Hydraulic couplings are essential components in hydraulic systems, facilitating the connection and disconnection of fluid lines. They enable efficient fluid transfer, ensuring seamless operation in diverse industrial and mobile applications. Understanding the different types, materials, and applications of hydraulic couplings is crucial for system optimization and maintenance.
This guide provides a comprehensive overview of hydraulic couplings, exploring their functionalities, selection criteria, and best practices. Whether you’re a seasoned engineer or a novice, this information will help you navigate the complexities of hydraulic systems and choose the right couplings for your needs.
What is Hydraulic Coupling
A hydraulic coupling is a component used to connect hydraulic hoses, pipes, and tubes within a hydraulic system. Its primary function is to facilitate the transfer of hydraulic fluid, enabling the transmission of power. These couplings are designed to withstand high pressures and prevent leaks, ensuring the efficient and safe operation of hydraulic machinery.
Hydraulic couplings come in a variety of types, each tailored to specific applications and requirements. They can be categorized based on their connection method, such as threaded, quick-disconnect, or flange couplings. The selection of the appropriate coupling is crucial for maintaining system integrity and preventing downtime due to leaks or component failures.
How Hydraulic Coupling Works
Hydraulic couplings function by creating a secure, leak-free connection between two or more components in a hydraulic system. The basic principle involves using mechanical force and sealing elements to contain pressurized fluid. When two coupling halves are joined, they form a tight seal that prevents fluid from escaping, allowing for efficient power transmission.
This is achieved through various mechanisms, including:
- Threaded Connections: These use screw threads to create a tight seal between the coupling halves.
- Quick Disconnects: These employ locking mechanisms that allow for rapid connection and disconnection, often using ball bearings or poppets.
- Flange Connections: These use bolted flanges and gaskets to create a strong, leak-proof seal, particularly in high-pressure applications.
Once connected, the coupling allows hydraulic fluid to flow freely through the system, enabling the operation of hydraulic actuators, motors, and other components. The coupling’s design ensures that the connection remains secure even under high pressure and vibration, maintaining the integrity of the hydraulic circuit.
Hydraulic Coupling Types
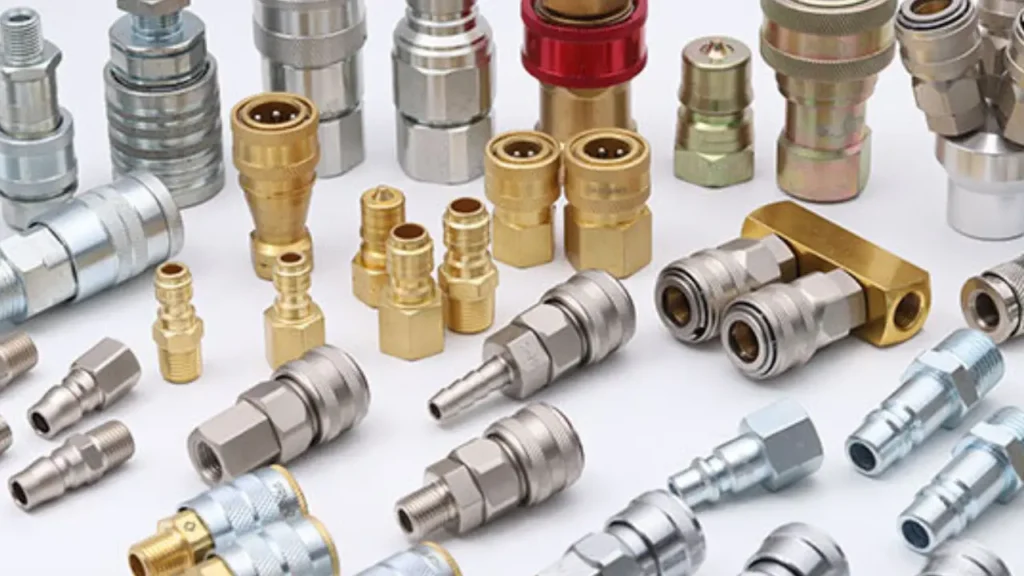
Hydraulic couplings are essential for connecting hydraulic hoses and pipes, ensuring efficient fluid transfer. Understanding their various types is crucial for selecting the right coupling for your application. Here are common hydraulic coupling types:
Threaded Hydraulic Couplings
Threaded hydraulic couplings utilize screw threads to create a secure connection between two components. They are widely used for their simplicity and reliability in various hydraulic systems. These couplings are available in numerous thread standards, such as NPT, BSP, and metric, ensuring compatibility with diverse equipment. The threaded design allows for a tight seal, preventing leaks under high pressure, making them suitable for applications requiring robust connections.
