Compression fittings are essential components in plumbing, gas lines, and various mechanical systems, providing a secure connection between pipes.
Many people often wonder, “Can you reuse compression fittings?” While compression fittings are known for their ease of use and reliability, there’s often confusion around whether they can be reused, especially after they’ve been installed.
In this article, we will dive deep into the factors that determine whether compression fittings can be reused, their limitations, and the best practices for reusing them. If you have any questions or doubts about the content, feel free to contact us for further clarification.
Understanding Compression Fittings
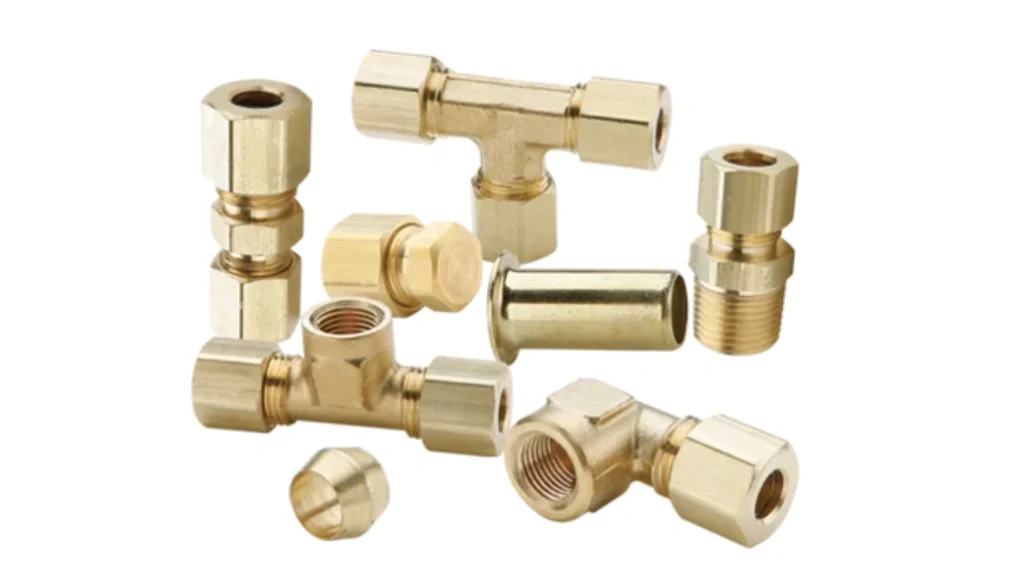
Structure
Compression fittings typically consist of three main parts: a compression nut, a ferrule (also known as an olive), and a fitting body. The compression nut is the outer part that you tighten with a wrench. The ferrule is a small, usually brass or plastic ring that plays a crucial role in creating a seal. The fitting body is what connects the pipes.
Working Principle
The working principle of compression fittings is quite straightforward. When you tighten the compression nut, it exerts pressure on the ferrule.
This pressure causes the ferrule to deform slightly and squeeze onto the pipe, creating a tight seal. This seal prevents any leaks in the plumbing or piping system. I remember when I first started working with compression fittings, understanding this principle was key to ensuring successful installations.
Factors Affecting the Reusability of Compression Fittings
Fitting Material
- Copper Compression Fittings
Copper compression fittings are quite common. They are relatively durable and can often be reused multiple times. However, over time, copper can corrode, especially in environments with high levels of moisture or certain chemicals.
I once had a project in an old building where the copper compression fittings showed signs of corrosion after a few years of use. Despite this, after careful inspection and cleaning, some of them were still reusable.
- Stainless Steel Compression Fittings
Stainless steel compression fittings are highly resistant to corrosion. They can withstand harsh environments better than copper fittings. In my experience, stainless steel compression fittings can be reused many times without significant degradation in performance.
I’ve reused stainless steel compression fittings in industrial piping systems where the conditions were quite demanding.
- Plastic Compression Fittings
Plastic compression fittings are lightweight and easy to install. However, they may not be as durable as metal fittings. They can be more prone to cracking or deforming under pressure. I’ve found that plastic compression fittings can usually be reused a few times, but it’s important to check them carefully for any signs of damage.
