When it comes to managing fluid flow in piping systems, what fitting changes pipe direction is a common question. Pipe fittings are essential components in any piping network, designed to connect, control, and change the direction of pipes.
These fittings play a critical role in ensuring the system functions properly, whether it’s in industrial, residential, or commercial settings. Let’s delve into the different types of pipe fittings that alter the direction of flow, their manufacturing process, and their proper applications.
All Types : What Fitting Changes Pipe Direction?
There are several pipe fittings used to change the direction of pipes. These fittings come in various shapes and sizes, each tailored for specific applications.
Below are the main types of fittings that change pipe direction:
Elbows (90° and 45°)
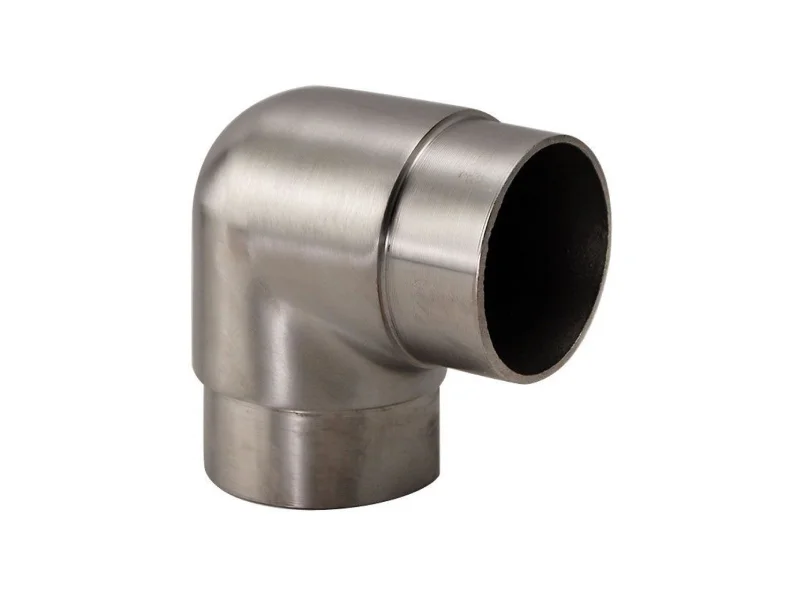
Elbows are among the most commonly used fittings to change the direction of pipe flow. They typically come in 90° and 45° angles, allowing for sharp or moderate directional changes. Elbows are used in both residential and industrial plumbing systems, as well as in various fluid and gas transport systems.
Application:
Elbows are not only used in situations where space is not a limiting factor, but they also play a critical role in the design of piping systems that require tight turns or gradual bends to accommodate equipment layout or building structure.
In industrial settings, elbows are utilized in high-pressure systems such as oil and gas pipelines, chemical processing plants, and power generation facilities. In residential applications, elbows are commonly found in heating systems, air conditioning units, and water supply lines. They can be fabricated from materials like steel, copper, PVC, and others, depending on the requirements of the system’s operating conditions.
Tees (T-Fittings)
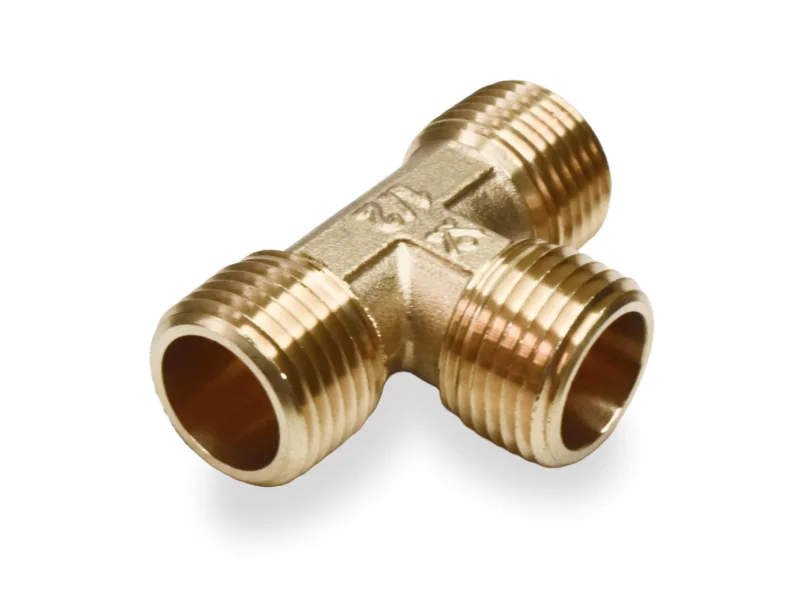
A tee fitting allows a pipe to split into two directions at a right angle, changing the flow direction. It’s primarily used when you need to connect a branch pipe to a main pipeline.
