Hydraulic hose fitting types play a crucial role in the performance and safety of hydraulic systems. Choosing the right fitting type directly impacts the system’s efficiency, durability, and reliability.
In this article, I will guide you through the basic principles, common types, and a detailed comparison of two popular connection methods for hydraulic hose fittings. If you have any questions about the content, feel free to contact us.
What are Hydraulic Hose Fittings?
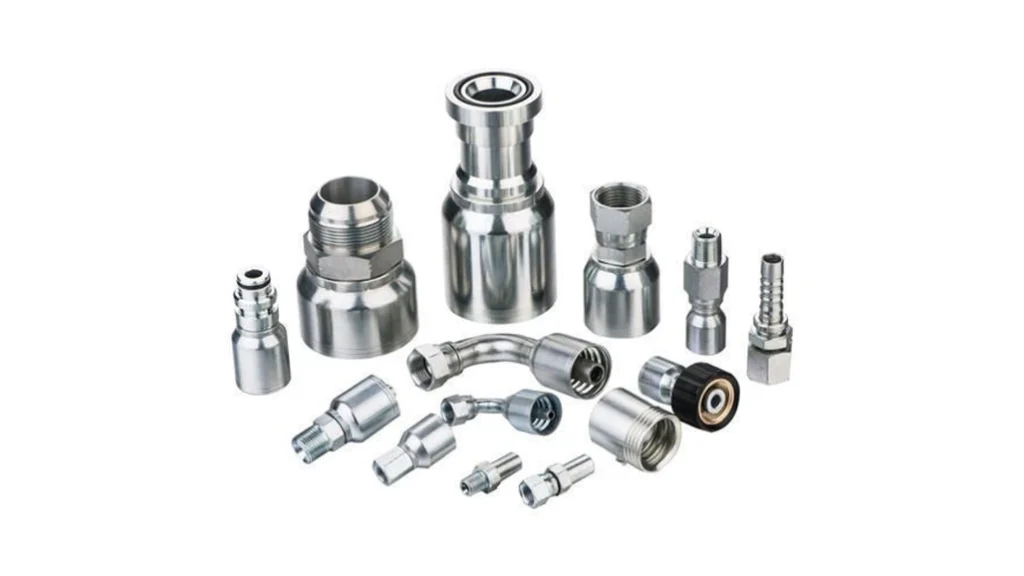
Hydraulic hose fittings are critical components that connect hoses to pumps, valves, cylinders, and other hydraulic system elements. They create leak-proof connections, ensuring the safe transfer of hydraulic fluid under high pressure.
How Do Hydraulic Hose Fittings Work?
Hydraulic fittings use precision engineering to form tight seals, either through compression, threading, or other mechanisms. Their primary function is to withstand high pressure and prevent fluid leaks or disconnections during operation.
Basic Components of Hydraulic Fittings
- Body: The main structure that connects to the hose.
- Ferrule: Crimps around the hose to secure the connection.
- Nut: Provides threading for attachment.
- Seal: Prevents fluid leakage.
