Hydraulic couplers are vital components in any hydraulic system, enabling efficient fluid transfer and connection between various parts. Choosing the right type of coupler is crucial for optimal performance and preventing costly leaks or failures. With numerous types available, each designed for specific applications, understanding their differences is essential.
This blog post will delve into the various types of hydraulic couplers, highlighting their features, benefits, and ideal applications. We aim to provide a comprehensive guide to help you make informed decisions when selecting the best hydraulic coupler for your specific needs, ensuring your hydraulic systems operate smoothly and reliably.
What Are Hydraulic Couplers

Hydraulic couplers are critical components in hydraulic systems, facilitating the connection and disconnection of hydraulic hoses, pipes, and other components. They ensure efficient fluid flow and prevent leaks, enabling the reliable operation of hydraulic machinery.
Key functions of hydraulic couplers include:
- Connecting and disconnecting hydraulic lines.
- Ensuring leak-free fluid transfer.
- Withstanding high pressures and vibrations.
- Enabling the transmission of hydraulic power.
Key Components of Hydraulic Couplers
Hydraulic couplers are essential components in hydraulic systems, facilitating the connection and disconnection of hydraulic hoses, pipes, and other components. They ensure efficient fluid flow and prevent leaks, enabling the reliable operation of hydraulic machinery.
Key components of hydraulic couplers include:
- Body: The main housing of the coupler, providing structural support and containing other components.
- Sleeve or Collar: In quick-disconnect couplings, this component is used to engage or disengage the locking mechanism.
- Seals: These components, such as O-rings or gaskets, prevent fluid leakage at the connection point.
- Locking Mechanism: This mechanism, often involving balls or poppets, ensures a secure connection between the male and female halves of the coupler.
- Valve (in some types): Some couplers, such as poppet-type couplings, incorporate a valve to control fluid flow and minimize spillage during disconnection.
Hydraulic Coupler Types
Hydraulic couplers are essential for connecting and disconnecting hydraulic lines, each type designed for specific applications and operational needs. Understanding their variations is critical for optimal system performance. This guide explores the diverse range of hydraulic couplers, highlighting their unique features and applications.
Quick-Release Hydraulic Couplers
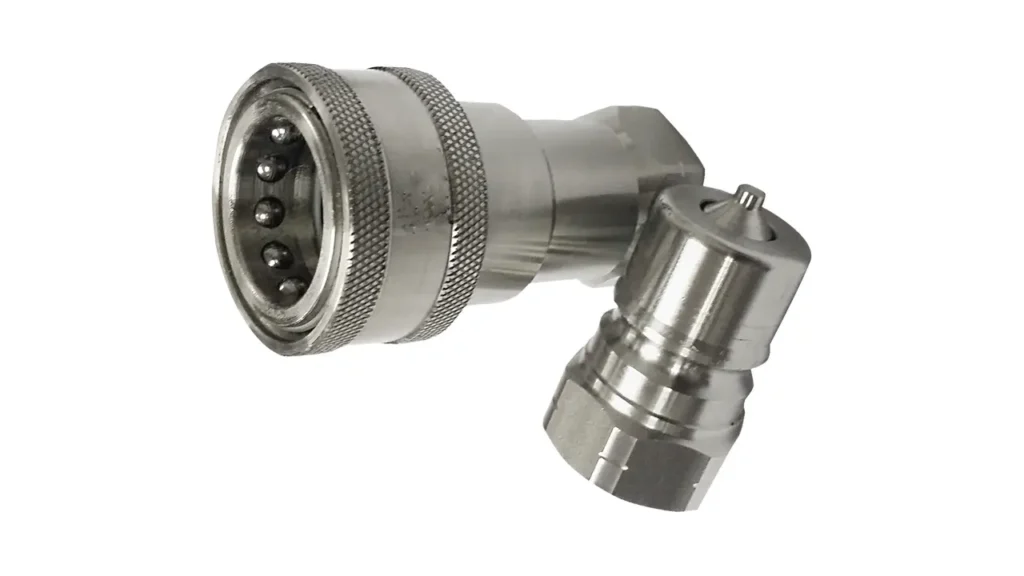
Quick-release hydraulic couplers are designed for rapid connection and disconnection of hydraulic lines, minimizing downtime and simplifying maintenance. They typically utilize a ball-locking mechanism that allows for easy engagement and disengagement without the need for tools. These couplers are ideal for applications requiring frequent changes or where speed is crucial, such as in mobile hydraulic equipment, construction machinery, and agricultural implements.
The design of quick-release couplers often includes a sleeve or collar that, when retracted, releases the locking balls, allowing the male and female halves to separate. This mechanism ensures a secure connection while providing the convenience of quick detachment. They are widely used in situations where hydraulic tools or attachments need to be changed frequently, improving operational efficiency.
