydraulic Fittings
Hydraulic fittings are specialized components that act as the crucial connectors within a hydraulic system.
Hydraulic Fitting Types
Hydraulic Hose Fittings
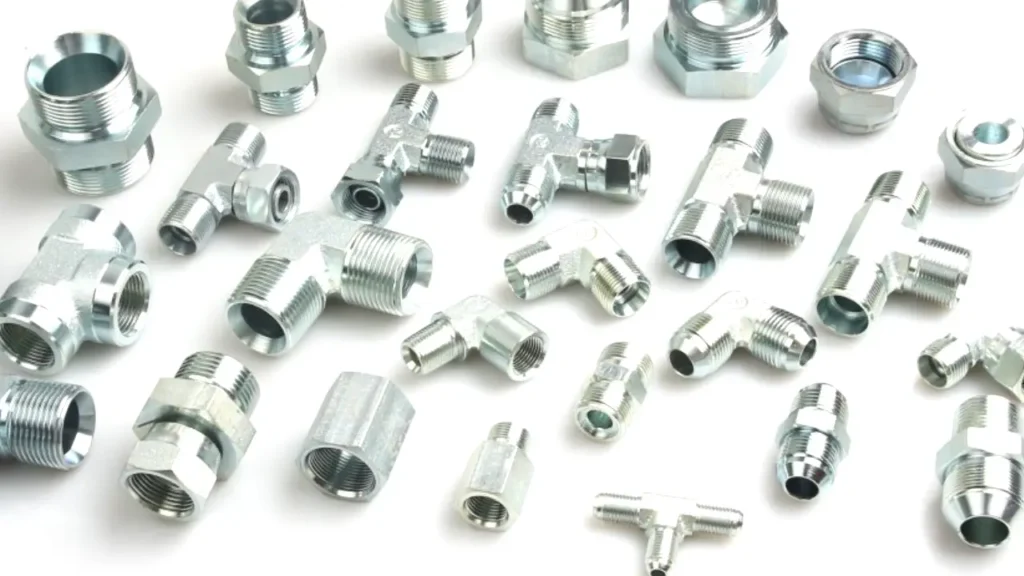
Hydraulic hose fittings are the critical components that connect hydraulic hoses to other parts of the system, such as pumps, valves, cylinders, and motors. They play a vital role in ensuring the secure and leak-free transfer of hydraulic fluid.
Key Functions:
- Form a Secure Connection: Hose fittings create a robust and leak-proof seal between the hose and other system components.
- Maintain System Integrity: Prevent fluid leakage, which can lead to safety hazards, reduced system efficiency, and costly repairs.
- Enable Fluid Flow: Ensure the smooth and uninterrupted flow of hydraulic fluid throughout the system.
Types of Hose Fittings:
- Crimped Fittings: These are permanently attached to the hose during manufacturing. They offer high strength and durability, making them suitable for demanding applications. However, replacing a hose with a crimped fitting requires cutting and re-crimping, which can be time-consuming.
- Reusable Fittings: Designed for easier hose replacement. They utilize mechanisms like clamping or specialized threads that allow for repeated assembly and disassembly.
- One-Piece Fittings: Combine the fitting and the hose end into a single unit, simplifying installation and minimizing potential leak points.
Factors to Consider:
- Hose type and size: Compatibility is crucial for a secure and reliable connection.
- Operating pressure and temperature: The fitting must withstand the operating conditions of the system.
- Fluid compatibility: The fitting material must be compatible with the hydraulic fluid used.
- Application requirements: Consider factors like vibration, pulsation, and corrosion resistance.
Properly selected and installed hose fittings are essential for the safe and efficient operation of any hydraulic system.