Common Types of Hydraulic Hose Fittings
Hydraulic hose fitting types are generally categorized by their connection mechanism and thread style. Here are the most prevalent categories:
1. Compression Hydraulic Hose Fittings
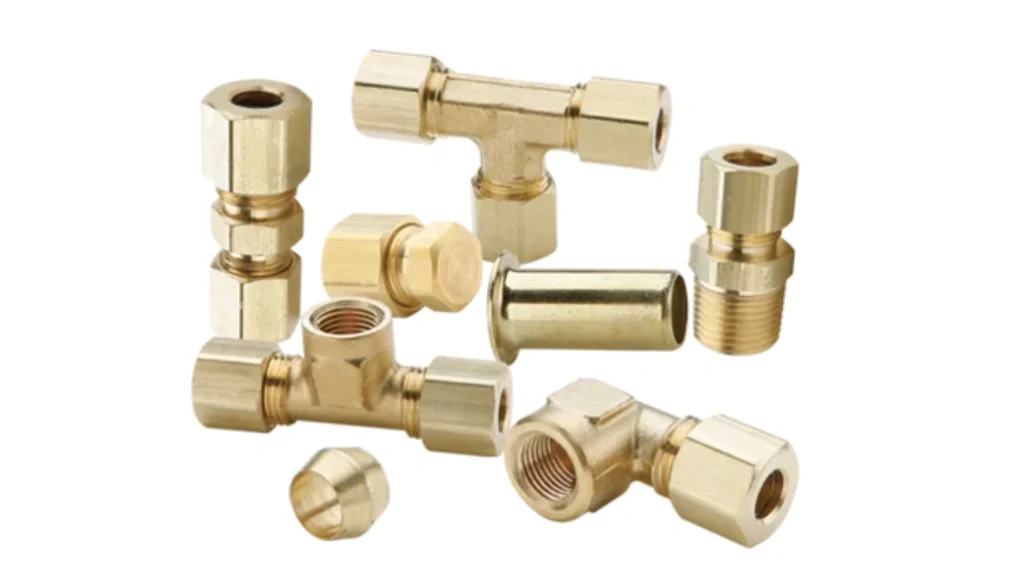
Compression fittings are widely utilized in hydraulic systems due to their robust connection capabilities. They operate by compressing a ferrule (also known as an olive) around the hydraulic hose. This compression creates a tight seal, preventing any leakage of hydraulic fluid. The ferrule is typically made of a malleable metal, such as brass or stainless steel, which can deform under pressure to conform to the shape of the hose.
The structure of compression fittings consists of a fitting body, a compression nut, and one or more ferrules. When installing, the hose is inserted into the fitting body, and the compression nut is tightened. As the nut is turned, it exerts pressure on the ferrule, causing it to bite into the hose and create a secure and leak-tight connection.
These fittings are highly reliable and are especially well-suited for high-pressure systems. In industrial settings where hydraulic systems need to operate under extreme pressure, compression fittings can maintain their integrity. For example, in a hydraulic press used in metal forging, the high-pressure hydraulic fluid requires a connection that can withstand significant force. Compression fittings can handle these demands, ensuring the smooth operation of the press.
However, compression fittings do have some drawbacks. Their installation requires a certain level of skill and precision. If the compression nut is not tightened correctly, it can lead to leaks or even complete failure of the connection. Also, they may be more expensive compared to some other types of fittings due to their complex structure and high-quality materials.
Common Specifications:
- BSPP Compression Fittings: These are based on the British Standard Pipe Parallel thread system. They are commonly used in the UK and other countries following British standards. The parallel threads provide a consistent connection surface, and the compression mechanism ensures a tight seal.
- Metric Compression Fittings: Designed to work with metric-sized hoses and components. They are prevalent in European and Asian countries where the metric system is widely adopted. The metric sizing allows for easy compatibility with other metric-based hydraulic equipment.
- JIC Compression Fittings: Joint Industry Council (JIC) compression fittings are popular in the United States, especially in the automotive and industrial sectors. They have a specific design that meets the industry-recognized standards for performance and reliability.