Application:
Tees are essential components in any piping network that requires fluid distribution or collection. In addition to plumbing and fire suppression systems, tees are used in HVAC systems for airflow management, in process industries for diverting flow or mixing fluids, and in sewage systems for combining multiple waste flows into one main line.
The versatility of tees allows them to be used with different types of pipes, including metallic and non-metallic conduits, making them indispensable in both new construction and renovation projects.
Cross Fittings
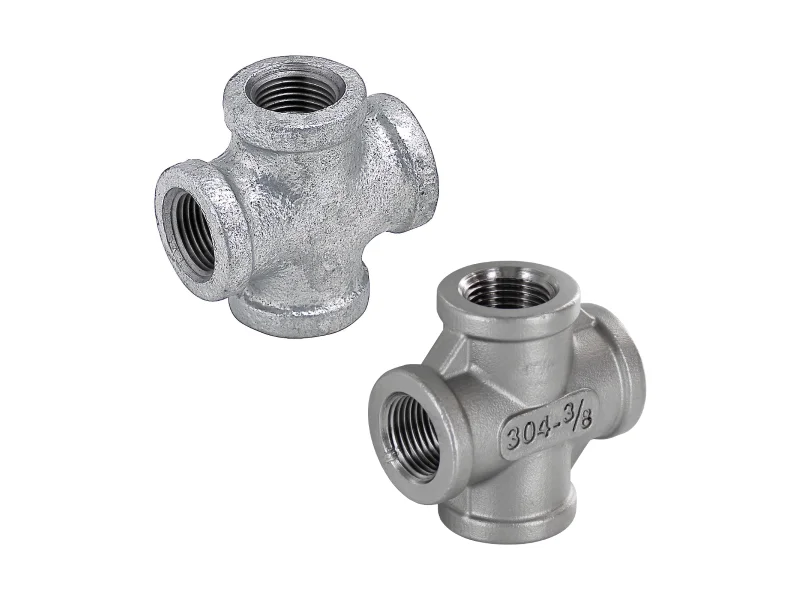
Cross fittings are similar to tees but are designed to split the pipeline into four directions. It’s a less common fitting compared to tees but is used in specific applications requiring multi-directional flow.
Application:
Cross fittings find their niche in complex piping networks that demand multi-directional flow capabilities within a confined space. They are frequently used in the installation of sprinkler systems, where each cross fitting can serve four separate sprinklers or branches.
In industrial applications, cross fittings may be employed in cooling systems, lubrication networks, and other scenarios where fluid must be distributed to several points simultaneously. Due to the stress concentration at the intersection points, cross fittings are typically reserved for low-pressure applications unless specifically designed for higher pressures.
Elbow Tees
These are a combination of an elbow and a tee fitting, allowing the pipe to both change direction and branch off simultaneously.
Application:
Elbow tees are specialized fittings used in advanced industrial configurations, such as petrochemical plants and refineries, where compactness and efficiency are paramount. These fittings allow for the redirection of flow while also branching off, which can significantly reduce the number of individual fittings required in a system.
This can lead to cost savings, reduced installation time, and fewer potential leak points. Additionally, elbow tees can help streamline maintenance by consolidating connections into a single component.
Reducers
While primarily used to change the size of pipes, reducers can also help change direction in a system by creating a smoother transition from one diameter to another.
Application:
Reducers are vital in systems that require a change in pipe diameter to adjust flow rates or pressure levels. They are commonly used in steam and hot water systems to maintain efficient heat transfer, in pumping stations to match pump outlet sizes with pipeline diameters, and in pneumatic systems to control air pressure.
By providing a smooth transition between different pipe sizes, reducers minimize turbulence and friction loss, contributing to overall system efficiency. They are also important in ensuring proper sealing and minimizing the risk of leaks when connecting dissimilar sized pipes.