Quick Disconnect Hydraulic Couplings
Quick disconnect hydraulic couplings are designed for rapid connection and disconnection of hydraulic lines without the need for tools. They feature a locking mechanism, often using ball bearings or poppets, that allows for easy engagement and disengagement. These couplings are ideal for applications requiring frequent connection changes or maintenance, such as mobile hydraulic equipment or test benches. Their efficiency reduces downtime and simplifies system modifications.
Flange Hydraulic Couplings
Flange hydraulic couplings use bolted flanges and gaskets to create a strong, leak-proof seal. They are commonly used in high-pressure applications where a robust connection is essential. Flange couplings provide a reliable seal even under extreme conditions, making them suitable for heavy-duty industrial systems. They are typically used for larger diameter pipes and hoses, ensuring a secure and stable connection in demanding environments.
Camlock Hydraulic Couplings
Camlock hydraulic couplings, also known as cam and groove couplings, provide a quick and simple way to connect and disconnect hoses. They use a cam-operated locking mechanism that allows for rapid engagement and disengagement without tools. These couplings are widely used in fluid transfer applications, such as chemical, petroleum, and industrial settings. Their ease of use and versatility make them a popular choice for temporary or frequent connections.
How to Use Hydraulic Quick Coupling

Hydraulic quick couplings streamline fluid line connections, offering rapid engagement and disengagement. Proper usage ensures safety and efficiency. This guide details the essential steps for effectively using hydraulic quick couplings, from inspection to disconnection, ensuring seamless hydraulic system operation.
Step 1: Inspect the Couplings
Before connecting any hydraulic quick couplings, meticulously inspect both the male and female halves. Ensure they are clean and free from debris, dirt, or any foreign particles that could obstruct fluid flow or damage the sealing surfaces. Check for signs of wear, damage, or corrosion, such as scratches, dents, or rust. A thorough inspection is vital to prevent leaks and ensure a proper, secure connection. Any damaged couplings should be replaced immediately.
Step 2: Prepare the Hydraulic System
Prior to engaging the quick couplings, ensure the hydraulic system is depressurized. This step is crucial for safety and to prevent fluid spray or accidental disconnection under pressure. If possible, shut off the hydraulic pump and release any residual pressure in the lines. This preparation ensures a safe and controlled connection process, minimizing the risk of injury or system damage.
Step 3: Align and Connect the Couplings
Carefully align the male and female halves of the quick coupling. Most quick couplings feature a push-to-connect mechanism. Gently push the male half into the female half until you hear or feel a distinct click, indicating that the locking mechanism has engaged. Some couplings may require a slight twisting motion to ensure a secure connection. Verify that the locking collar or sleeve is fully engaged and locked in place.
Step 4: Test the Connection
After connecting the couplings, perform a visual inspection to confirm that they are properly seated and locked. Gently tug on the connected couplings to ensure they are securely fastened and will not disconnect under pressure. If the system is safe to pressurize, slowly introduce pressure while observing the coupling for any signs of leaks or instability. If any leaks are detected, immediately depressurize the system and re-inspect the connection.
Step 5: Disconnect the Couplings (If Necessary)
To disconnect the quick couplings, first, ensure the hydraulic system is depressurized. Most quick disconnect couplings have a release mechanism, such as a collar or sleeve that needs to be pulled back or twisted. Pull back the collar or sleeve to release the locking mechanism, and then gently pull the male and female halves apart. If the couplings are under residual pressure, a small amount of fluid may escape during disconnection. Always perform this step with care and in a safe manner.
How to Choose the Best Hydraulic Couplings
Selecting the right hydraulic couplings is crucial for ensuring efficient and leak-free hydraulic system performance. This guide provides a step-by-step approach to help you choose the best hydraulic couplings for your specific needs, considering factors like pressure, fluid type, and application requirements.