2. Threaded Hydraulic Hose Fittings
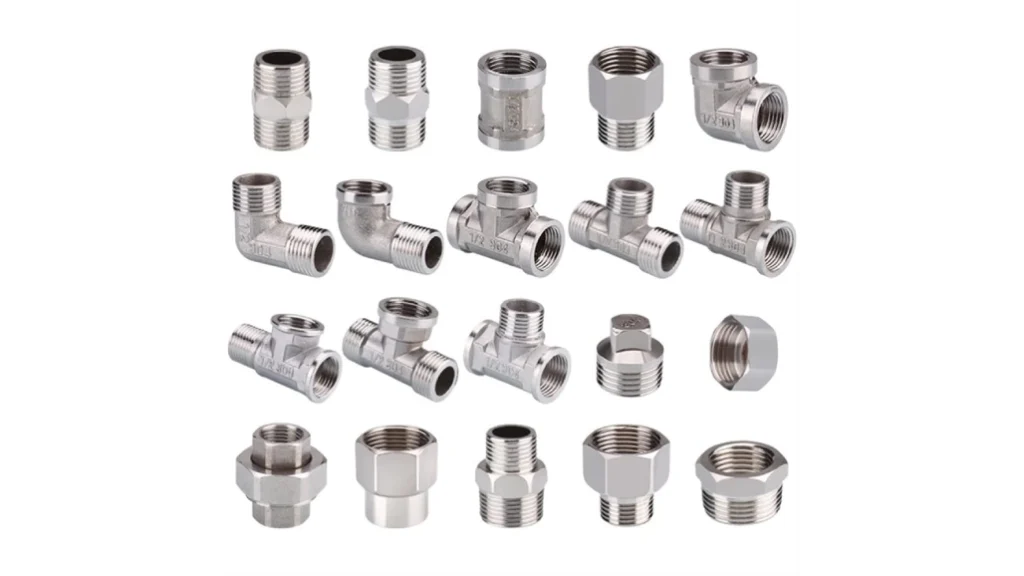
Threaded fittings are a straightforward and widely used type of hydraulic hose connection. They rely on the engagement of matching threads on the fitting and the hose end or the connected component. The threads can be either straight or tapered, depending on the specific application.
The structure of threaded fittings typically includes a male and a female thread. The male thread is usually on the end of the fitting that is inserted into the hose or connected to another component, while the female thread is on the corresponding part. When the two parts are screwed together, the threads interlock, creating a connection.
These fittings are popular because of their simplicity and effectiveness. They are easy to install and disassemble, which makes them convenient for maintenance and repairs. In small-scale hydraulic systems, such as those used in DIY projects or small machinery, threaded fittings are a common choice. For example, in a home – made hydraulic lift for a garage, threaded fittings can be used to connect the hoses to the pump and the lift cylinder.
However, threaded fittings may not be as suitable for high – pressure or high – vibration environments. The threads can loosen over time due to vibration, leading to leaks. Also, the sealing ability of threaded fittings often depends on additional sealing elements like gaskets or thread sealants. If these are not properly applied, leakage can occur.
Common Specifications:
- NPT (National Pipe Thread): Widely used in North America. NPT threads are tapered, which means the diameter of the thread changes along its length. This taper helps to create a seal when the threads are tightened. NPT fittings are commonly used in hydraulic systems in the United States, especially in the automotive and industrial sectors.
- BSP (British Standard Pipe): There are two types of BSP threads – BSPP (British Standard Pipe Parallel) and BSPT (British Standard Pipe Tapered). BSPP threads are parallel and are often used for applications where a more precise and consistent connection is required. BSPT threads, on the other hand, are tapered and are suitable for applications where a self-sealing connection is needed. BSP fittings are commonly used in the UK and many other countries that follow British standards.
- UNF (Unified Fine Thread): The Unified Fine Thread is part of the Unified Thread Standard, which is used in the United States and some other countries. UNF threads have a finer pitch compared to some other thread types, which allows for a more precise adjustment and a stronger connection. They are often used in applications where a high-strength and accurate connection is required.
3. Push-to-Connect Hydraulic Hose Fittings
Push – to – connect fittings are designed for quick and tool-free connections, making them extremely convenient in certain applications. These fittings have a unique mechanism that allows the hose to be simply pushed into the fitting, and a built-in locking mechanism holds it in place.
The structure of push-to-connect fittings typically includes a body with a cavity to receive the hose, a locking mechanism (such as a spring-loaded collet or a ball-and-groove system), and a sealing element. When the hose is pushed into the fitting, the locking mechanism engages, preventing the hose from being pulled out. The sealing element, usually an O-ring or a sealing gasket, ensures a leak-tight connection.
These fittings are common in low-pressure systems where the need for frequent connection and disconnection is high. In applications such as portable hydraulic tools, irrigation systems, or pneumatic systems, push-to-connect fittings offer great convenience. For example, in a portable hydraulic jack used for automotive repairs, the ability to quickly connect and disconnect the hydraulic hose can save time and effort.