Manufacturing Process of Pipe Fittings
The manufacturing of pipe fittings is a sophisticated process that ensures the final product is durable, precise, and capable of handling the pressures and conditions of the system they’re intended for. Below are the key stages involved in manufacturing pipe fittings:
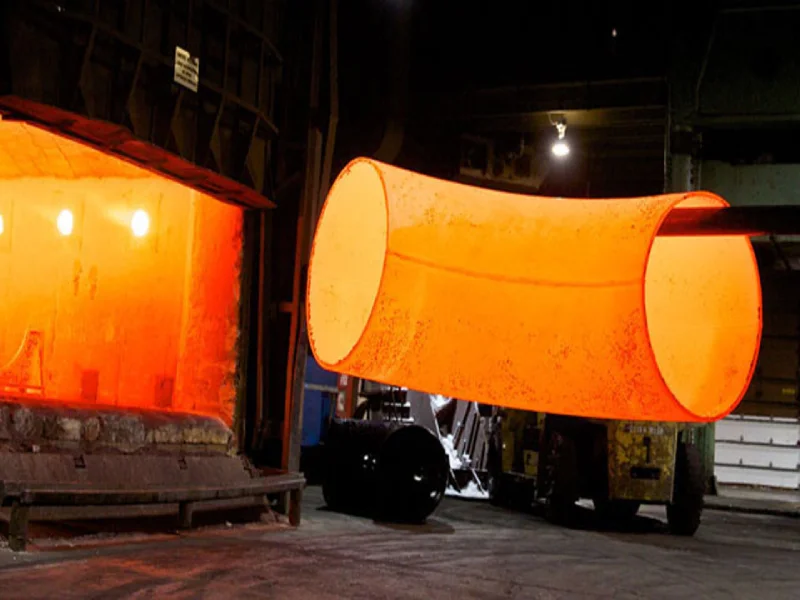
Material Selection
- Description: The material used for pipe fittings depends on the specific application. Common materials include stainless steel, carbon steel, copper, brass, and PVC. Stainless steel, for example, is often used for industrial applications where corrosion resistance is crucial.
- Process Insight: Materials are chosen based on factors like fluid type, pressure requirements, temperature, and environmental conditions.
Casting or Forging
- Description: Pipe fittings are typically either cast or forged. Casting involves pouring molten metal into molds, while forging involves shaping metal under high heat and pressure.
- Process Insight: Forged fittings are stronger and can withstand higher pressure, while cast fittings are more cost-effective but may not be as durable.
Machining
- Description: Once the fitting has been cast or forged, it’s sent through a machining process to refine the shape, drill holes for threading, and ensure the fitting’s dimensions are precise.
- Process Insight: Machining is a critical step to ensure the fitting’s ability to connect securely to other components without leaks.
Testing
- Description: Quality control is paramount in pipe fitting manufacturing. The fittings undergo pressure testing, leak testing, and stress testing to ensure they meet industry standards.
- Process Insight: Test pressures are usually higher than operational limits to ensure the fittings can withstand extreme conditions.
Pipe Fitting Process and Installation
Preparing the Pipes
Before starting any installation, it’s essential to prepare the pipes properly. This step ensures that the fittings will be installed securely, preventing future leaks or system failures. The preparation process involves cleaning the pipe ends to remove dirt, debris, and any rough edges. Using a pipe cleaner or cloth to wipe the surfaces can help maintain the integrity of the connection.
If any burrs or sharp edges are present, they should be filed down to avoid damaging the fitting or causing issues when connecting. Clean and smooth pipes guarantee a better, tighter seal between the pipe and the fitting, thus reducing the risk of leaks.
Selecting the Correct Fitting
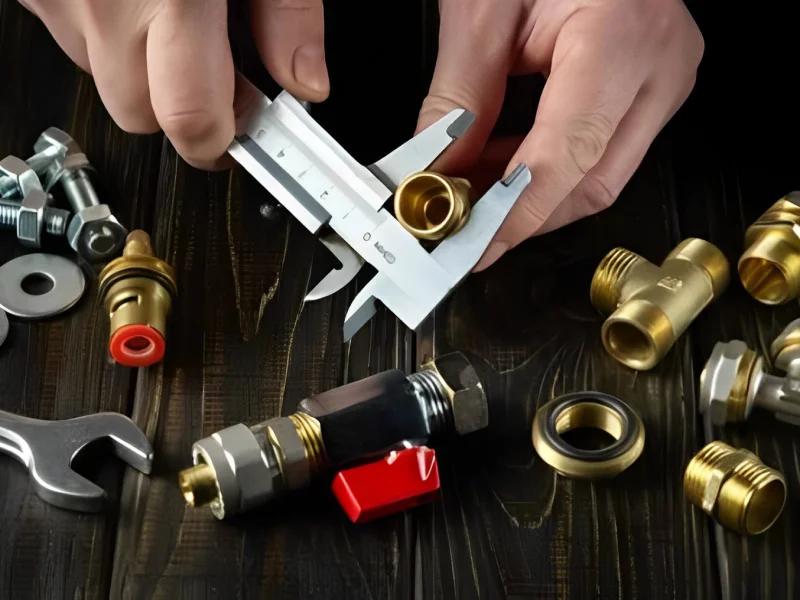
Choosing the right fitting is the next crucial step in the process. The type of fitting depends on the angle and direction change required in the system. For instance, a 90-degree elbow fitting is ideal for sharp turns in the pipe direction, while a 45-degree elbow is better suited for less acute changes. When branching pipes, a tee fitting is typically used.