Step 1: Determine the Operating Pressure
The first step in choosing hydraulic couplings is to determine the maximum operating pressure of your hydraulic system. This information is critical, as couplings are rated for specific pressure levels. Selecting a coupling with a pressure rating lower than your system’s operating pressure can lead to leaks, failures, and potential safety hazards. Always choose couplings that meet or exceed the maximum pressure requirements to ensure safe and reliable operation.
Step 2: Identify the Fluid Type
Different hydraulic fluids have varying chemical properties that can affect coupling materials. Identify the type of fluid your system uses, such as hydraulic oil, water-glycol, or other specialized fluids. This will help you select couplings made from compatible materials that resist corrosion and degradation. For example, stainless steel couplings are often preferred for corrosive fluids, while standard steel couplings are suitable for mineral oil-based fluids.
Step 3: Consider the Application Requirements
The specific application of your hydraulic system will influence the type of coupling needed. Consider factors such as frequency of connection and disconnection, environmental conditions, and space limitations. For applications requiring frequent connections, quick disconnect couplings are ideal. For high-pressure or heavy-duty applications, flange or threaded couplings may be more suitable. If your system operates in harsh environments, choose couplings with appropriate corrosion resistance and sealing capabilities.
Step 4: Evaluate the Coupling Material and Size
The material and size of the coupling are essential for ensuring compatibility and performance. Select couplings made from materials that are compatible with the fluid and operating environment. Consider the size and thread type required to match your hydraulic hoses and components. Ensure the coupling’s dimensions are appropriate for your system’s layout and space constraints. Choosing the correct material and size will prevent leaks and ensure optimal performance.
Step 5: Check for Certifications and Standards
Ensure the hydraulic couplings you choose meet relevant industry standards and certifications. This guarantees that the couplings have been tested and verified for quality and performance. Look for certifications such as ISO, SAE, or other industry-specific standards. Purchasing certified couplings provides assurance of reliability and safety, reducing the risk of failures and ensuring compliance with regulatory requirements.
How to Measure Hydraulic Quick Coupler
Accurate measurement of hydraulic quick couplers is essential for ensuring compatibility and proper function within your hydraulic system. This guide provides a step-by-step approach to help you measure hydraulic quick couplers effectively, covering key dimensions and considerations.
Step 1: Identify the Coupler Type
Before measuring, determine the type of quick coupler you have. Common types include ball-type, poppet-type, and flat-face couplers. Identifying the type helps you understand the specific dimensions that need to be measured and the tools required. Each type has unique features that affect how measurements are taken.
Step 2: Measure the Body Size
Measure the outer diameter of the coupler body. This measurement is crucial for determining the overall size and compatibility of the coupler with your system. Use a caliper or measuring tape for accurate readings. Record the diameter in millimeters or inches, depending on your system’s specifications. The body size is a fundamental dimension for identifying the coupler’s series and pressure ratings.
Step 3: Measure the Thread Size and Type
Identify and measure the thread size and type of both the male and female coupler halves. Common thread types include NPT, BSP, and metric. Use a thread gauge or caliper to measure the thread diameter and pitch. This measurement is critical for ensuring compatibility with your hydraulic hoses and fittings. Accurate thread measurement prevents leaks and ensures a secure connection.
Step 4: Measure the Valve Size
For poppet-type or flat-face couplers, measure the diameter of the internal valve or poppet. This measurement determines the flow capacity of the coupler. Use a caliper to measure the valve diameter accurately. The valve size affects the flow rate and pressure drop within the hydraulic system, ensuring optimal performance.
Step 5: Measure the Overall Length
Measure the overall length of the coupler, including any extensions or fittings. This measurement is important for ensuring the coupler fits within the available space in your hydraulic system. Use a measuring tape or caliper to obtain the overall length. The overall length helps determine if the coupler is compatible with the system’s layout and design.
Conclusion
In conclusion, hydraulic couplings are essential components in fluid power systems, enabling efficient and secure connections. Understanding their types, materials, and applications is crucial for optimizing performance and preventing costly failures. Proper selection and maintenance ensure system reliability and longevity. From quick disconnects to threaded couplings, each type serves specific needs within diverse hydraulic applications.
This guide has provided a comprehensive overview, highlighting the importance of choosing the right coupling for your system. We hope this information empowers you to make informed decisions.
For high-quality wholesale hydraulic couplings, contact DF Hydraulics today. We offer a wide selection of durable and reliable couplings to meet your specific needs.