However, push-to-connect fittings may not be suitable for high-pressure or high-vibration environments. The locking mechanism may not be able to withstand high pressures, and vibration can cause the hose to become dislodged. Also, the sealing ability of these fittings may be limited compared to other types of fittings.
Common Specifications:
- DOT Push Fittings: These are designed to meet the Department of Transportation (DOT) standards, which are often used in automotive and transportation-related hydraulic systems. DOT push fittings are known for their reliability and ease of use in applications such as brake systems and hydraulic clutch systems.
- SAE Quick-Connects: The Society of Automotive Engineers (SAE) quick-connect fittings are widely used in the automotive and industrial sectors. They are designed to provide a fast and secure connection, and their design meets the industry-recognized SAE standards for performance and reliability.
4. Flange Hydraulic Hose Fittings
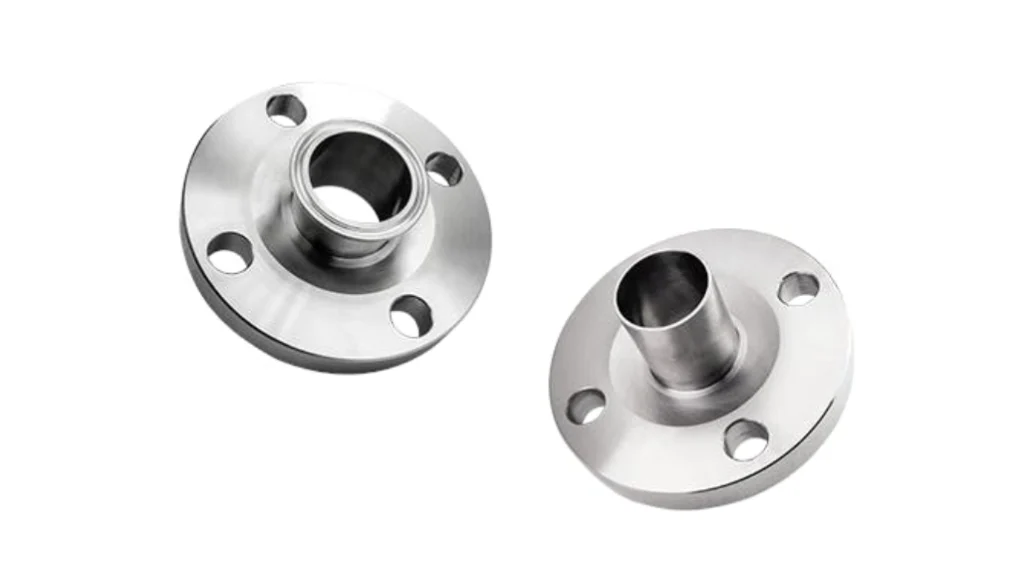
Flange fittings are used to create a strong and vibration-resistant connection in hydraulic systems. They use bolts and flanges to join two components together, providing a large contact area and a secure connection.
The structure of flange fittings consists of two flanges, one on each component to be connected, and a set of bolts and nuts. The flanges are typically made of metal, such as steel or stainless steel, and have holes for the bolts. The hydraulic hose is usually connected to the flange through a separate fitting or by being directly attached to the flange. When the bolts are tightened, the flanges are pulled together, creating a tight seal.
These fittings are commonly used in high-pressure and high-vibration environments, such as in industrial machinery, large-scale hydraulic systems, and offshore applications. For example, in an oil rig’s hydraulic system, where the equipment is subject to significant vibration and high-pressure hydraulic fluid, flange fittings can provide a reliable and long-lasting connection.
However, flange fittings are relatively large and heavy compared to other types of fittings. Their installation also requires more space and effort, as it involves aligning the flanges and tightening multiple bolts. Additionally, they are more expensive due to their complex structure and the need for high-quality materials.
