Measuring NPT (National Pipe Thread) fittings accurately is essential for ensuring proper fit, functionality, and performance in a wide range of applications.
Whether you’re working on plumbing, industrial systems, or fluid control systems, precise measurements of NPT fittings are crucial for preventing leaks, ensuring system efficiency, and maintaining safety standards.
In this guide, I’ll walk you through the entire process of how to measure NPT fittings, offering detailed instructions, common tools, and tips that I’ve learned from hands-on experience. By the end, you’ll know exactly how to measure NPT fittings for any project.
If you have any questions about the content, feel free to contact us directly.
What is a NPT Fitting?
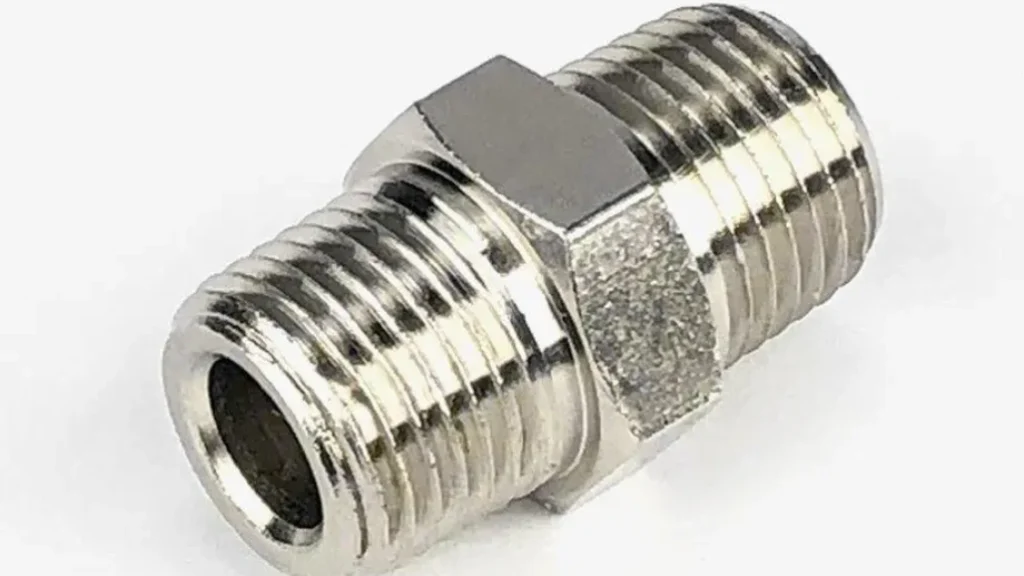
NPT fittings are designed with tapered threads, which create a seal as the fitting is screwed into a matching pipe or component. The tapered nature of NPT threads (a 1/16 inch per inch taper) allows for a tight, leak-resistant connection. These fittings are widely used in plumbing, automotive, oil and gas, and industrial systems.
Structure of NPT Fittings
NPT fittings feature a distinct set of threads that are designed to create a seal when they tighten. They are differentiated from other types of threads by their angle (60 degrees) and taper. The outer thread diameter gets smaller as it moves down the fitting.
Common Sizes of NPT Fittings
The size of an NPT fitting is typically defined by its nominal diameter. Here’s a table of the most common NPT fitting sizes and their associated measurements:
NPT Size | Major Diameter (inches) | Minor Diameter (inches) | Pitch (Threads per inch) |
1/8″ | 0.405 | 0.302 | 27 |
1/4″ | 0.54 | 0.417 | 18 |
3/8″ | 0.675 | 0.539 | 18 |
1/2″ | 0.84 | 0.67 | 14 |
3/4″ | 1.05 | 0.866 | 14 |
1″ | 1.315 | 1.05 | 11 |
1-1/4″ | 1.66 | 1.292 | 11 |
1-1/2″ | 1.9 | 1.515 | 11 |
Applications and Features
NPT fittings are known for their versatility. They are commonly used in plumbing, heating systems, gas lines, and hydraulic systems due to their ability to create leak-proof seals. The most important features of NPT fittings include:
- Leakproof seal: The tapered design helps to form a reliable seal.
- Versatility: Used in a variety of systems, including water, gas, and oil lines.
- Ease of use: Can be hand-tightened without requiring specialized equipment, though they still need proper measurement for accuracy.
The Importance of Measuring NPT Fittings
Accurate measurement of NPT fittings is crucial for several reasons:
- Ensure proper fit: Incorrect measurements can result in fittings not matching the pipes, causing leaks or system failures.
- Maintain system integrity: Accurate measurement helps avoid under-tightening or over-tightening, both of which can compromise the system.
- Compliance with standards: Many industries have strict regulations regarding thread measurements. Ensuring measurements are correct is necessary for regulatory compliance.
How to Measure NPT Fittings
Measuring NPT fittings requires specialized tools and a clear understanding of how to measure each dimension properly. Here’s a step-by-step breakdown of the process.