Usage Environment
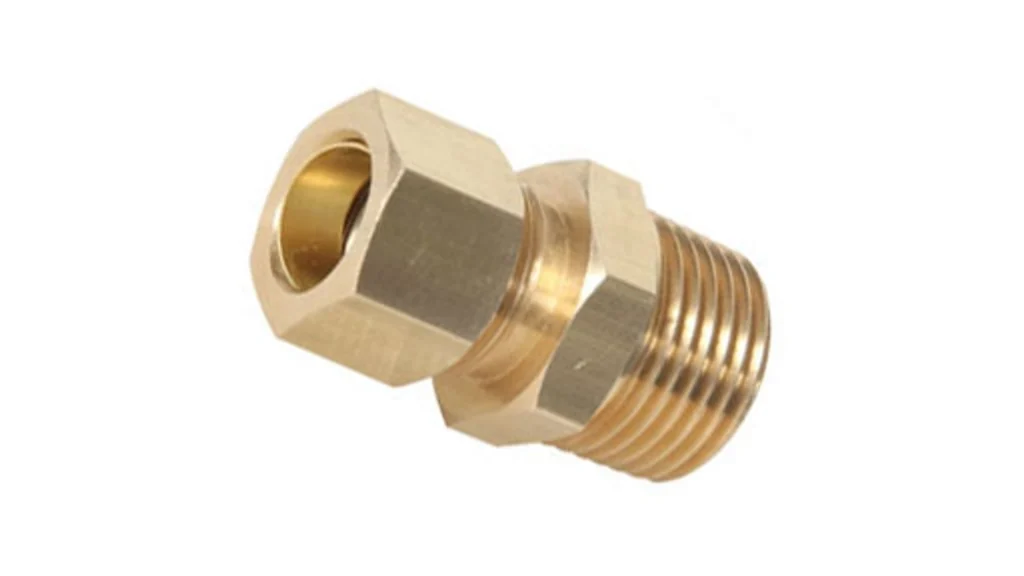
- High – Temperature Environments
In high-temperature environments, compression fittings can be affected. For example, in a hot water heating system, the constant exposure to high temperatures can cause the materials to expand and contract.
This can lead to wear and tear on the fitting components. I had a situation where compression fittings in a steam-based heating system needed to be replaced more frequently due to the extreme heat.
- High – Pressure Environments
High-pressure environments put a lot of stress on compression fittings. The seals can be more likely to fail, and the components may experience more significant wear. In a commercial building’s water supply system with high-pressure pumps, I had to be extra cautious when considering reusing compression fittings.
- Chemically Corrosive Environments
If the fluid flowing through the pipes contains chemicals that can corrode the fitting materials, the reusability of compression fittings is greatly reduced. I worked on a project in a chemical plant where the pipes carried corrosive substances. In this case, reusing compression fittings was not a viable option as they deteriorated quickly.
Usage Frequency and Wear
As compression fittings are used more frequently, the components, especially the ferrule and the sealing surfaces, will experience wear. The ferrule may become deformed or lose its ability to create a proper seal.
I’ve seen cases where after repeated use, the ferrule of a compression fitting became so worn that it could no longer provide a leak-tight connection. By examining the wear patterns, I could determine whether the fitting was still reusable.
How to Determine if Compression Fittings Can Be Reused
Visual Inspection
- Step 1: Check for Cracks
Carefully examine the fitting body, compression nut, and ferrule for any cracks. Cracks can be a sign of serious damage and indicate that the fitting should not be reused. I always use a bright light and a magnifying glass to get a closer look.
- Step 2: Look for Deformation
Check for any signs of deformation in the fitting. This could include a bent or misshapen compression nut or a ferrule that has lost its original shape. A deformed fitting may not be able to create a proper seal.
- Step 3: Examine Wear Marks
Look for wear marks on the sealing surfaces and the ferrule. Excessive wear can mean that the fitting is no longer reliable.
Sealing Performance Test
- Step 1: Assemble the Fitting
Put the compression fitting back together with a section of pipe. Make sure to assemble it correctly, just as you would for a new installation.
- Step 2: Apply Low – Pressure Fluid
Apply a low – pressure fluid, such as water or air, to the system. In a plumbing application, I would use water and slowly increase the pressure to a level slightly above normal operating pressure.
- Step 3: Check for Leaks
Inspect the fitting for any signs of leakage. If there are leaks, the fitting may not be suitable for reuse.