Common Specifications:
- SAE Code 61 and Code 62: These are standards set by the Society of Automotive Engineers. SAE Code 61 flanges are used for high-pressure applications and have a specific design that meets the SAE standards for performance and reliability. SAE Code 62 flanges are similar but are designed for even higher-pressure applications.
- ISO 6162 Flange Fittings: These are based on the International Organization for Standardization (ISO) standards. ISO 6162 flange fittings are widely used in international markets and are known for their compatibility and reliability.
5. Swaged and Crimped Flange Hydraulic Hose Fittings
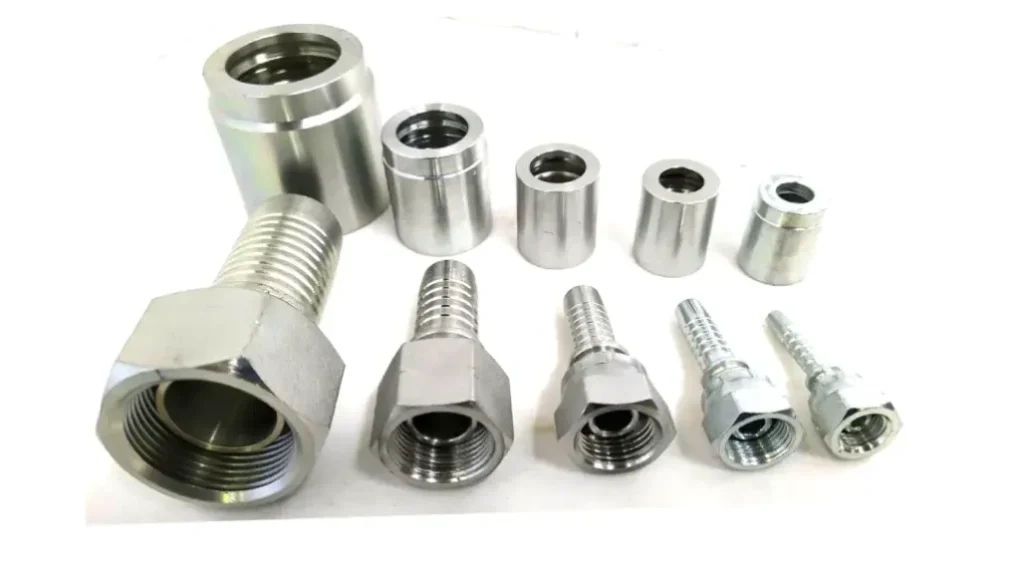
Swaged and crimped fittings are permanently attached to the hydraulic hose using specialized crimping tools. This method ensures a long-lasting and reliable connection.
The process of attaching swaged and crimped fittings involves inserting the hose into the fitting and then using a crimping tool to deform the fitting around the hose. The fitting is designed to tightly grip the hose, creating a secure and leak-tight connection. The crimping tool applies a specific amount of force to ensure the proper deformation of the fitting.
These fittings are commonly used in applications where a permanent and high-strength connection is required. In industrial hydraulic systems, such as those in manufacturing plants or construction equipment, swaged and crimped fittings can provide a reliable connection that can withstand harsh operating conditions. For example, in a large-scale construction crane’s hydraulic system, the swaged and crimped fittings ensure that the hydraulic hoses remain connected under high-pressure and heavy-duty usage.
However, once installed, swaged and crimped fittings are difficult to remove or replace. If there is a problem with the hose or the fitting, the entire assembly may need to be replaced. Also, the installation requires specialized crimping tools, which can be expensive and may not be readily available.
Common Specifications:
- Hydraulic Crimp Fittings: These are specifically designed for hydraulic applications. They are available in various sizes and materials to suit different hydraulic system requirements. The crimping process for hydraulic crimp fittings is carefully controlled to ensure a proper and reliable connection.
- Swaged Ferrule Fittings: Swaged ferrule fittings use a ferrule that is swaged onto the hose. The swaged ferrule provides a tight grip on the hose, creating a secure connection. These fittings are often used in high-pressure hydraulic systems where a strong and reliable connection is essential.