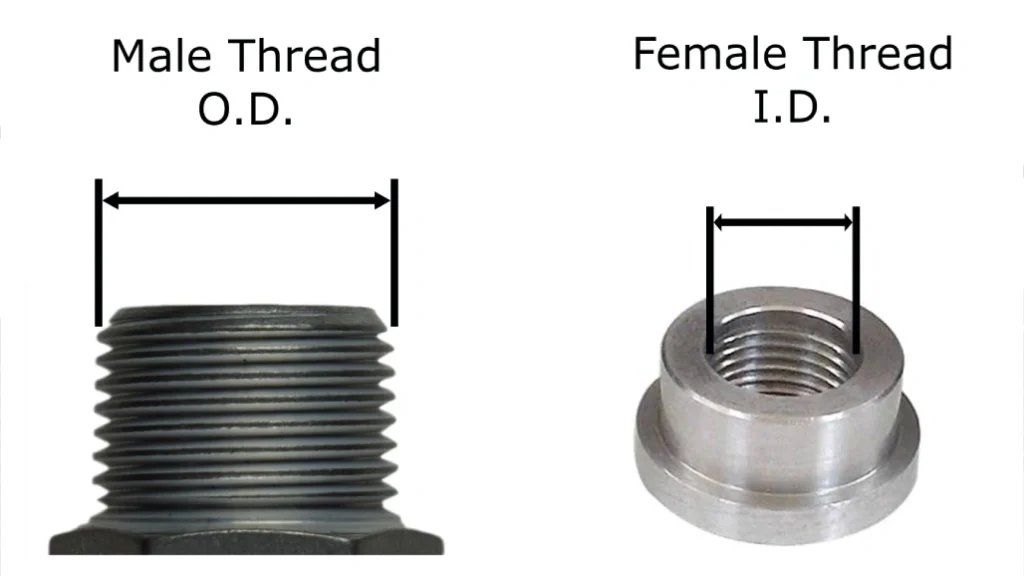
Measuring External Threads
Step 1: Measuring the Major Diameter
Using my digital calipers, I place the jaws of the calipers around the outermost part of the male NPT thread. I make sure to measure at several points along the length of the thread to account for any taper. The measurement should be taken perpendicular to the axis of the thread.
One important thing to note is that the major diameter of an NPT thread is not a constant value due to the taper. I record the largest measurement obtained as the major diameter.
Step 2: Measuring the Pitch Diameter
Using a Thread Micrometer:
I adjust the thread micrometer to fit the threads of the NPT fitting. The anvils of the thread micrometer are designed to contact the flanks of the threads at the pitch diameter. I carefully position the micrometer and take the reading.
It’s important to ensure that the micrometer is perpendicular to the axis of the thread for an accurate measurement.
Three – Wire Method:
First, I select three precision wires of the appropriate diameter. I place the wires in the thread grooves, two on one side and one on the opposite side.
Then, using a regular micrometer, I measure the distance over the wires. I use a specific formula to calculate the pitch diameter from this measurement.
The formula takes into account the wire diameter, the number of threads per inch, and the measured distance over the wires.
Step 3: Measuring the Minor Diameter
I use the calipers to measure the innermost part of the male NPT thread. Similar to measuring the major diameter, I measure at multiple points along the thread length due to the taper.
I record the smallest measurement as the minor diameter. One common error to avoid is measuring at an angle, which can give an incorrect value for the minor diameter.
Step 4: Measuring the Thread Pitch
I take a thread gauge from my set and try to match it to the threads on the NPT fitting. I carefully place the gauge on the threads and check if the teeth of the gauge fit perfectly into the threads.
Once I find the correct gauge that fits snugly, I note down the number of threads per inch. This value is crucial as it determines the thread specification of the NPT fitting.
Step 5: Measuring the Thread Angle
Using a universal angle gauge, I place the gauge against the flanks of the NPT thread. I make sure to position the gauge accurately to measure the angle between the flanks of the thread. The standard thread angle for NPT fittings is 60 degrees.
Any deviation from this angle can affect the performance of the fitting. I take multiple measurements at different points along the thread to ensure accuracy.
Measuring Internal Threads
Step 1: Measuring the Major Diameter
For measuring the major diameter of the female NPT thread, I use a special inside – diameter caliper or a bore gauge. I insert the measuring tool into the female thread and carefully expand it until it touches the innermost part of the thread. I make sure to measure at several points along the length of the thread to account for the taper.
Step 2: Measuring the Pitch Diameter
I use a pipe thread plug gauge. I insert the plug gauge into the female NPT thread. The plug gauge has a series of steps or bands that represent different pitch diameters. If the plug gauge goes in and out smoothly with a proper fit, then the pitch diameter of the female thread is within the acceptable range. If it is too tight or too loose, then the pitch diameter may be incorrect.
Step 3: Measuring the Minor Diameter
I use a small-diameter caliper or a specialized tool to measure the outermost part of the female NPT thread. Similar to measuring the major diameter, I measure at multiple points along the thread length. I need to be careful not to damage the threads while measuring the minor diameter.