Hydraulic Adapter Fittings
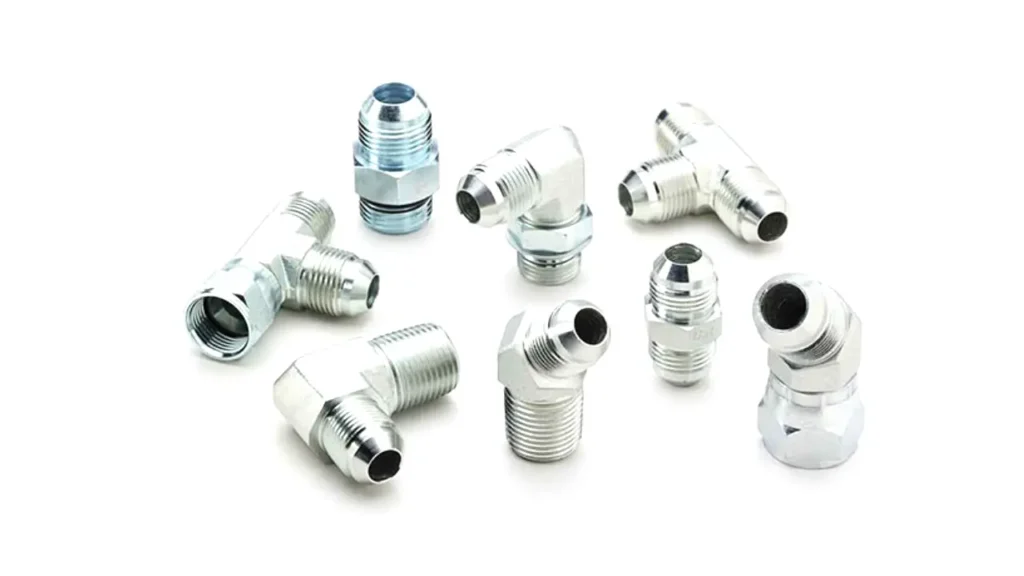
Hydraulic adapter fittings are crucial components in hydraulic systems, serving as connectors between components with incompatible thread sizes, types, or configurations. Essentially, they bridge the gap to ensure a seamless and leak-free connection.
Key Functions:
- Thread Conversion: Adapters allow for the connection of components with different thread standards, such as NPT (National Pipe Thread), BSPP (British Standard Pipe Parallel), and metric threads. For example, an adapter might connect an NPT male fitting to a BSPP female fitting.
- Size Reduction/Increase: Reducing bushings are a common type of adapter that connects a larger diameter fitting to a smaller one, enabling a smooth transition in fluid flow.
- Changing Flow Direction: Elbow adapters can change the direction of fluid flow while simultaneously adapting between different thread types.
- Branching Connections: Branch adapters allow for the splitting of fluid flow into multiple directions.
Benefits:
- Flexibility and Compatibility: Adapters increase the flexibility of system design by allowing for the integration of components from various manufacturers with different thread standards.
- Maintenance and Repair: They simplify maintenance and repair procedures by enabling easier access and component replacement.
- System Modification: Adapters allow for modifications to existing systems to accommodate changes in component design or to incorporate new components.
Selecting the Right Adapter:
- Compatibility: Ensure the adapter is compatible with the thread sizes and types of the components being connected.
- Pressure and Temperature Rating: The adapter must be able to withstand the operating pressures and temperatures of the hydraulic system.
- Material Compatibility: The adapter material should be compatible with the hydraulic fluid and the materials of the connected components.
By carefully selecting and using hydraulic adapter fittings, system designers and technicians can ensure the efficient and reliable operation of their hydraulic systems while maintaining flexibility and ease of maintenance.
Hydraulic Bulkhead Fittings
Hydraulic bulkhead fittings are specialized connectors designed to pass through a wall, bulkhead, or other barrier, allowing for connections to be made from one side to the other.
Key Features:
- Pass-through Design: The primary function is to facilitate connections across a physical barrier without requiring access to the interior of the equipment.
- Versatility: Available in a wide range of configurations, including straight, elbow, and tee designs, to accommodate various system requirements.
- Materials: Typically constructed from durable materials such as stainless steel, brass, and carbon steel, offering excellent corrosion resistance and compatibility with various hydraulic fluids.
Applications:
- Industrial Machinery: Widely used in industrial machinery where access to the interior of equipment may be limited or inconvenient. This includes applications in food processing, packaging, material handling, and other sectors.
- Marine Applications: Crucial in marine environments where access to the interior of vessels can be challenging. They enable connections to be made through ship hulls, bulkheads, and other barriers.
- Aerospace Applications: Used in aircraft and spacecraft to connect components within confined spaces, ensuring reliable fluid transfer and system integrity.
Benefits:
- Improved Accessibility: Simplify maintenance and repair procedures by allowing for easier access to components without the need for disassembly.
- Space-Saving: Enable compact and efficient system designs by minimizing the need for complex routing of hoses and pipes.
- Enhanced Safety: Minimize the risk of leaks and spills by providing a secure and reliable connection across the barrier.
In essence, hydraulic bulkhead fittings play a vital role in enhancing the accessibility, efficiency, and safety of hydraulic systems, particularly in applications where space is constrained or access is limited.
Hydraulic Tee and Cross Fittings
Hydraulic tee and cross fittings are essential components in any hydraulic system, playing a crucial role in directing the flow of fluid.
- Tee Fittings: These fittings have one inlet and two outlets, allowing the fluid to branch off in two directions. They are widely used in distribution systems to direct hydraulic fluid to multiple components, such as cylinders, motors, and valves.
- Cross Fittings: These fittings have one inlet and three outlets, providing even more branching options. They are used in more complex configurations where fluid needs to be directed to multiple points simultaneously.
