Hydraulic fittings are the connective tissue of any hydraulic system, responsible for joining components, controlling fluid flow, and withstanding immense pressures.
This guide will provide an in-depth technical overview of various fitting types, including their construction, materials, and performance characteristics. We will also discuss critical considerations such as compatibility, installation techniques, and maintenance best practices.
What Are Hydraulic Fittings
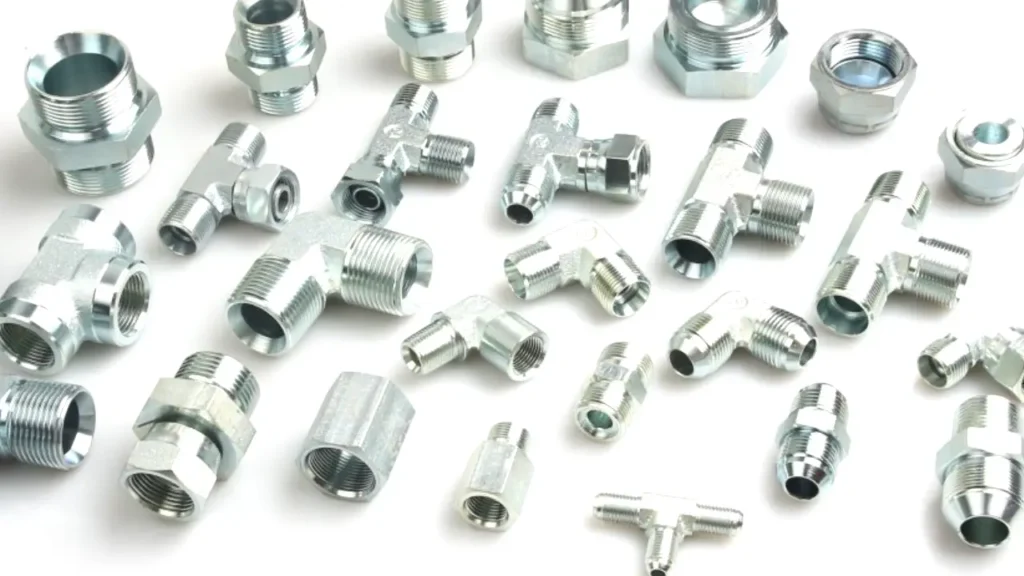
Hydraulic fittings are essential components in any hydraulic system. They serve as the crucial connectors that link various parts together, ensuring the smooth and uninterrupted flow of hydraulic fluid.
Hydraulic Fitting Material
The choice of material for hydraulic fittings is crucial for their performance, durability, and suitability in different applications. Here’s a breakdown of common materials:
1. Steel:
- Most common: Offers a good balance of strength, durability, and cost-effectiveness.
- Suitable for: High-pressure applications and general-purpose use.
- Types:
- Carbon Steel: A standard option, readily available and relatively affordable.
- Alloy Steel: Offers enhanced strength and resistance to wear and tear.
2. Stainless Steel:
- Excellent corrosion resistance: Ideal for applications exposed to harsh environments, such as marine or chemical processing.
- High strength: Suitable for high-pressure systems.
- More expensive: Compared to carbon steel.
- Types:
- 304 Stainless Steel: A common grade with good corrosion resistance.
- 316 Stainless Steel: Offers superior corrosion resistance, particularly in chloride-containing environments.
3. Brass:
- Good corrosion resistance: Suitable for many applications.
- Excellent machinability: Easy to work with.
- Lower strength: Compared to steel, may not be suitable for extremely high-pressure applications.
4. Aluminum:
- Lightweight: Ideal for applications where weight reduction is critical, such as aerospace.
- Good corrosion resistance: Offers good performance in many environments.
- Lower strength: Compared to steel, may not be suitable for all applications.
5. Plastic (e.g., Nylon, PTFE):
- Lightweight and corrosion-resistant: Suitable for certain low-pressure applications.
- Limited pressure and temperature capabilities: Not suitable for high-pressure or high-temperature systems.
Factors influencing material selection:
- Operating pressure and temperature: The chosen material must be able to withstand the pressures and temperatures encountered in the hydraulic system.
- Fluid compatibility: The material should be compatible with the hydraulic fluid used (e.g., resistance to corrosion, swelling, or degradation).
- Environmental conditions: Factors like exposure to moisture, chemicals, or extreme temperatures will influence material choice.
- Cost: The cost of the material is an important consideration.
By carefully selecting the appropriate material for hydraulic fittings, you can ensure system reliability, safety, and longevity.
Material | Strength | Corrosion Resistance | Cost | Weight | Applications |
---|---|---|---|---|---|
Steel | High | Moderate | Low | High | General purpose, high-pressure systems |
Stainless Steel | High | Excellent | High | High | Harsh environments, marine applications |
Brass | Moderate | Good | Moderate | Moderate | Plumbing, low-pressure hydraulics |
Aluminum | Moderate | Good | Moderate | Low | Aerospace, weight-sensitive applications |
Plastic | Low | Excellent | Low | Very Low | Low-pressure, non-critical applications |
By carefully selecting the right material for hydraulic fittings, you can ensure system reliability, safety, and longevity.
