Banjo fittings are integral components in various hydraulic, automotive, and industrial systems. These fittings are unique for their compact design, which allows fluid transfer in tight spaces.
In this article, we’ll dive deep into what is a banjo fitting, its components, working principles, and how to select the right fitting for your needs.
If you have any questions or need further clarification on banjo fittings, feel free to contact us.
What is a Banjo Fitting: Overview and Applications

What Are Banjo Fittings Components?
Banjo fittings are specialized components used to connect fluid lines in applications where space is limited, and a secure, leak-proof connection is essential. These fittings consist of a banjo bolt that threads through a fitting body and connects to a component, such as a valve, manifold, or pipe. The fluid flows through the hollow center of the bolt, and the banjo fitting body directs the fluid to the desired location.
Parts of a Banjo Fitting
Banjo fittings are made up of several key parts:
- Banjo Bolt: The threaded bolt that passes through the fitting body.
- Banjo Fitting Body: The hollow body that accommodates the bolt and directs fluid flow.
- Banjo Gasket: A sealing washer placed between the fitting and the component to ensure a leak-proof connection.
- Banjo Clamp: Sometimes used to secure the fitting in place and prevent movement.
These parts work together to create a reliable, high-performance connection.
Banjo fittings are designed to connect hoses, pipes, or tubes in a way that allows fluid to flow while minimizing the use of space. These fittings are widely used in hydraulic systems, automotive fuel lines, and industrial machinery.
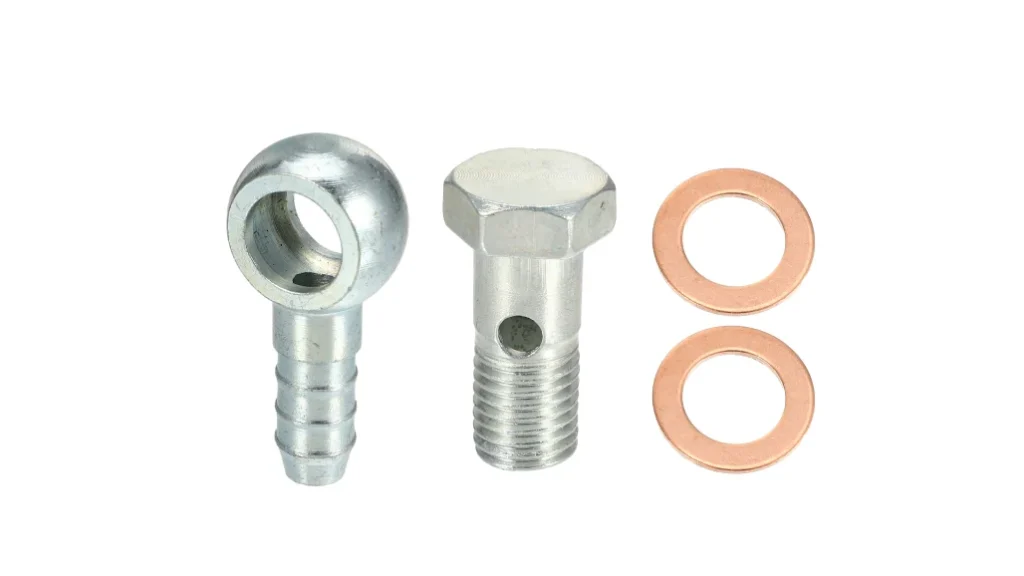
Key Features of Banjo Fittings
Banjo fittings are chosen for their versatility, durability, and compact design. They offer several distinct features that make them ideal for various applications.
1. Compact Design
One of the key features of banjo fittings is their space-saving design. The L-shaped or T-shaped configuration allows them to be used in areas with limited space, which is particularly useful in automotive and machinery applications.
2. Leak-Proof Connection
Banjo fittings are designed to provide a secure, leak-proof connection. The banjo gasket or sealing washer placed around the fitting ensures that no fluid escapes under pressure, making them ideal for high-pressure hydraulic systems.
3. Easy Installation
Banjo fittings are relatively easy to install, especially when compared to other types of fittings that require more space or specialized tools. Their design allows for a straightforward connection process, making them convenient in both manufacturing and repair scenarios.
4. Durability and Strength
Banjo fittings are typically made from high-strength materials, such as stainless steel or brass, which can withstand the stresses of high-pressure fluid systems. They are also corrosion-resistant, ensuring longevity even in harsh environments.