Key Functions:
- Fluid Distribution: Tee and cross fittings are fundamental for distributing hydraulic fluid efficiently throughout the system.
- System Flexibility: They provide flexibility in system design by allowing for multiple connections and branching points.
- Component Integration: They enable the integration of various components into the hydraulic circuit, such as actuators, valves, and filters.
Considerations for Selection:
- Flow Rate: The fitting must be able to handle the required flow rate without causing excessive pressure drop or turbulence.
- Pressure Rating: The fitting must be able to withstand the operating pressures of the system.
- Material Compatibility: The fitting material must be compatible with the hydraulic fluid and the materials of the connected components.
By selecting the appropriate tee and cross fittings, engineers and technicians can ensure optimal system performance, reliability, and efficiency.
Hydraulic Plugs and Caps Fittings
Hydraulic plugs and caps are essential components in any hydraulic system, serving vital roles in maintaining system integrity and safety.
- Plugs: These are threaded fittings used to seal off unused ports or openings within the hydraulic system. They effectively prevent:
- Fluid leakage: Minimizing fluid loss and potential contamination.
- Contaminant ingress: Preventing dirt, dust, and other debris from entering the system, which can cause damage and malfunctions.
- System pressure loss: Ensuring the system maintains its intended operating pressure.
- Caps: Often push-on or snap-on covers, caps are used to seal off open ends of hoses, pipes, or fittings. They provide a simple yet effective means of:
- Preventing fluid leakage: Protecting against accidental spills or drips.
- Minimizing contamination: Keeping out dust, dirt, and moisture.
- Protecting components: Preventing damage to the internal components of fittings or hoses during storage, transport, or maintenance.
Key Considerations:
- Material Compatibility: Plugs and caps must be made of materials compatible with the hydraulic fluid and the surrounding environment. Common materials include steel, stainless steel, brass, and plastic.
- Size and Thread Compatibility: Accurate sizing and thread compatibility are crucial for ensuring a secure and leak-free seal.
- Durability: Plugs and caps should be durable and resistant to wear and tear, especially in harsh environments or those subject to frequent handling.
By effectively utilizing plugs and caps, hydraulic system operators can enhance system reliability, improve safety, and minimize maintenance costs.
Note: This information is for general knowledge and guidance only. Always consult with a qualified engineer or hydraulic specialist for specific applications and material recommendations.
Hydraulic Flange Fittings
Hydraulic flange fittings are specialized connectors designed for high-pressure applications and large-diameter connections within a hydraulic system.
Key Characteristics:
- Bolted Connection: They utilize a bolted flange connection, creating a robust and leak-proof seal between components. This design ensures high strength and reliability, making them suitable for demanding applications.
- Large Diameter Connections: Flange fittings are typically used for larger pipe or hose sizes, where other types of fittings may not be practical or provide sufficient strength.
- High Pressure Capability: They are designed to withstand extremely high pressures, making them ideal for heavy-duty applications such as those found in industrial machinery, large-scale hydraulic presses, and other demanding environments.
Advantages:
- High Pressure and Flow Capacity: Capable of handling high pressures and large volumes of fluid flow.
- Reliable Sealing: The bolted flange connection provides a secure and reliable seal, minimizing the risk of leaks and ensuring system integrity.
- Versatility: Available in a wide range of sizes and configurations to suit various application requirements.
Disadvantages:
- More Complex Installation: Installation and maintenance can be more complex compared to other fitting types, requiring more time and effort.
- May Require Specialized Tools: May require specialized tools and equipment for installation and maintenance, such as torque wrenches and specialized alignment tools.
Applications:
- Heavy-duty industrial machinery: Used in various industrial applications, including heavy equipment, construction machinery, and material handling systems.
- Large-scale hydraulic presses: Employed in applications requiring high force and pressure, such as metal forming and forging processes.
- Oil and gas industry: Used in high-pressure applications within the oil and gas industry, such as pipelines and drilling equipment.
In summary, hydraulic flange fittings are essential components for high-pressure and large-diameter hydraulic systems. Their robust design, high pressure capability, and reliable sealing make them ideal for demanding applications where safety, reliability, and performance are critical.
Hydraulic Reusable Fittings
Hydraulic reusable fittings are designed to be easily disconnected and reconnected without damaging the hose or the fitting itself. This offers significant advantages in terms of maintenance and repair, making them a valuable asset in many hydraulic systems.
Key Advantages:
- Reduced Downtime: Reusable fittings minimize downtime associated with hose replacement. When a hose needs to be replaced, the fitting can be reused, significantly reducing repair time and costs.
- Easier Maintenance: The ability to easily disconnect and reconnect components simplifies maintenance procedures, allowing for quicker inspections, repairs, and troubleshooting.