These couplers are available in various sizes and pressure ratings to accommodate different hydraulic systems. They are often used in environments where fluid spillage is a concern, and some models include features to minimize fluid loss during disconnection. Their versatility and ease of use make them a staple in many hydraulic applications.
Flat-Face Hydraulic Couplers
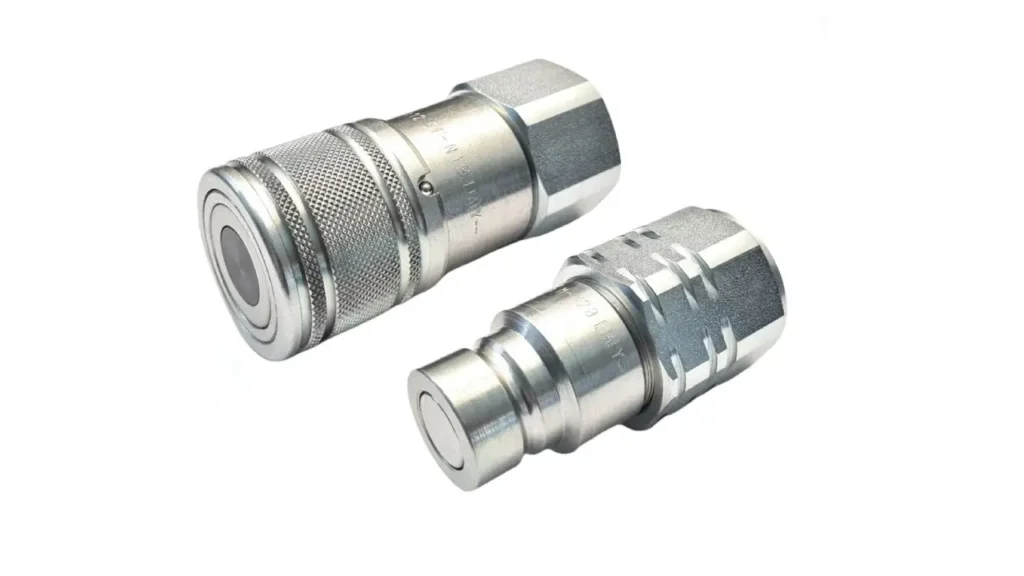
Flat-face hydraulic couplers are designed to minimize fluid spillage and contamination during connection and disconnection. They feature a flat mating surface that reduces the amount of trapped fluid and allows for easy cleaning. These couplers are ideal for applications where cleanliness and environmental protection are essential, such as in food processing, pharmaceutical, and environmentally sensitive industries.
The flat-face design also provides a more robust connection, reducing the risk of leaks and ensuring a reliable seal. These couplers are often used in high-pressure hydraulic systems where fluid loss can be costly or hazardous. Their design minimizes air inclusion, which can cause damage to hydraulic components.
Flat-face couplers are available in various materials, including stainless steel, to enhance corrosion resistance and durability. They are commonly used in applications where hydraulic tools are frequently changed, ensuring a clean and efficient connection every time. Their design reduces the need for frequent cleaning and maintenance, which can save time and resources.
ISO-A Hydraulic Couplers
ISO-A hydraulic couplers are designed according to the ISO 7241-A standard, ensuring interchangeability between different manufacturers. They are general-purpose couplers widely used in industrial and agricultural applications. These couplers typically utilize a ball-locking mechanism and are known for their reliability and ease of use.
The ISO-A standard ensures that couplers from different manufacturers can be interchanged, simplifying maintenance and reducing the need for specialized parts. This standardization makes them a popular choice for original equipment manufacturers (OEMs) and end-users alike. They are designed to handle a wide range of pressures and flow rates, making them suitable for diverse hydraulic systems.
ISO-A couplers are available in various materials, including steel and stainless steel, to accommodate different operating environments. They are commonly used in applications such as construction equipment, agricultural machinery, and industrial tools. Their robust design and standardized dimensions make them a reliable choice for many hydraulic applications.
ISO-B Hydraulic Couplers
ISO-B hydraulic couplers are designed according to the ISO 7241-B standard, providing another level of interchangeability and reliability. They are commonly used in applications where a more robust and leak-resistant connection is required. These couplers typically feature a poppet-valve design, which minimizes fluid loss during disconnection.
The ISO-B standard ensures that these couplers are interchangeable with other manufacturers‘ products, simplifying maintenance and reducing downtime. The poppet-valve design provides a reliable seal and minimizes fluid spillage, making them suitable for applications where environmental protection is a concern. They are designed to withstand high pressures and flow rates, ensuring reliable performance in demanding environments.