For transitions between different pipe sizes, reducers or bushings are the preferred options. It’s important to consider factors like pipe diameter, material, and system pressure when selecting the correct fitting. Using the wrong type of fitting may cause leakage, poor flow, or even system failure.
Installing the Fitting
Once you have the right fitting and prepared pipes, installation can begin. For threaded connections, apply PTFE (Teflon) tape or thread sealant to the threads to ensure a tight seal and prevent leaks. This is particularly important in high-pressure systems where even small leaks can cause major issues.
After applying the sealant, use the appropriate tools, such as a pipe wrench, to secure the fitting onto the pipe. It’s essential to not overtighten the fitting, as this can damage the threads or cause stress fractures, especially on plastic pipes or fittings. Tighten it just enough to create a firm, leak-proof connection.
Testing the System After Installation
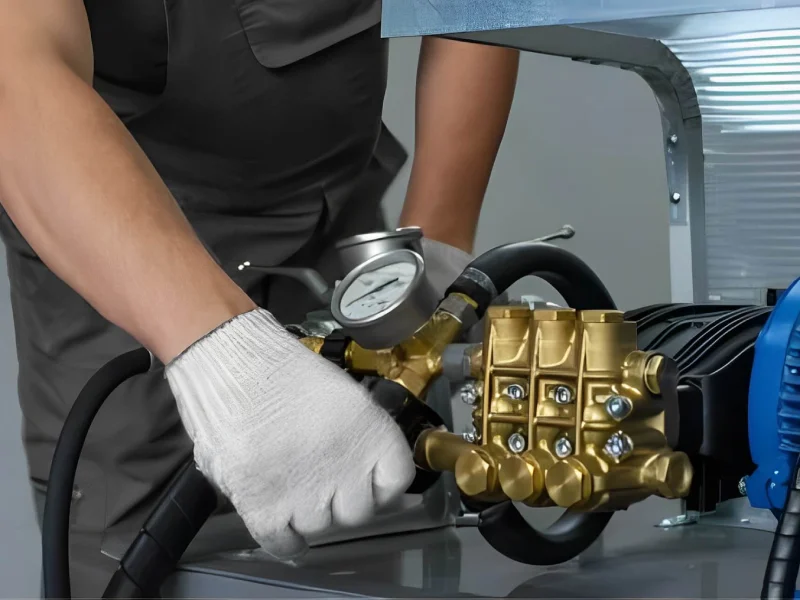
Once the fittings are installed, the next step is to test the system to ensure everything is functioning as expected. Pressurize the piping system slowly to check for any signs of leaks. If the system is under high pressure, perform a pressure test to verify that all fittings can handle the required load without compromising the structure.
The pressure test should be carried out in accordance with the manufacturer’s guidelines or industry standards. If any leaks are detected, identify the source and re-tighten or replace the fitting as necessary. Ensuring that the system is leak-free before it’s put into full operation is crucial for the longevity of the installation.
Sealing and Securing the Fittings
For some applications, additional sealing may be required, especially in outdoor or high-pressure systems. After tightening the fittings, you can apply additional sealant or wrap the joints with specialized tape for extra security. In some cases, securing the fittings with clamps or brackets may be necessary, particularly for larger pipe sizes or in systems subject to vibration.
This helps prevent any movement or strain on the connections that could lead to loosening or leaks over time.
Final Inspection and Maintenance
The final step involves conducting a thorough inspection of the entire piping system. Check all joints, connections, and fittings to ensure that everything is securely in place. It’s also essential to inspect the fittings for signs of wear, corrosion, or damage that could compromise the system’s integrity.