5. Versatility
Banjo fittings are available in a variety of sizes, materials, and configurations to suit different fluid types, pressures, and temperatures. This versatility makes them an essential component in automotive, hydraulic, fuel line, and industrial applications.
Key Applications of Banjo Fittings
- Automotive Systems: Banjo fittings are commonly used in fuel lines, brake systems, and power steering systems, where they ensure a tight, leak-free connection.
- Hydraulic Equipment: In hydraulic systems, banjo fittings are used to connect pipes and hoses in tight spots, where standard fittings might not fit.
- Fuel Lines: Banjo fittings are often used in fuel systems due to their ability to create a reliable seal and minimize leakage under pressure.
- Industrial Machinery: In industries that use high-pressure fluid systems, banjo fittings are ideal for managing fluid flow efficiently.
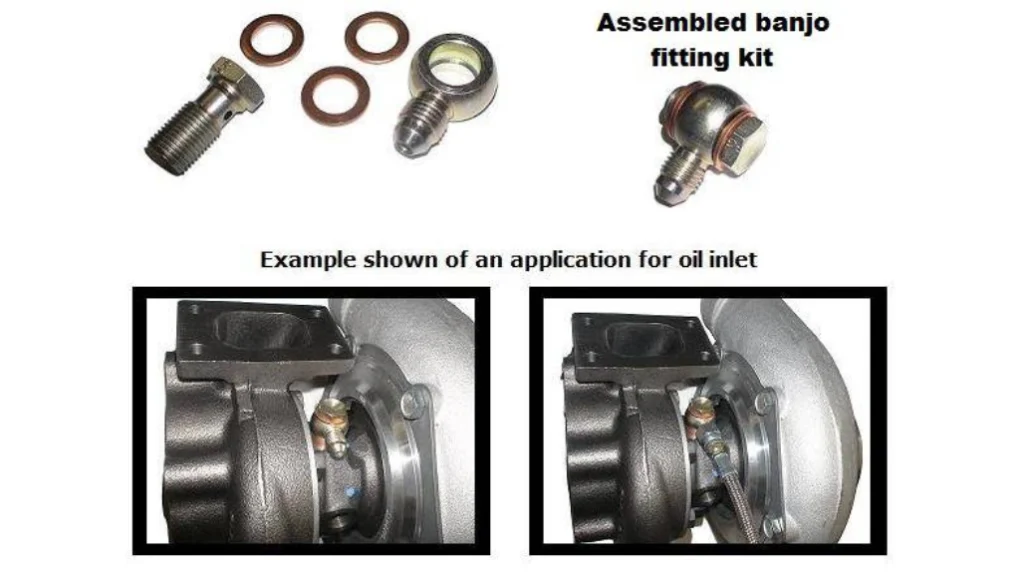
How Does a Banjo Fitting Work?
Banjo fittings are composed of several parts that together form a reliable connection. The main components include the banjo fitting body, banjo bolt, sealing washers, and sometimes, the banjo clamp.
The Working Principle of Banjo Fittings
Banjo fittings work by creating a secure connection between a hose or pipe and a component, such as a valve or cylinder. The banjo bolt threads through the fitting body and connects to the piece that banjo fitting threads onto — usually a component with a threaded hole, such as a manifold or valve.
The fitting body itself is often shaped like an L or T, which allows the hose to be connected in a way that can accommodate tight spaces. The banjo gasket or sealing washer is placed between the fitting and the component it connects to, ensuring a leak-proof seal under high pressure.
Fluid Flow in Banjo Fittings
The unique design of the banjo fitting allows fluid to flow through the hollow center of the banjo bolt. As the banjo bolt passes through the fitting, it ensures fluid can flow freely from one side of the connection to the other. The fluid flows through the fitting body and exits through the open port, which is often positioned at a right angle to the hose or pipe, making it ideal for tight or complex installations.
Banjo Fitting Sizes and Types
Banjo fittings come in a wide range of sizes and types to suit various applications. When choosing a banjo fitting, it’s important to consider the following:
Hose Size: The size of the hose or pipe being used will influence the selection of the banjo fitting. Choose a fitting that is compatible with the hose size to ensure a secure connection.
Thread Size: Ensure the banjo fitting has the correct thread size to match the component it’s being connected to.
Material: Banjo fittings can be made from different materials, including stainless steel, brass, and aluminum. The material should be chosen based on the fluid being transported and the pressure requirements.