- Cost-Effectiveness: By reducing the need for frequent hose replacements and minimizing downtime, reusable fittings contribute to lower overall maintenance costs.
Common Types of Reusable Fittings:
- Swivelling Fittings: These fittings allow for rotation of the connected component without twisting or kinking the hose. This is crucial in applications where movement is required, preventing hose damage and improving system flexibility.
- Compression Fittings: These utilize a ferrule that is compressed against the hose, creating a secure seal. They are widely used due to their versatility, ease of installation, and reliable performance.
- Quick-Disconnect Couplings: These fittings allow for rapid connection and disconnection of hoses, making them ideal for applications where frequent connections and disconnections are necessary.
Applications:
Reusable fittings are widely used in various industries, including:
- Construction Equipment: Where frequent hose connections and disconnections are required.
- Agriculture: In mobile equipment like tractors and harvesters.
- Material Handling: In forklifts, cranes, and other equipment that require frequent hose movements.
- Industrial Machinery: In applications where ease of maintenance and quick repairs are critical.
Choosing the Right Reusable Fittings:
Selecting the appropriate reusable fittings requires careful consideration of factors such as:
- Operating pressure and temperature: The fittings must be able to withstand the operating conditions of the system.
- Fluid compatibility: The materials used in the fittings must be compatible with the hydraulic fluid.
- Application requirements: The fittings should be selected based on the specific demands of the application, such as frequency of connection/disconnection, movement requirements, and space constraints.
By utilizing reusable fittings, hydraulic system operators can enhance efficiency, reduce downtime, and improve overall system performance.
Hydraulic One-piece Fittings
Hydraulic one-piece fittings are a unique type of hose fitting that integrates the fitting and the hose end into a single, inseparable unit. This innovative design offers several key advantages:
- Simplified Assembly: One-piece fittings eliminate the need for separate fittings and the associated assembly steps. This significantly reduces installation time and effort, streamlining the process and minimizing the potential for errors.
- Reduced Leak Points: By eliminating the connection between the fitting and the hose, one-piece fittings minimize the number of potential leak points. This enhances system reliability and reduces the risk of fluid leaks, which can lead to safety hazards and system inefficiencies.
- Compact Design: Due to their integrated design, one-piece fittings often have a more compact and streamlined profile compared to traditional fittings. This can be beneficial in applications where space is limited, such as in mobile equipment or in confined spaces within machinery.
- Improved Durability: In some cases, one-piece fittings can offer improved durability and resistance to vibration and shock compared to traditional fittings, as the integrated design can provide a more robust and secure connection.
However, it’s important to note that one-piece fittings may have some limitations:
- Hose Replacement: Replacing a hose with a one-piece fitting can be more challenging, as the entire assembly needs to be replaced.
- Repair Limitations: If the fitting itself is damaged, the entire assembly may need to be replaced, which can increase repair costs.
Despite these limitations, one-piece fittings offer a valuable solution for many hydraulic applications, particularly those that prioritize simplicity, reliability, and space efficiency.
Key Applications:
- Mobile Equipment: Used in construction and agricultural machinery where space is limited and ease of installation is crucial.
- Aerospace: Used in aircraft and spacecraft applications where weight and space constraints are critical.
- Industrial Machinery: Used in various industrial applications where reliability and ease of maintenance are paramount.
By carefully considering the specific requirements of the application, one-piece fittings can offer a valuable solution for enhancing the performance and reliability of hydraulic systems.
Hydraulic Push Lock Fittings
Hydraulic push lock fittings are a type of reusable fitting that offers a quick and easy method for connecting and disconnecting hoses. These fittings utilize a simple push-to-connect mechanism, making them ideal for applications where frequent connections and disconnections are required.
Key Features:
- Ease of Use: Installation and removal are typically accomplished with a single hand, significantly reducing installation time.
- Versatility: Available in a wide range of sizes and configurations to suit various applications.
- Reliability: When properly installed, push lock fittings provide a secure and leak-free connection.
- Durability: Many push lock fittings are designed to withstand demanding environments and provide long-lasting service.
Applications:
- Mobile Equipment: Widely used in mobile applications such as construction equipment, agricultural machinery, and material handling equipment where quick connections and disconnections are crucial for efficiency.
- Industrial Machinery: Employed in various industrial settings where hoses may need to be frequently connected and disconnected for maintenance, repair, or reconfiguration.
- Testing and Maintenance: Used in testing and maintenance procedures where quick access to components is required.
Benefits:
- Increased Productivity: Faster connections and disconnections lead to increased productivity and reduced downtime.
- Improved Safety: Minimize the risk of leaks and spills, enhancing safety in the workplace.
- Reduced Maintenance Costs: Ease of installation and maintenance can help to reduce overall maintenance costs.