Regular maintenance should be scheduled to check for any signs of leaks or pressure loss. If any fittings are found to be faulty or damaged, they should be replaced immediately to avoid any disruptions in service or safety hazards.
Common Applications of Fittings That Change Pipe Direction
Residential Plumbing Systems
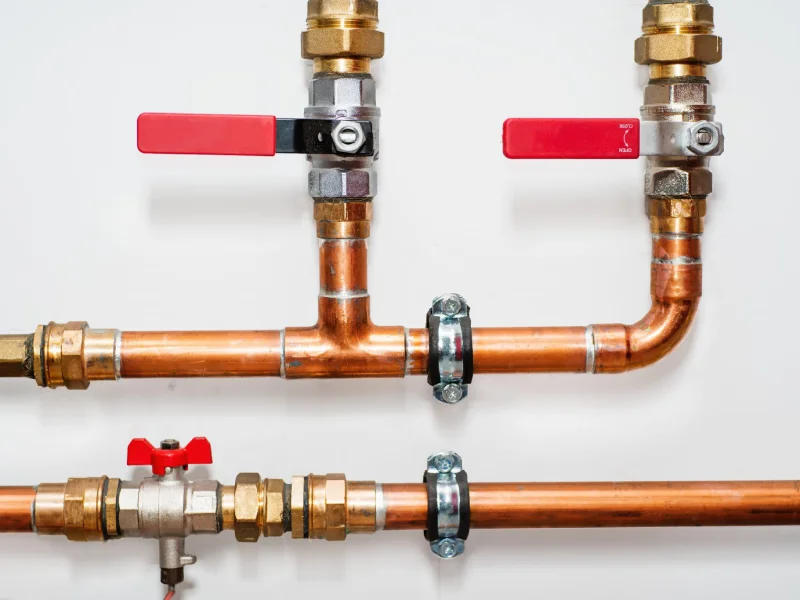
In residential plumbing systems, pipe fittings that change direction are used to guide water from the main supply to various fixtures, such as sinks, showers, and toilets. These fittings, such as elbows and tees, are essential for navigating pipes around walls, corners, and obstacles.
For example, a 90-degree elbow fitting is often used to change the direction of pipes under sinks or behind walls, while a tee fitting is used to branch off water supply lines to different fixtures. These fittings ensure that the plumbing system functions efficiently, delivering water to all parts of the home.
Industrial Fluid Systems
In industrial fluid systems, fittings are used to direct the flow of liquids or gases through complex pipelines. These systems often operate under high pressures, which require durable fittings capable of withstanding extreme conditions. Elbows, tees, and reducers are frequently used to direct the flow of oil, gas, or chemicals through pipelines.
For example, a 90-degree elbow may be used to change the direction of a fluid flow through a pipeline in a refinery or chemical plant. Tees are used to branch the fluid flow into different directions to supply various processing units. The ability to control and direct fluid flow efficiently is critical to maintaining system pressure, preventing leaks, and ensuring smooth operation.
HVAC Systems
In heating, ventilation, and air conditioning (HVAC) systems, fittings are used to redirect air or refrigerants through ducts and coils. These fittings help to direct the flow of conditioned air to different rooms or parts of the building.
For example, elbows are commonly used to navigate air ducts around corners, while tees help split the airflow to different rooms or vents. The proper use of fittings in HVAC systems ensures optimal airflow and temperature control, improving energy efficiency and comfort within the building. By using the right types of fittings, HVAC systems can operate more effectively, even in complex layouts or buildings with many rooms and ducts.
Agricultural Irrigation Systems
In agricultural applications, fittings that change pipe direction are used in irrigation systems to deliver water to crops in a controlled manner. These systems often require a network of pipes to move water across large fields.
Elbow fittings are used to change the direction of water flow as it moves across different sections of the field, while tees can be used to branch the water supply to different irrigation lines. The ability to change the direction of the water flow allows for efficient irrigation, ensuring that all areas of the field receive the right amount of water for optimal crop growth.
Oil and Gas Pipelines
In the oil and gas industry, fittings are used to change the direction of pipelines that transport crude oil, natural gas, or refined products. These systems are often extremely large and operate under high pressures, requiring fittings that can handle intense conditions.