Step 4: Measuring the Thread Pitch and Angle
Measuring the thread pitch for internal threads is similar to external threads. I use a thread gauge to determine the number of threads per inch. For measuring the thread angle, I can use a small – sized angle gauge or a specialized tool designed for internal threads.
The key difference compared to external thread measurement is the access and the tools required. I need to be more careful with internal thread measurements as the tools may not be as easy to position accurately.
Data Handling and Analysis for Measure NPT Fittings
Step 1: Handling Measurement Data
After completing the measurements, it’s essential to handle your data accurately:
- Record Multiple Measurements: Always take multiple measurements for consistency. Use the average of your measurements if there is any discrepancy.
- Identify Anomalies: If any measurements are out of specification, it’s important to identify the cause (incorrect tool calibration, improper measuring technique, etc.).
Step 2: Checking Measurement Conformance
Once you have your measurements, compare them to the relevant NPT standards to ensure that they meet the requirements.
If the measurements are not in line with standards, adjustments may be needed, such as using different fittings or changing the measurement tools.
Key Considerations for Measure NPT Fittings
Safety Precautions
When measuring NPT fittings, especially in an industrial setting, I always wear safety glasses to protect my eyes from any debris that may fly off during the cleaning or measurement process. If the fittings are part of an active system, I ensure that the system is depressurized before starting the measurement.
Tool Maintenance
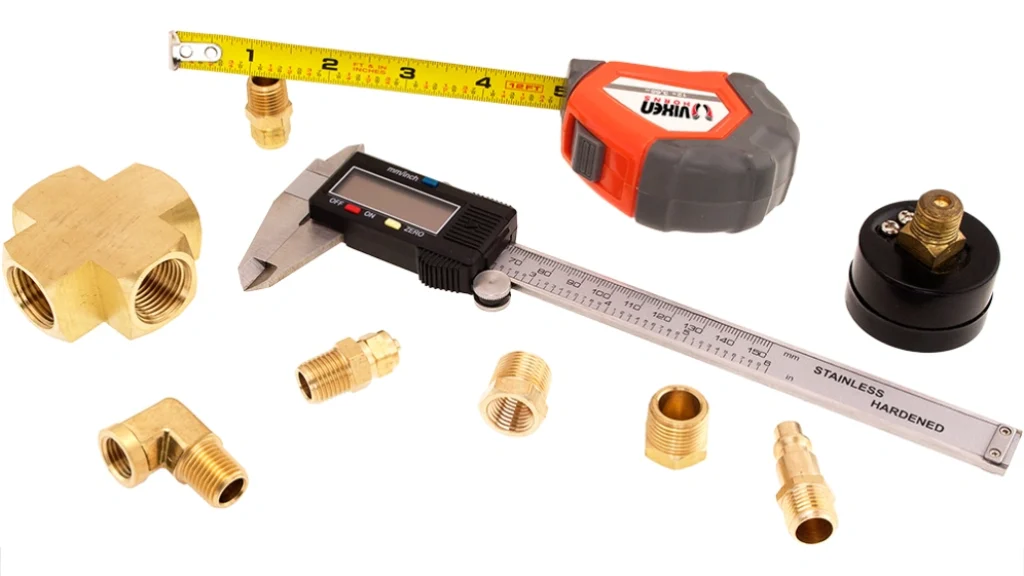
Regular maintenance of the measurement tools is crucial. I clean the tools after each use to prevent the accumulation of dirt and debris. I also check for any signs of wear or damage and replace any damaged parts promptly. For example, if the jaws of a caliper are bent, it can affect the accuracy of the measurement.
Documentation
I keep detailed documentation of all the measurements I perform. This includes the measurement data, the results of the analysis, and any actions taken based on the results, such as replacing a fitting that did not meet the standards. The documentation is useful for future reference and for quality control purposes.
Conclusion
Accurately measuring NPT fittings is a multi – step process that requires the right tools, proper preparation, and careful execution.
By following the steps outlined in this article, you can ensure that your NPT fittings are measured correctly, which is essential for the safe and efficient operation of any piping or fluid system. If you are interested in our products, you can visit our homepage or ask us for a product catalog.
FAQs About How to Measure NPT Fittings
How do you determine NPT fitting size?
NPT fitting size is typically determined by measuring the major, minor, and middle diameters, along with the thread pitch. Compare these measurements to standard NPT dimensions to determine the fitting size.
What is the OD of a 1/2 NPT fitting?
The outer diameter (OD) of a 1/2 NPT fitting is typically 0.840 inches. This measurement refers to the major diameter of the external threads.
How to measure pipe fitting thread size?
Measure the major, minor, and middle diameters of the fitting’s threads using a caliper or micrometer. Additionally, check the thread pitch using a pitch gauge to ensure the fitting is the correct size.
What is the actual size of a 1-inch NPT connection?
The actual size of a 1-inch NPT fitting includes a major diameter of approximately 1.315 inches and a pitch of 11 threads per inch.
Where to buy fittings?
You can purchase high-quality NPT fittings from us. Our brand, Dingfeng, offers a full range of fittings. We provide customized solutions to meet your specific needs. Feel free to contact us for more details or to get our product catalog.