Summary Table:
Fitting Type | Connection Mechanism | Structure Highlights | Suitable Environments | Advantages | Disadvantages | Common Specifications |
Compression Fittings | Compresses a ferrule around the hose | Fitting body, compression nut, one or more ferrules | High-pressure systems | Highly reliable, good for high-pressure scenarios | Installation requires skill, relatively expensive | BSPP Compression Fittings, Metric Compression Fittings, JIC Compression Fittings |
Threaded Fittings | Matching threads on fitting and hose/component | Male and female threads | Low-pressure, simple systems | Simple, easy to install, and disassemble | May loosen in high – vibration, sealing may depend on additional elements | NPT (National Pipe Thread), BSP (British Standard Pipe), UNF (Unified Fine Thread) |
Push-to-Connect Fittings | Push-in connection with built-in locking mechanism | Body with cavity, locking mechanism, sealing element | Low-pressure systems with frequent connection/disconnection needs | Quick and tool-free connection | High-pressure, high – vibration environments | DOT Push Fittings, SAE Quick – Connects |
Flange Fittings | Bolts and flanges join components | Two flanges, bolts, nuts | Strong, vibration-resistant connection | Applications requiring permanent, high-strength connection | Large, heavy, installation requires more space and effort, expensive | SAE Code 61 and Code 62, ISO 6162 Flange Fittings |
Swaged and Crimped Fittings | Hose inserted into the fitting, deformed by the crimping tool | Specialized crimping tools permanently attach fitting to the hose | Long-lasting, reliable connection | Hose inserted into the fitting, deformed by crimping tool | Difficult to remove or replace, requires specialized tools | Hydraulic Crimp Fittings, Swaged Ferrule Fittings |
How to Choose the Right Hydraulic Hose Fitting
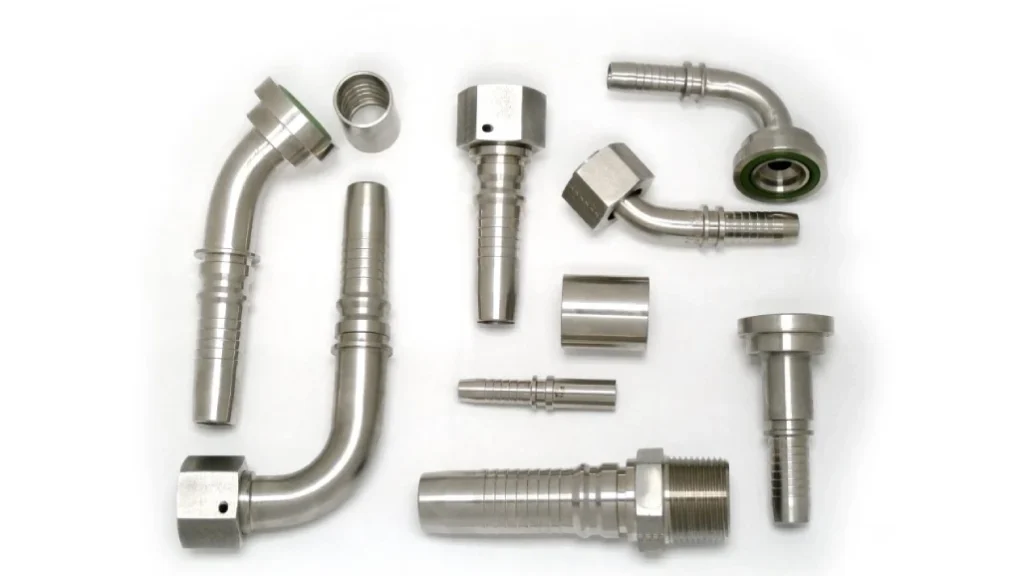
When selecting hydraulic hose fittings, consider the following steps:
Step 1: Assess System Requirements
Identify the pressure, temperature, and flow rate requirements of your hydraulic system.
Step 2: Match Hose and Fitting Specifications
Ensure compatibility between hose and fitting materials, dimensions, and pressure ratings.