Limitations:
- Pressure Limitations: May not be suitable for extremely high-pressure applications.
- Potential for Leakage: Improper installation or wear and tear can lead to leaks.
Overall, push lock fittings offer a convenient and efficient solution for connecting and disconnecting hydraulic hoses in a wide range of applications. Their ease of use, versatility, and reliability make them a popular choice in many industries.
Hydraulic Compression Fittings
Hydraulic compression fittings are a type of reusable fitting that utilizes a ferrule (a metal sleeve) to create a secure and leak-proof connection between a tube or hose and the fitting.
How they work:
- The ferrule is inserted into the fitting body.
- The tube is then inserted into the fitting.
- A nut is tightened onto the fitting, which compresses the ferrule against the tube.
- This compression creates a tight seal between the tube and the fitting, preventing fluid leakage.
Key Advantages:
- Versatility: Suitable for a wide range of applications, including high-pressure systems.
- Reusability: Can be easily disassembled and reassembled multiple times without damaging the hose or fitting.
- Ease of installation: Relatively easy to install compared to other types of fittings, requiring minimal specialized tools.
- Reliability: Provide a reliable and leak-free connection when properly installed.
Applications:
- Industrial machinery: Widely used in various industrial applications, including manufacturing, construction, and material handling.
- Mobile equipment: Commonly found in mobile equipment such as trucks, tractors, and construction machinery.
- Aerospace: Used in aircraft and spacecraft where reliability and safety are critical.
Factors to Consider:
- Tube material and size: The compression fitting must be compatible with the type and size of the tube being used.
- Operating pressure and temperature: The fitting must be able to withstand the operating conditions of the hydraulic system.
- Fluid compatibility: The materials of the fitting and ferrule must be compatible with the hydraulic fluid.
Proper installation of compression fittings is crucial for ensuring their reliability and performance. It is essential to follow the manufacturer‘s instructions carefully and use the appropriate tools and techniques to achieve a secure and leak-free connection.
Hydraulic Hose Barb Fittings
Hydraulic hose barb fittings are a common and relatively simple type of fitting used to connect hoses in various applications.
- Key Feature: These fittings feature a barbed end that is inserted into the hose. The hose is then secured in place using a clamp or a crimped ferrule.
- Materials: Typically made from materials like brass, steel, or stainless steel, chosen for their strength and corrosion resistance.
- Applications: Commonly used in low-pressure applications, such as:
- Automotive applications (fuel lines, coolant lines)
- Agricultural equipment
- General industrial applications
Advantages:
- Simple and cost-effective: Relatively inexpensive to manufacture and install.
- Easy to assemble: Can be easily installed using basic tools.
- Widely available: Easily found in most hardware and industrial supply stores.
Disadvantages:
- Limited to lower pressure applications: Not suitable for high-pressure applications due to the potential for leakage.
- May require frequent tightening: The clamp or ferrule may loosen over time, requiring periodic tightening to maintain a secure seal.
- Potential for leaks: If not installed correctly or if the hose or clamp deteriorates, leaks may occur.
Proper Installation:
- Select the correct size: Ensure the barb size is compatible with the inner diameter of the hose.
- Clean the hose end: Remove any dirt, debris, or burrs from the hose end before inserting it onto the barb.
- Secure the hose: Use appropriate clamps or ferrules to securely attach the hose to the barb.
- Tighten properly: Tighten the clamps or ferrules to the manufacturer‘s specifications to ensure a secure and leak-free connection.
While relatively simple, proper selection and installation of hose barb fittings are crucial for ensuring the safety and reliability of any hydraulic system.
Hydraulic Quick Coupler Fittings
Hydraulic quick couplers are specialized fittings designed for rapid connection and disconnection of hydraulic lines. They significantly improve efficiency and convenience in various applications where frequent attachments and detachments are necessary.
Key Features:
- Speed and Convenience: Quick couplers enable fast and easy connection and disconnection of hydraulic hoses, minimizing downtime and increasing productivity.
- Self-Sealing Mechanism: Most quick couplers incorporate a self-sealing mechanism that prevents fluid leakage when disconnected. This minimizes fluid loss and contamination, improving system efficiency and safety.
- Versatility: Available in a wide range of sizes and configurations to suit various applications, including different pressure ratings, flow rates, and thread types.
- Improved Safety: By minimizing the need for manual connections and disconnections, quick couplers reduce the risk of injuries and accidents.
Applications:
- Construction Equipment: Widely used in construction equipment, such as excavators, loaders, and backhoes, for quickly attaching and detaching various attachments like buckets, breakers, and augers.
- Agricultural Machinery: Used in tractors, combines, and other agricultural equipment for connecting and disconnecting implements like plows, cultivators, and sprayers.