Component Integrity Check
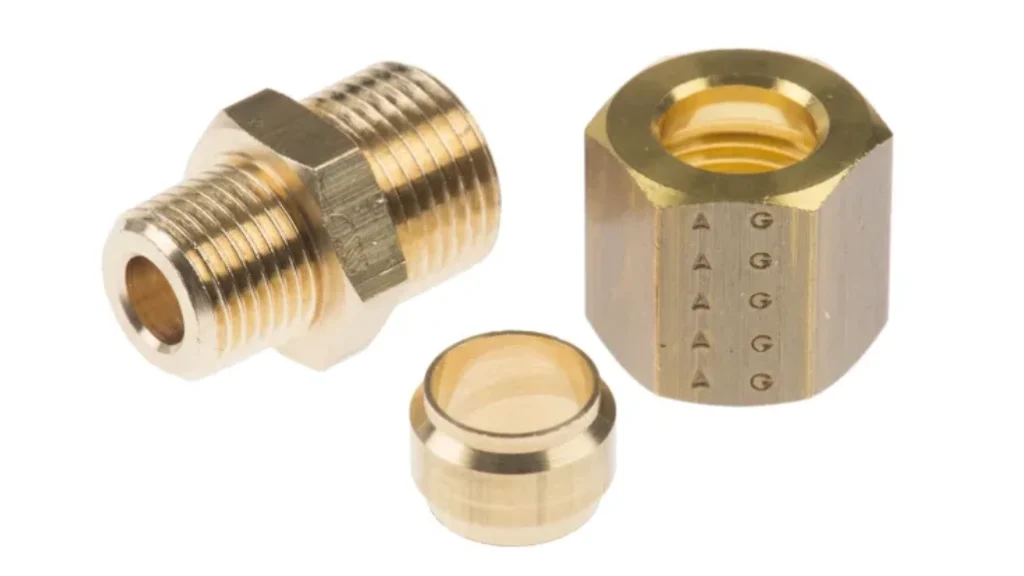
- Step 1: Check the Compression Nut
Make sure the threads on the compression nut are in good condition. Stripped threads can prevent the nut from being tightened properly.
- Step 2: Examine the Ferrule
Check that the ferrule is intact and has not lost any of its parts. A missing or damaged ferrule will not be able to create a proper seal.
- Step 3: Assess the Fitting Body
Ensure that the fitting body has no holes or other damage that could affect its functionality.
Steps and Precautions for Reusing Compression Fittings
Dismantling Steps
- Step 1: Prepare the Tools
Gather the necessary tools, such as an adjustable wrench or a pipe wrench. I always make sure my wrenches are in good condition and the right size for the job.
- Step 2: Loosen the Compression Nut
Using the wrench, carefully loosen the compression nut in a counter-clockwise direction. Be gentle to avoid damaging the threads.
- Step 3: Remove the Ferrule and Separate the Pipes
Once the nut is loose enough, remove the ferrule and separate the pipes from the fitting body.
Cleaning and Maintenance
- Step 1: Clean the Fitting
Use a suitable cleaner to remove any dirt, debris, or corrosion from the fitting. I often use a wire brush or a chemical cleaner depending on the material of the fitting.
- Step 2: Lubricate the Threads
Apply a small amount of lubricant to the threads of the compression nut. This will make it easier to tighten and prevent the threads from seizing.
- Step 3: Inspect and Replace Worn Parts
If any parts, such as the ferrule, show excessive wear, consider replacing them.
Re-installation Steps
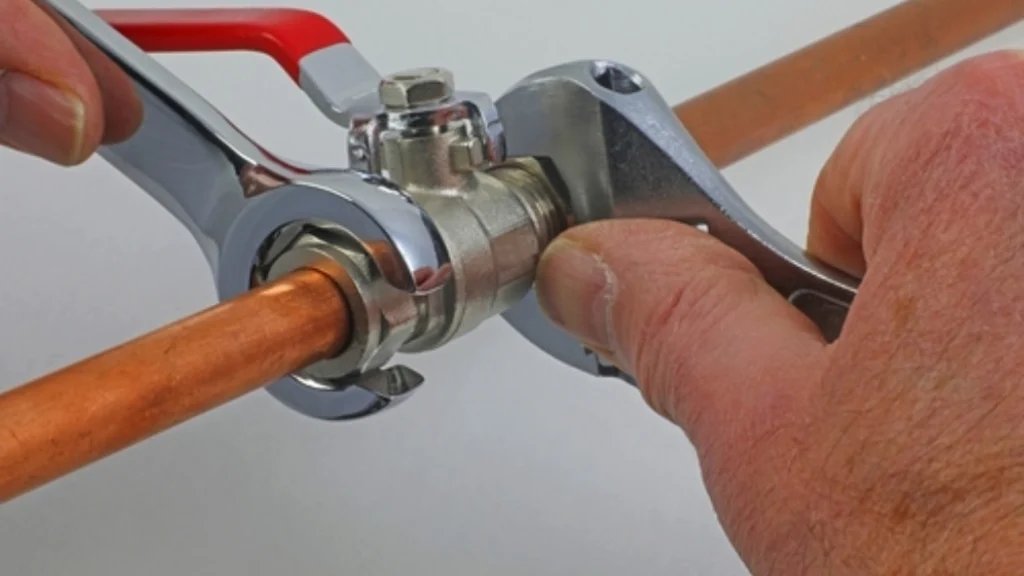
- Step 1: Slide the Components onto the Pipe
Slide the compression nut and then the ferrule onto the pipe in the correct order. Just like in a new installation, the ferrule should be facing the end of the pipe.