What is the Piece That Banjo Fitting Threads Onto?

When working with banjo bolt fittings, it’s crucial to understand what the banjo bolt threads onto. The piece that banjo fitting threads onto is usually a component with a threaded hole, such as a banjo pipe fitting or a banjo clamp. This part is often located on the manifold, fuel line, or valve to which the banjo fitting is attached.
Common Pieces for Banjo Bolt Threads
- Banjo Pipe Fittings: These are specialized fittings that allow the connection of a banjo fitting to a pipe or hose.
- Banjo Clamps: In some cases, a banjo clamp is used to secure the fitting and prevent any movement that could lead to leaks.
- Manifolds and Valves: The fitting may thread directly onto a manifold or valve, allowing fluid to flow through the system.
The threaded hole on these components is designed to accommodate the banjo bolt, creating a secure connection. It’s important to select the correct size and material for the piece that the banjo fitting threads onto, as this ensures the fitting remains leak-proof and durable.
How to Select the Right Banjo Fitting
Selecting the right banjo fitting involves several key considerations. Here’s a step-by-step guide to ensure you choose the best fitting for your application.
Step 1: Assess the System’s Fluid Type
The first step in selecting a banjo fitting is to identify the type of fluid it will carry. Different fluids (such as oil, water, or hydraulic fluid) require different sealing materials and pressure ratings.
Step 2: Measure the Required Fitting Size
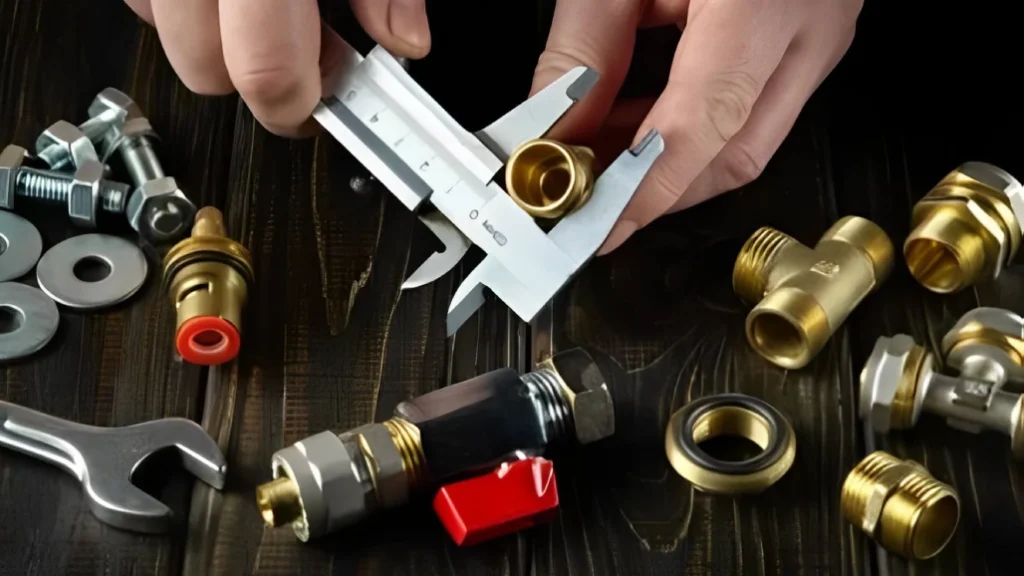
Banjo fittings come in various sizes, and selecting the correct size is crucial to ensuring a secure and leak-proof connection. To accurately measure the size, you’ll need to check the pipe or hose diameter and match it with the appropriate fitting.
Step 3: Check the Thread Type and Pitch
Banjo fittings come with various thread types, including NPT (National Pipe Thread) and BSP (British Standard Pipe). Make sure you choose a fitting with the correct thread type for your system.
Step 4: Evaluate Pressure and Temperature Requirements
Banjo fittings need to withstand the pressure and temperature ranges of the system. Consider the maximum operating pressure and temperature of your system to ensure the fitting’s material and design are suitable.
Step 5: Choose the Material
Banjo fittings are available in various materials, including stainless steel, brass, and aluminum. The material you select should depend on the environmental conditions, such as exposure to corrosion, pressure requirements, and temperature.
Common Mistakes to Avoid When Choosing Banjo Fittings
Choosing the right banjo fitting can be tricky, and making the wrong choice could result in leaks, system failures, or maintenance issues. Here are some common mistakes to avoid:
- Incorrect Size: Selecting a fitting that doesn’t match the size of your hose or pipe can result in leaks or weak connections.