- Material Handling: Utilized in forklifts, cranes, and other material handling equipment for attaching and detaching various attachments and accessories.
- Industrial Applications: Employed in various industrial settings, such as manufacturing plants and factories, for connecting and disconnecting hydraulic tools and equipment.
Types of Quick Couplers:
- Flat Face Couplers: Feature a flat face design for easy connection and disconnection.
- Poppet Couplers: Utilize a poppet valve to control fluid flow and prevent leakage.
- Ball Couplers: Utilize a ball valve to control fluid flow.
- Sleeve Couplers: Utilize a sleeve mechanism to connect and disconnect the coupling.
Selecting the Right Quick Coupler:
- Pressure and flow rate requirements: The quick coupler must be able to handle the operating pressures and flow rates of the hydraulic system.
- Compatibility: Ensure compatibility with the hose sizes and thread types of the connected components.
- Environmental considerations: Select couplers that are suitable for the operating environment, such as temperature extremes, corrosive conditions, and exposure to dirt and debris.
By incorporating quick couplers into hydraulic systems, businesses can significantly enhance efficiency, reduce downtime, and improve overall productivity.
Hydraulic Ferrule Fittings
Hydraulic ferrule fittings are a common and crucial type of connection in hydraulic systems. They utilize a metal ferrule that is crimped or compressed onto the hose to create a strong and leak-proof seal.
How they work:
- A metal ferrule, typically made of steel or brass, is placed over the end of the hose.
- The fitting body is then threaded onto the hose and tightened using a wrench or specialized tool.
- As the fitting is tightened, the ferrule is drawn into the fitting body, compressing the hose and creating a tight seal.
- The compression also helps to prevent the hose from pulling out of the fitting.
Key Advantages:
- Reliable Sealing: Ferrule fittings provide a highly reliable seal, preventing leaks and ensuring the integrity of the hydraulic system.
- Durability: They are robust and can withstand high pressures and vibrations.
- Versatility: Available in a wide range of sizes and configurations to suit various applications.
- Ease of Installation: While proper installation techniques are essential, ferrule fittings are generally easier to install than some other types of fittings.
Applications:
- Widely used in various industrial, mobile, and marine applications.
- Found in construction equipment, agricultural machinery, and many other types of heavy-duty machinery.
- Used in high-pressure systems where reliability and leak-free performance are critical.
Proper Installation:
- It is crucial to follow the manufacturer‘s instructions carefully for proper installation.
- Using the correct tools and techniques is essential to ensure a secure and leak-free connection.
- Improper installation can lead to leaks, hose damage, and potential system failure.
Ferrule fittings are a vital component in many hydraulic systems, providing a reliable and efficient means of connecting hoses and ensuring the safe and effective operation of the equipment.
Hydraulic Banjo Fittings
Banjo fittings are a specialized type of hydraulic fitting designed for applications where space is limited or where a specific orientation is required. They feature a unique curved or angled body, resembling a banjo, which allows for flexible routing of the hydraulic hose.2
Key Characteristics:
- Unique Shape: The curved or angled body distinguishes banjo fittings from other types.3 This shape provides flexibility in hose routing, allowing for easier installation and better clearance in confined spaces.
- Two-Piece Design: Typically consist of two main parts:
- The Banjo Body: The curved or angled portion of the fitting.
- The Bolt: A hollow bolt that passes through the banjo body and connects to the hydraulic component.
- Washers: Often used to create a seal between the banjo body and the component.
Applications:
- Automotive: Widely used in automotive braking systems, steering systems, and fuel injection systems.
- Aerospace: Employed in aircraft hydraulic systems due to their compact size and ability to navigate tight spaces.
- Racing: Frequently used in high-performance racing vehicles where space is at a premium.
Advantages:
- Space-saving: Their unique shape allows for flexible routing and installation in confined spaces.
- Improved aesthetics: Can contribute to a cleaner and more aesthetically pleasing installation.
- Versatility: Available in a variety of sizes and configurations to suit different applications.
Disadvantages:
- Can be more complex to install: May require more precise alignment and tightening compared to some other types of fittings.
- Potential for leaks: If not installed correctly, leaks can occur at the banjo bolt or the washer interface.
Proper installation of banjo fittings is crucial to ensure leak-free performance and system reliability. It is important to use the correct washers, tighten the bolt to the specified torque, and ensure proper alignment of the components.
Hydraulic Grease Fitting
Hydraulic grease fittings, often referred to as “zerks,” are small, threaded components used to introduce grease into bearings, joints, and other components that require lubrication. They provide a convenient and controlled method for delivering grease to critical areas within a machine or system.
How they work:
- Connection Point: A grease fitting is threaded into a designated port on the component that needs lubrication.
- Grease Gun Connection: A grease gun is connected to the fitting.