Step 3: Consider the Environment
For corrosive or high-temperature environments, select fittings with appropriate coatings or materials, like stainless steel.
Step 4: Evaluate Installation and Maintenance Needs
Choose a fitting type that aligns with your team’s expertise and maintenance capabilities.
Step 5: Consult Experts
When in doubt, consult hydraulic specialists or trusted suppliers like Dingfeng for customized solutions.
Conclusion
In conclusion, understanding the different hydraulic hose fitting types is essential for anyone working with hydraulic systems. Each type has its own unique characteristics, advantages, and limitations.
By considering factors such as pressure and flow requirements, the working environment, and compatibility, we can make an informed decision on which fitting type to use.
Whether it’s a small-scale DIY hydraulic project or a large-scale industrial installation, choosing the right fitting can ensure the smooth operation and long-term reliability of the hydraulic system. If you’re interested in our products, you can visit our homepage or ask us for a product catalog.
FAQs About Hydraulic Hose Fitting Types
What are the different types of hydraulic hose connectors?
There are several different types of hydraulic hose connectors. Flared fittings, have a flared end on the hose that is compressed by a nut and sleeve. Compression fittings use a compression nut and ferrules to create a seal on the hose.
Quick-connect fittings are designed for easy connection and disconnection, with male and female parts that lock together. There are also bite-type fittings, where a metal insert bites into the hose to create a connection.
Each type has its own advantages and is suitable for different applications. For example, I used flared fittings in a car’s hydraulic brake system, compression fittings in a hydraulic press, and quick-connect fittings in a portable hydraulic testing kit.
What is the best type of hydraulic fitting?
The best type of hydraulic fitting depends on various factors. If you need a fitting for a high-pressure system, compression fittings are often a great choice due to their high-strength connection and excellent sealing capabilities.
For applications where you need to frequently connect and disconnect the hoses, quick-connect fittings are ideal. In low-pressure and simple systems, flared fittings can be sufficient. For example, in my homemade hydraulic lift for car maintenance, I used compression fittings because of the high-pressure requirements.
But when I needed to connect and disconnect hoses frequently to test different hydraulic components, I switched to quick-connect fittings.
How to identify hydraulic fitting types?
Identifying hydraulic fitting types can be done by examining their structure. Flared fittings have a distinct flared end on the hose, along with a nut and sleeve. Compression fittings have a compression nut and one or more ferrules.
Quick – connect fittings are easily recognizable by their male and female parts with a locking mechanism. You can also look at the connection method. If it involves a threaded connection, it could be a type of flared or compression fitting.
In some cases, referring to the manufacturer’s markings or documentation can also help. I once had to identify fittings in an old hydraulic system. By carefully examining the structure and connection method, I was able to determine that they were compression fittings.
What are the most common thread types of fittings used when making hydraulic hoses?
The most common thread types for hydraulic hose fittings include NPT (National Pipe Thread), BSP (British Standard Pipe), and metric threads. NPT threads are widely used in North America.
They have a tapered design, which helps create a seal when tightened. BSP threads are common in the UK and many other countries. There are two types of BSP threads: BSPP (parallel) and BSPT (tapered).
Metric threads are used in many European and Asian countries. The choice of thread type depends on the region, the compatibility with other components in the system, and the specific application requirements. For example, in a hydraulic system for a machine imported from Europe, I had to use metric – threaded fittings to ensure proper connection.
Can hydraulic hose fittings be reused?
In some cases, hydraulic hose fittings can be reused. Flared fittings and compression fittings can often be reused if they are in good condition.
For example, if the flared end of a hose and the corresponding fitting parts are not damaged, and the compression nuts and ferrules of compression fittings have not been overly deformed, they can be disassembled and reinstalled.
However, it’s important to carefully inspect them for any signs of wear, corrosion, or damage before reuse.
Quick-connect fittings can also be reused, but if the locking mechanism is damaged or the seals are worn out, it’s best to replace them. I’ve reused compression fittings in some of my projects after thoroughly inspecting them, and they worked just fine.