Elbows, tees, and reducers are commonly used to navigate the pipelines around obstacles, change the direction of flow, or adjust the size of the pipeline to accommodate different types of fluids. The correct installation of pipe fittings is essential in maintaining the integrity and safety of these critical infrastructure systems.
Chemical Processing Plants
In chemical processing plants, pipe fittings are essential for directing the flow of various chemicals through reactors, filters, and other equipment. Fittings such as elbows and tees are used to route the chemicals through the plant while maintaining proper pressure and flow.
In these applications, fittings must be made from materials resistant to corrosion and chemical degradation. Proper installation and maintenance of these fittings ensure that the chemicals are transported safely and that the system operates without leaks or failures.
Conclusion
In conclusion, fittings that change pipe direction are integral to ensuring the smooth and efficient operation of piping systems across various industries. Whether you’re dealing with residential plumbing, industrial fluid transport, or HVAC systems, the ability to control and redirect the flow of fluids is essential for maintaining system integrity.
By understanding the different types of fittings, their manufacturing processes, and proper installation techniques, you can ensure that your piping systems operate effectively and safely.
Choosing the right fitting, understanding its capabilities, and properly installing it will ultimately extend the lifespan of your piping system and improve its performance.
With a range of options available, from elbows and tees to reducers and cross fittings, you can tailor your system to meet any directional change, size transition, or flow control requirement. Always remember that the quality of the fitting, as well as the installation process, plays a crucial role in the long-term success of your piping system.
If you have any questions, please feel free to contact us at any time.
FAQs
What Fitting Changes Pipe Direction at a 90-Degree Angle?
90-Degree Elbow Fitting: This fitting is specifically designed to change the direction of the pipe by 90 degrees. It’s one of the most commonly used fittings in plumbing and piping systems for creating corners or turns.
Available in various materials such as PVC, copper, steel, and brass, and in different sizes to fit diverse applications. Ensure you choose an elbow that matches your pipe size and system requirements. Some elbows come with long sweeps (longer radius) for smoother flow transitions, which can be beneficial in reducing turbulence and pressure drops.
What Fitting Changes Pipe Direction by Splitting Into Two?
Tee Fitting: A tee fitting is used when you need to split the flow from one line into two separate lines. Tees are available in several configurations:Equal Tee: Both outlets have the same diameter as the inlet.
Reducing Tee: One or both outlets have a smaller diameter than the inlet, allowing for connections between pipes of different sizes.
Straight Tee: The branch outlet is perpendicular to the main run.
Sanitary Tee: Designed for use in drain, waste, and vent (DWV) systems where smooth flow is important.When selecting a tee, consider the application, material compatibility, and whether any size reductions are necessary.
Can Pipe Fittings Handle High-Pressure Systems?
Yes, certain pipe fittings are engineered to withstand high-pressure conditions. Forged fittings, for example, are manufactured under high pressure and temperature, resulting in a denser structure that can handle higher pressures compared to cast or threaded fittings.
Materials like stainless steel, carbon steel, and alloy steel are often chosen for their strength and durability in high-pressure environments. Always verify that the fittings you select are rated for the specific pressure and temperature requirements of your system. Refer to the manufacturer’s specifications and consult with a professional if needed.
How Do I Know Which Pipe Fitting to Use?
Selecting the appropriate fitting depends on several factors:Direction Change: Use elbows for changes in direction, tees for branching off, and crosses for four-way intersections.
Pipe Size: Ensure the fitting matches the outer diameter (OD) of your pipe. Measure accurately using calipers or a measuring tape.
System Pressure and Temperature: Choose fittings rated for the working pressure and temperature of your system.
Material Compatibility: Make sure the fitting material is compatible with the pipe material and the fluid being transported.
Application Requirements: Specialized applications may require reducers, unions, flanges, or other specific fittings.Consulting a plumbing or piping chart or seeking advice from a professional can help ensure you make the right choice.
Are There Fittings That Change Pipe Direction and Size?
Yes, reducers are fittings that allow for changes in both direction and size. These fittings are useful when connecting pipes of different diameters.
Types of reducers include:
Concentric Reducers: Used primarily in horizontal runs, they maintain a constant centerline between the larger and smaller ends.
Eccentric Reducers: Commonly used in vertical runs or when transitioning from a larger to a smaller pipe, they offset the centerline to prevent air pockets in liquid systems.
Choose the reducer type based on the application and the orientation of the pipes. Reducers can be straight or angled (elbows with reducing ends), providing flexibility in design.