- Step 2: Insert the Pipe into the Fitting Body
Insert the pipe into the fitting body until it reaches the stop.
- Step 3: Tighten the Compression Nut
First, hand-tighten the nut as much as possible. Then, use a wrench to give it an additional 1/4 to 1/2 turn, but be careful not to over-tighten.
Re-Inspection and Testing
- Step 1: Visual Inspection
After re-installation, visually inspect the fitting to make sure everything looks correct.
- Step 2: Pressure Test
Apply the appropriate pressure to the system and check for any leaks. I usually let the system run for a while to ensure there are no hidden leaks.
How Many Times Can You Reuse a Compression Fitting?
The number of times you can reuse a compression fitting depends on several factors, including the type of material, the condition of the fitting, and the pressure it will be exposed to. In general, you can reuse compression fittings at least once, but they may lose some of their sealing ability with each reuse.
For example, brass compression fittings can often be reused several times if the ferrule remains intact and there’s no significant wear. However, if you’re working with copper pipes or plastic materials, it’s generally recommended to replace the ferrule after each use to ensure a secure seal.
From my experience, it’s always a good idea to replace the ferrule for better longevity and security of the connection, as the compression fitting’s ability to seal properly diminishes over time.
Conclusion
In conclusion, the question of whether you can reuse compression fittings is not a simple one-size-fits-all answer. It depends on various factors such as the fitting material, the usage environment, and the level of wear.
By carefully inspecting the fittings, performing the necessary tests, and following the correct procedures for disassembly, cleaning, and reinstallation, it is possible to reuse compression fittings in many cases.
However, it’s crucial to exercise caution and make sure that the reused fittings will not compromise the safety and functionality of the plumbing or piping system.
If you’re interested in our products, you can visit our homepage or ask us for a product catalog.
FAQs About Reuse Compression Fittings
Can Compression Fittings Be Reused on Copper Pipe?
Copper pipes are one of the most common materials used with compression fittings. Yes, compression fittings can be reused on copper pipes as long as the fitting and ferrule are in good condition. However, with repeated use, the ferrule may lose its ability to compress effectively, leading to potential leaks.
When reusing a compression fitting on copper pipes, always inspect the ferrule for signs of deformation. If the ferrule is damaged or flattened, it’s essential to replace it to ensure a proper seal.
Can You Undo and Redo a Compression Fitting?
Yes, you can undo and redo a compression fitting, but it’s important to proceed carefully. Repeated disassembly and reassembly can cause wear and tear on the fitting components, especially the ferrule.
To avoid any damage, make sure you reassemble the fitting using proper tools, and test the connection thoroughly to check for leaks. If the fitting or ferrule shows signs of damage, it’s best to replace them before reusing.
Are Compression Fittings Single Use?
Compression fittings are generally not single-use, but they do have limitations. The main factor in determining whether a compression fitting is reusable is the condition of the ferrule. If the ferrule has been deformed or flattened, it will no longer create a tight seal, and the fitting should be replaced.
In some cases, such as with brass fittings or higher-quality compression fittings, you can reuse them multiple times as long as the ferrule and fitting remain in good condition. However, it’s advisable to always replace the ferrule to maintain the integrity of the seal.
Can Gas Compression Fittings Be Reused?
Gas compression fittings can generally be reused, but with more caution. When working with gas lines, the integrity of the seal is critical to avoid dangerous leaks. If the fitting has been in place for a while, it’s essential to check the ferrule and fitting thoroughly for damage.
In my experience, gas compression fittings should ideally be replaced if they have been used for extended periods. If you choose to reuse them, always test the connection for leaks before putting the system back into operation.
Barb vs Compression Fittings: What’s the Difference?
Barb fittings and compression fittings both serve similar functions—connecting two pipes or hoses together—but they operate differently.
Barb fittings have a series of barbs that hold the hose or pipe in place as the fitting is pushed in. These are typically used for flexible hoses and don’t require any sealing materials.
Compression fittings, on the other hand, use a ferrule and nut to compress the pipe against the fitting, creating a tight seal. These are more commonly used for rigid pipes like copper and brass.
While barb fittings are easier to install and remove, compression fittings tend to offer a more secure and leak-proof connection, especially for high-pressure systems.
How to Properly Install a Compression Fitting?
To install a compression fitting, first insert the pipe into the fitting and then place the ferrule onto the pipe. Slide the nut over the ferrule and tighten it onto the fitting.
Make sure the pipe is fully inserted and the nut is tightened securely without over-tightening. Always test for leaks after installation.