- Ignoring Pressure Ratings: Always check the pressure ratings of your banjo fitting. Using a fitting not rated for the pressure in your system can cause catastrophic failure.
- Overlooking the Material: Banjo fittings come in a variety of materials, and using the wrong material can result in corrosion or failure. Be sure to select one that matches the fluid type and environmental conditions.
Conclusion
Banjo fittings are indispensable components in a wide range of systems, from automotive to industrial applications. By understanding their design, types, and how to choose the right fitting for your needs, you can ensure a reliable and efficient fluid connection.
If you’re interested in exploring our range of banjo fittings or need assistance with selecting the perfect one for your system, feel free to visit our homepage or contact us directly for more information.
FAQs About What is a Banjo Fitting
Can I use banjo fittings for fuel lines?
Yes, banjo fittings are commonly used in fuel lines, particularly in automotive applications, due to their ability to create a tight, leak – proof connection in space – constrained areas. In automotive fuel systems, space is often at a premium, especially in the engine compartment. Banjo fittings are designed in a way that they can be easily installed in tight spaces where other types of connectors may not fit.
Their compact design allows for efficient routing of fuel lines. Moreover, the ability to create a leak – proof connection is of utmost importance in fuel systems. Any fuel leakage can be extremely dangerous, as fuel is highly flammable.
The banjo bolt, when tightened correctly, compresses the banjo gasket (a crucial component for sealing) between the banjo fitting body and the mating component, ensuring that no fuel can escape. This makes banjo fittings a reliable choice for fuel line connections in cars, trucks, and other vehicles.
How do I measure a banjo fitting?
To measure a banjo fitting, check the thread size, hose size, and the overall length of the bolt to ensure compatibility with your system. The thread size of the banjo bolt is critical as it must match the internal threads of the component it will be screwed into. This is usually measured in terms of the diameter and the pitch of the threads.
For example, in a metric system, it could be something like M10x1.5, where M10 represents the diameter and 1.5 represents the pitch. The hose size is important as it determines the compatibility with the hoses that will be connected to the banjo fitting. This is typically measured in terms of the inner diameter of the hose.
If the hose size is not correct, it can lead to issues such as poor flow or a loose connection. The overall length of the bolt is also significant. It needs to be long enough to pass through the banjo fitting body and the mating component and still have enough threads to be properly tightened. Measuring these aspects accurately is essential for a successful installation and proper functioning of the system.
What materials are banjo fittings made from?
Banjo fittings are typically made from materials like stainless steel, brass, and aluminum, which are resistant to corrosion and capable of withstanding high – pressure systems. Stainless steel is a popular choice due to its excellent corrosion resistance properties.
In environments where the fitting may be exposed to moisture, chemicals, or harsh weather conditions, stainless steel can maintain its integrity over time. It also has high strength, allowing it to withstand the pressures present in hydraulic and industrial systems. Brass is another common material.
It has good corrosion resistance, especially in certain chemical environments, and is relatively easy to machine. This makes it suitable for applications where precise threading and shaping of the fitting are required. Aluminum is lightweight, which can be an advantage in applications where weight reduction is a priority, such as in some automotive or aerospace systems. Despite being lightweight, it still has sufficient strength to handle the pressures in many systems. Additionally, it can be treated with various coatings to enhance its corrosion resistance.
How to install banjo fittings correctly?
First, hand – screw the threaded part of the fitting into the corresponding component. Then, place the ferrule on the tube or pipe to be connected. Next, insert the tube or pipe with the ferrule into the threaded end of the fitting.
Finally, use a wrench to tighten the fitting nut, causing the ferrule to deform under pressure, thus creating a tight seal between the tube and the fitting. When installing, it should be noted to avoid over – tightening, so as not to damage the ferrule or the threads.
What are the maintenance key points of banjo fittings?
Regularly inspect banjo fittings to check for signs of damage, wear, or leakage, especially pay attention to parts such as seals, O – rings, and threads. Use appropriate cleaning solutions and tools to remove accumulated dirt, debris, and other contaminants, but avoid using strong corrosive chemicals that may damage the fittings.
According to the manufacturer’s recommendations, select suitable lubricants and apply them to the threads and seals to reduce friction and extend the service life. When storing, place them in a clean, dry environment free from corrosive substances and extreme temperatures, preferably in a protective box or container.