- Grease Delivery: When the grease gun is operated, it forces grease through the fitting and into the internal components of the machine.
Key Features:
- Thread Types: Available in various thread sizes and styles to fit different applications. Common thread types include NPT (National Pipe Thread) and metric threads.
- Materials: Typically made from materials like steel, brass, or stainless steel, chosen for their strength, durability, and corrosion resistance.
- Angles: Available in various angles, such as straight, 90-degree, and 45-degree angles, to accommodate different installation requirements.
Importance:
- Essential for Proper Lubrication: Regular greasing is crucial for maintaining the proper operation of bearings, joints, and other moving parts within a hydraulic system.
- Reduces Wear and Tear: Proper lubrication reduces friction, wear, and tear, extending the life of components and improving overall system efficiency.
- Prevents Equipment Failure: Insufficient lubrication can lead to premature wear, overheating, and ultimately, equipment failure.
Regular Greasing Schedule:
- The frequency of greasing depends on factors such as the type of equipment, operating conditions, and the recommended intervals specified by the equipment manufacturer.
- Regular inspections and maintenance are essential to ensure proper lubrication and prevent equipment failures.
By incorporating grease fittings and adhering to a regular greasing schedule, you can significantly enhance the performance, reliability, and longevity of your hydraulic systems.
Hydraulic Camlock Fittings
Hydraulic camlock fittings are a type of quick-disconnect coupling that utilizes a cam mechanism for easy and secure connection and disconnection of hoses and pipes.
Key Features:
- Simple Operation: Connecting and disconnecting camlock fittings is typically accomplished with a single hand, making them ideal for applications where speed and efficiency are crucial.
- Secure Connection: The cam mechanism provides a strong and reliable seal, preventing leaks and spills.
- Versatility: Available in a wide range of sizes and configurations to suit various applications and flow rates.
- Durability: Constructed from durable materials such as aluminum, stainless steel, and brass, offering excellent resistance to corrosion and wear.
Applications:
- Industrial Applications: Widely used in various industries, including construction, agriculture, transportation, and manufacturing, for transferring liquids, powders, and gases.
- Firefighting: Used in firefighting equipment to quickly connect and disconnect hoses.
- Chemical Processing: Utilized in chemical plants for transferring various chemicals and fluids.
Types of Camlock Fittings:
- Type A: The most common type, featuring a male camlock with a groove that engages with a female camlock.
- Type B: A variation of Type A with a different cam design.
- Type C: Designed for high-pressure applications.
- Type D: A specialized type with a different locking mechanism.
Benefits:
- Improved efficiency: Significantly reduce the time required for connecting and disconnecting hoses.
- Enhanced safety: Minimize the risk of spills and leaks, improving workplace safety.
- Increased productivity: Faster connections and disconnections lead to increased productivity in various applications.
- Reduced maintenance: Durable construction minimizes the need for frequent repairs and replacements.
Camlock fittings are a valuable asset in many industries, offering a reliable and efficient solution for connecting and disconnecting hoses and pipes.
Hydraulic Test Fittings
Hydraulic test fittings are specialized components designed to facilitate the monitoring and diagnosis of hydraulic systems. They provide convenient access points for connecting pressure gauges, flow meters, and other testing equipment.
Key Functions:
- Pressure Measurement: Allow for accurate measurement of system pressure at various points, helping to identify potential pressure drops, blockages, or excessive pressure.
- Flow Rate Monitoring: Enable the measurement of fluid flow rates within the system, helping to identify potential restrictions or leaks.
- System Diagnosis: Assist in diagnosing system malfunctions, such as component failures, leaks, and contamination.
Types of Test Fittings:
- Test Ports: Permanently installed fittings that provide a dedicated access point for connecting testing equipment.
- Quick-Connect Couplings: Allow for rapid connection and disconnection of testing equipment, improving efficiency and reducing downtime.
- Gauge Adapters: Connect pressure gauges to the hydraulic system.
Benefits:
- Improved system maintenance: Enable proactive maintenance and troubleshooting, reducing downtime and repair costs.
- Enhanced safety: Allow for early detection of potential problems, minimizing the risk of system failure and ensuring safe operation.
- Increased efficiency: Streamline testing and diagnostic procedures, improving overall system efficiency.
Proper Selection and Installation:
- Compatibility: Choose test fittings that are compatible with the system’s operating pressure and fluid type.
- Accessibility: Select test points that are easily accessible for testing and maintenance.
- Installation: Install test fittings according to manufacturer‘s instructions to ensure proper function and prevent leaks.
By incorporating test fittings into the design and maintenance of hydraulic systems, engineers and technicians can ensure optimal system performance, improve safety, and minimize downtime.