What Are the Different Hydraulic Fittings
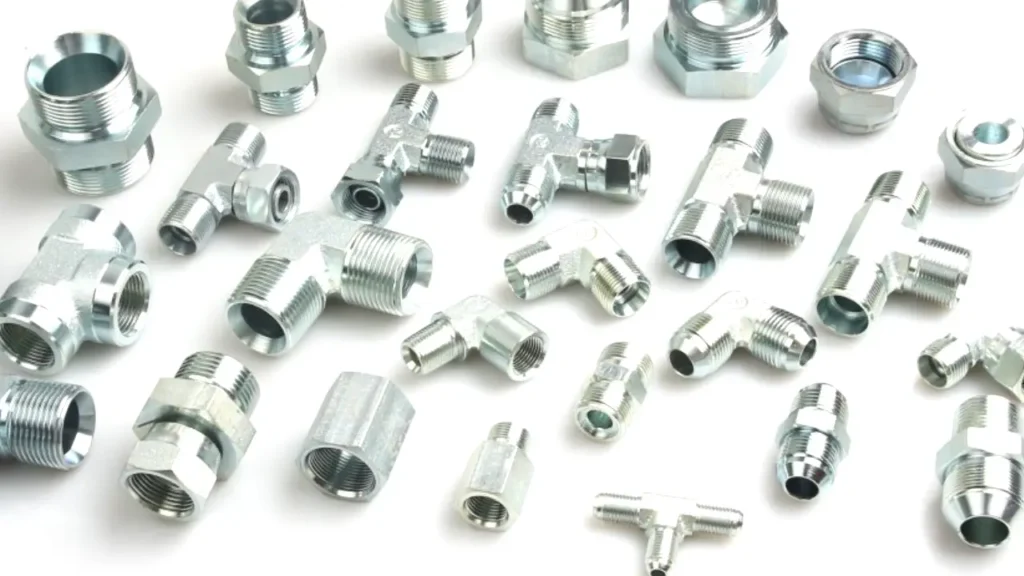
What are the different types of hydraulic fittings?
Hydraulic fittings are the critical connectors in a hydraulic system, ensuring the safe and efficient transfer of fluid power. They come in a wide variety of shapes, sizes, and configurations, each designed for specific applications and purposes.
Here’s a deeper look into some of the most common hydraulic fitting types:
1. Straight Fittings:
- Purpose: Connect components in a straight line.
- Types:
- Male: Have an external thread.
- Female: Have an internal thread.
- Nipples: Short, straight fittings with both male and female ends.
2. Elbow Fittings:
- Purpose: Change the direction of fluid flow, typically by 90 degrees.
- Types:
- 90-degree elbows: The most common type.
- 45-degree elbows: Provide a gentler change in direction.
3. Tee Fittings:
- Purpose: Allow fluid to branch off in two directions.
- Applications: Widely used in distribution and branching points within a hydraulic system.
4. Cross Fittings:
- Purpose: Connect four different components at a single point.
- Applications: Used in complex configurations where multiple connections are required.
5. Reducer/Enlarger Fittings:
- Purpose: Change the diameter of the fluid pathway.
- Applications: Used to transition between different hose or pipe sizes.
6. O-Ring Boss (ORB) Fittings:
- Purpose: Utilize O-rings for sealing, providing a reliable and leak-free connection.
- Advantages: Easy to assemble and disassemble, reusable.
7. Bulkhead Fittings:
- Purpose: Designed to pass through a wall or plate, allowing connections to be made from one side to the other.
- Applications: Often used in machinery and equipment where access to the interior is limited.
8. Swivel Fittings:
- Purpose: Allow for rotation of the connected component without twisting or kinking the hose.
- Applications: Useful in applications where movement is required, such as on mobile equipment.
9. Flare Fittings:
- Purpose: Create a seal by flaring the end of the tubing against the fitting.
- Types:
- 37-degree flare: Common in North American applications.
- 45-degree flare: Common in European applications.
10. Compression Fittings:
- Purpose: Create a seal by compressing a ferrule against the tubing.
- Advantages: Reusable and relatively easy to install.
11. Quick-Disconnect Fittings:
- Purpose: Allow for rapid connection and disconnection of components.
- Applications: Widely used in applications where frequent connections and disconnections are necessary.
Factors to Consider When Selecting Fittings:
- Pressure and temperature requirements: The fitting must be able to withstand the operating conditions of the system.
- Fluid compatibility: The fitting material must be compatible with the hydraulic fluid.
- Space constraints: The size and shape of the fitting must be appropriate for the available space.
- Ease of installation and maintenance: The fitting should be easy to install, disassemble, and maintain.
- Cost: The cost of the fitting should be considered within the overall system budget.
This is not an exhaustive list of hydraulic fittings, as there are many specialized fittings available for specific applications.
Always refer to the manufacturer‘s recommendations and consult with a qualified hydraulic engineer for proper fitting selection and installation.
Fitting Type | Description | Applications |
---|---|---|
Straight | Connect components in a straight line | General use |
Elbow | Change the direction of fluid flow | Various applications |
Tee | Branch fluid flow in two directions | Distribution points |
Cross | Connect four components at a single point | Complex configurations |
Reducer/Enlarger | Change the diameter of the fluid pathway | Transition between different sizes |
O-Ring Boss (ORB) | Utilize O-rings for sealing | Reliable and leak-free connections |
Bulkhead | Pass through a wall or plate | Limited access areas |
Swivel | Allow for rotation of the connected component | Applications with movement |
Flare | Create a seal by flaring the tubing | Common in various applications |
Compression | Create a seal by compressing a ferrule | Reusable, easy to install |
Quick-Disconnect | Allow for rapid connection and disconnection | Frequent connections and disconnections |
By understanding the different types of hydraulic fittings and their applications, you can make informed decisions to ensure the optimal performance and reliability of your hydraulic systems.
Conclusion:
In conclusion, understanding hydraulic fittings is paramount for the safe and efficient operation of any hydraulic system. By selecting the right fittings for your specific application, you can minimize leaks, prevent damage, and optimize overall system performance.
Ready to upgrade your hydraulic system with high-quality fittings? Explore our extensive selection of wholesale hydraulic fittings. We offer a wide range of options to suit various applications and budgets. Contact us today for a free consultation and let us help you find the perfect solution for your needs.