ISO-B couplers are available in various materials, including steel and stainless steel, to accommodate different operating conditions. They are commonly used in applications such as construction machinery, industrial equipment, and agricultural implements. Their robust design and standardized dimensions make them a trusted choice for many hydraulic systems.
Screw-To-Connect Hydraulic Couplers

Screw-to-connect hydraulic couplers provide a secure and reliable connection for high-pressure hydraulic systems. They feature a threaded connection that is tightened to create a leak-proof seal. These couplers are ideal for applications where high pressure and vibration are present, such as in heavy-duty industrial equipment and offshore applications.
The threaded connection of screw-to-connect couplers ensures a robust seal, preventing leaks even under extreme conditions. They are designed to withstand high pressures and vibrations, making them suitable for demanding environments. They are commonly used in applications where safety and reliability are paramount.
These couplers are available in various materials, including high-strength steel and stainless steel, to accommodate different operating conditions. They are often used in systems where frequent connection and disconnection are not required, as the threaded connection takes longer to engage and disengage compared to quick-release couplers. Their durability and high-pressure capabilities make them a reliable choice for critical hydraulic applications.
High-Pressure Hydraulic Couplers
High-pressure hydraulic couplers are designed to withstand extreme pressures, ensuring reliable performance in demanding applications. They are commonly used in heavy-duty industrial equipment, construction machinery, and offshore operations. These couplers are engineered to handle pressures exceeding the capabilities of standard hydraulic couplers.
The design of high-pressure couplers often includes specialized sealing materials and robust construction to prevent leaks and failures under high-pressure conditions. They are subjected to rigorous testing to ensure their integrity and reliability. They are commonly used in applications where safety and performance are critical, such as in hydraulic presses, heavy lifting equipment, and deep-sea exploration.
These couplers are available in various materials, including high-strength steel and stainless steel, to accommodate different operating environments. They are designed to provide a secure and leak-free connection even under extreme pressure and vibration. Their durability and high-pressure capabilities make them essential for demanding hydraulic systems.
Threaded Hydraulic Couplers
Threaded hydraulic couplers are a fundamental type of connection, using screw threads to create a secure, leak-proof seal. They are widely used in various hydraulic systems due to their simplicity and reliability. These couplers are available in numerous thread standards, such as NPT, BSP, and metric, ensuring compatibility with diverse equipment.
The threaded design allows for a tight seal, preventing leaks under high pressure, making them suitable for applications requiring robust connections. They are commonly used in stationary hydraulic systems where frequent connection and disconnection are not required. Their simplicity and ease of installation make them a popular choice for many hydraulic applications.
Threaded couplers are available in various materials, including steel, stainless steel, and brass, to accommodate different operating conditions. They are commonly used in applications such as industrial machinery, agricultural equipment, and automotive systems. Their versatility and reliability make them a staple in hydraulic systems.
How to Choose the Best Hydraulic Couplers
Selecting the right hydraulic couplers is crucial for ensuring the efficiency, safety, and reliability of your hydraulic systems. A thorough evaluation of your application’s specific needs is the first step. Consider the system’s operating pressure, fluid type, and environmental conditions.
Understanding these factors will guide you in choosing couplers that can withstand the demands of your operation.
Key considerations include:
- Pressure Rating: Ensure the coupler’s pressure rating meets or exceeds the system’s maximum operating pressure.
- Fluid Compatibility: Select materials that are compatible with the hydraulic fluid to prevent corrosion or degradation.
- Application Requirements: Consider frequency of connections, space limitations, and environmental factors.
Next, assess the coupler’s design and material. Quick-disconnect couplers are ideal for applications requiring frequent connections, while threaded or flange couplers are better suited for high-pressure or permanent installations. Material selection is also vital; stainless steel is preferred for corrosive environments, while steel is suitable for standard applications. Look for couplers that meet industry standards and certifications to ensure quality and reliability.
Finally, consider the long-term implications of your choice. While initial cost is a factor, investing in high-quality couplers can prevent costly downtime and repairs. Evaluate the ease of maintenance and availability of replacement parts. Consider factors like leak prevention and fluid spillage to minimize environmental impact and maintain a clean work environment. By carefully considering these factors, you can choose the best hydraulic couplers for your specific needs.
Conclusion
In conclusion, selecting the best hydraulic coupler type depends heavily on the specific needs of your application. Threaded couplings offer reliability for static connections, while quick disconnects provide efficiency for frequent changes. Flange couplings are ideal for high-pressure systems, and camlocks offer rapid connections for fluid transfer. Each type has its unique strengths, making careful consideration essential.
Understanding these distinctions ensures optimal performance and minimizes downtime. Choosing the right coupler enhances system safety and efficiency, contributing to overall operational success.
For high-quality wholesale hydraulic couplers tailored to your needs, contact DF Hydraulics today. We offer a wide range of durable and reliable couplings at competitive prices.