Hydraulic Swivel Fittings
Hydraulic swivel fittings are a specialized type of connector that allows for rotation of the connected component without twisting or kinking the hose.1 This unique feature provides several significant advantages in various applications:
Key Features and Benefits:
- Flexibility: Swivel fittings enable movement and rotation of the connected component, preventing hose twisting and potential damage. This is crucial in applications where the connected component moves or rotates, such as in mobile equipment, construction machinery, and robotic systems.
- Reduced Hose Wear and Tear: By preventing hose twisting, swivel fittings significantly reduce the risk of hose abrasion, kinking, and internal damage, which can lead to premature hose failure.
- Improved System Life: By minimizing hose wear and tear, swivel fittings contribute to a longer service life for the entire hydraulic system, reducing maintenance costs and downtime.
- Enhanced Maneuverability: In applications where equipment needs to maneuver in tight spaces, swivel fittings provide increased flexibility and maneuverability.
Applications:
- Mobile Equipment: Widely used in construction equipment, agricultural machinery, and other mobile applications where equipment movement is frequent.
- Industrial Machinery: Employed in various industrial settings where components may rotate or move during operation.
- Aerospace: Utilized in aircraft and spacecraft where space is limited and movement is required.
- Robotics: Incorporated into robotic systems to allow for flexible and precise movement of robotic arms and other components.
Types of Swivel Fittings:
- Ball-bearing swivels: Utilize ball bearings to provide smooth and reliable rotation.
- High-pressure swivels: Designed for applications with high operating pressures.
- Plain bearing swivels: Offer a more economical option but may have slightly higher friction.
By incorporating swivel fittings into a hydraulic system, engineers and technicians can enhance system reliability, reduce maintenance costs, and improve overall system performance.
Hydraulic Fitting Type Chart
Hydraulic Fitting Type | Description | Applications |
---|---|---|
Hydraulic Straight | Connect components in a straight line | General use, connecting hoses and components |
Hydraulic Elbow | Change the direction of fluid flow (typically 90 degrees) | Routing fluid around obstacles, connecting components at angles |
Hydraulic Tee | Branch fluid flow into two directions | Distributing fluid to multiple components |
Hydraulic Cross | Connect four components at a single point | Complex branching configurations |
Hydraulic Reducer/Enlarger | Change the diameter of the fluid pathway | Transition between different hose or pipe sizes |
Hydraulic O-Ring Boss (ORB) | Utilize O-rings for sealing, providing a reliable and leak-free connection | Widely used in various applications due to their ease of assembly and disassembly |
Hydraulic Bulkhead | Pass through a wall or plate, allowing connections to be made from one side to the other | Limited access areas, marine applications, industrial machinery |
Hydraulic Swivel | Allow for rotation of the connected component without twisting or kinking the hose | Mobile equipment, machinery with moving parts |
Hydraulic Flare | Create a seal by flaring the end of the tubing against the fitting | Common in various applications, known for their reliability |
Hydraulic Compression | Create a seal by compressing a ferrule against the tubing | Reusable, easy to install, widely used in various applications |
Hydraulic Quick Disconnect | Allow for rapid connection and disconnection of components | Applications requiring frequent connections and disconnections (e.g., construction, agriculture) |
Hydraulic Push Lock | Simple push-to-connect mechanism for easy installation and removal | Mobile hydraulics, applications where frequent connections are necessary |
Hydraulic Hose Barb | Have a barbed end that is inserted into the hose and secured with a clamp | Low-pressure applications, often used with rubber hoses |
Hydraulic Banjo | Feature a curved or angled body for flexible hose routing | Applications with space constraints, automotive, aerospace |
Hydraulic Flange | Utilize a bolted flange connection for high-pressure and large-diameter applications | Heavy-duty industrial machinery, large-scale hydraulic presses |
Hydraulic Plugs & Caps | Seal off unused ports or openings in a hydraulic system | Prevent leaks, contamination, and protect components |
Hydraulic Adapter | Connect components with different thread sizes or types | Bridge the gap between incompatible connections |
Hydraulic Grease Fitting | Allow for the introduction of grease into bearings and other components | Essential for maintaining proper lubrication and preventing wear and tear |
Conclusion
Choosing the right hydraulic fittings is crucial for the success of any hydraulic project. By understanding the different types of fittings available and their specific applications, you can select the most suitable components for your system. Factors such as pressure, temperature, fluid compatibility, and ease of installation should all be carefully considered when making your selection.
Ready to source high-quality hydraulic hose fittings for your next project? Explore our extensive inventory of wholesale hydraulic fittings on our hydraulic fitting manufacturer.
We offer a wide range of options to suit various applications and budgets. Contact us today for a free consultation and let our experienced team assist you in finding the perfect fittings for your specific needs.