When it comes to industrial applications, whether in hydraulic systems, plumbing, or machinery, the importance of reliable and well-built connections cannot be overstated. One such essential component is the NPT fitting. But what is an NPT fitting exactly?
In this article, I’ll dive into the details of NPT fittings, their manufacturing processes, common types, and how they’re used. Drawing from my own experience in this industry, I’ll also share insights into why choosing the right NPT fitting is critical for ensuring safety and efficiency in your systems.
What is NPT Fitting? Understanding the Basics
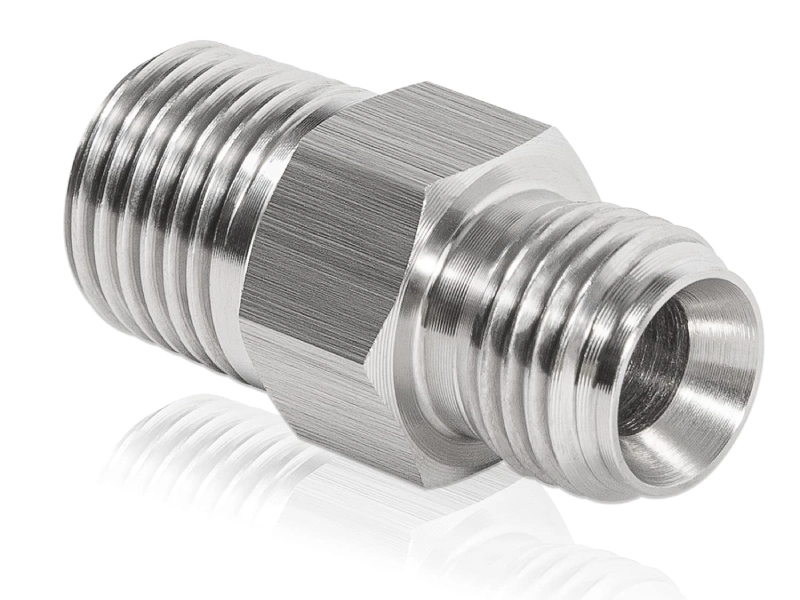
NPT stands for National Pipe Tapered Thread, which is a standard for tapered threads used on pipes and fittings in the United States. These fittings are designed to seal fluid and gas flow effectively by creating a tight, leak-proof connection as the threads tighten.
The primary feature that distinguishes NPT fittings from other types of fittings is the tapered design.
NPT threads are cut at a specific angle of 60 degrees, with the threads getting progressively deeper as you move down the pipe. This tapering ensures that as the male and female parts of the fitting are screwed together, they create a compression seal that prevents leaks.
Types of NPT Fittings
There are several types of NPT fittings, and each has specific applications depending on the fluid or gas being transferred, pressure levels, and the overall system design. Below, I’ll outline the most common types:
1. Male and Female NPT Fittings

Male NPT Fittings: These are fittings with tapered threads on the outside, meant to be screwed into a corresponding female NPT fitting.
Female NPT Fittings: These have tapered threads on the inside, allowing them to receive male NPT fittings securely.
2. NPT Elbows
NPT elbows are used to change the direction of flow in a system, typically at 90-degree angles. These are common in both plumbing and hydraulic systems.
3. NPT Tees
NPT tees are used to split a flow of fluid or gas in a system into two directions. They are available in various sizes depending on the specific needs of the application.
4. NPT Couplings
NPT couplings are used to join two pipes or fittings together. These can be either male or female, and their role is to create a longer, more continuous pipe or hose.
5. NPT Adapters
These fittings allow the connection of pipes with different thread types. For example, a male NPT fitting can be connected to a female BSP (British Standard Pipe) fitting using an NPT adapter.
6. NPT Plugs and Caps
These are used to block off or seal open ends of pipes or other fittings in a system.
The Manufacturing Process of NPT Fittings
The manufacturing process of NPT fittings involves several critical steps to ensure the precision and durability of the product. Here’s an overview of how these fittings are produced:
Material Selection:
NPT fittings are typically made from stainless steel, brass, carbon steel, or aluminum, depending on the intended use. For high-pressure systems or corrosive environments, stainless steel is a common choice due to its resistance to rust and corrosion.
Thread Cutting:
The hallmark of NPT fittings is their tapered thread design. This is achieved through a precise thread-cutting process using specialized machines. The threads are carefully cut at a 60-degree angle, ensuring that they will provide a tight seal when two fittings are joined.
Quality Control:
Every fitting undergoes rigorous quality control testing to ensure that the threads are accurately formed and that the fitting will function as expected. This includes pressure testing and leak detection.
Surface Treatment:
Some NPT fittings undergo surface treatments like plating or coating to enhance their corrosion resistance, especially if they are going to be used in harsh environments, such as marine or chemical processing systems.
Packaging:
After passing quality checks, NPT fittings are cleaned, packaged, and prepared for shipment to suppliers or customers.
How NPT Fittings Work and Their Applications?
NPT fittings are used across various industries where a strong, leak-proof connection is required. Some of the most common applications include:
Hydraulic Systems:
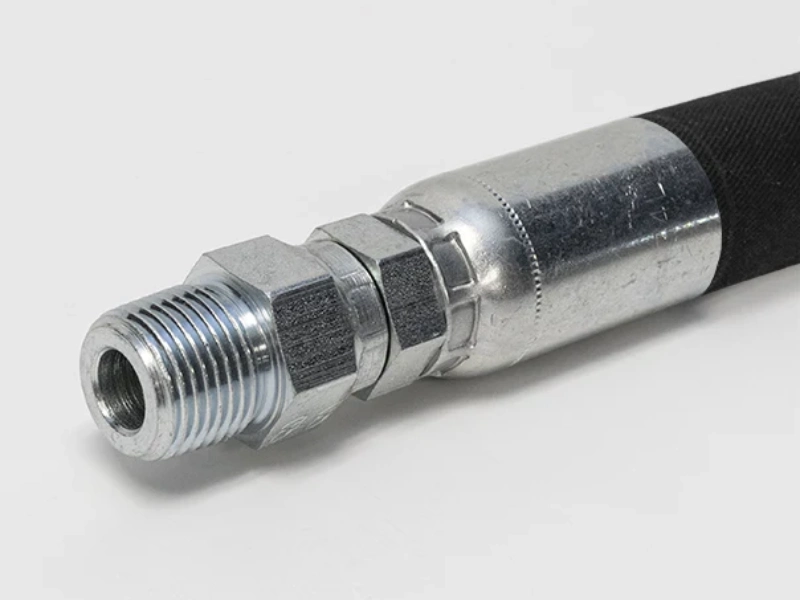
In hydraulic systems, NPT fittings are used to connect hoses, pumps, and valves. The taper of the threads ensures a leak-free connection even under high pressure.
Plumbing Systems:
NPT fittings are widely used in residential and commercial plumbing systems. They are ideal for joining pipes carrying water, natural gas, or other fluids.
Automotive and Aerospace:
The aerospace and automotive industries rely on NPT fittings for fluid lines, air systems, and more. The ability to withstand high pressure and temperature makes NPT fittings essential in these applications.
Oil and Gas:
The oil and gas industry uses NPT fittings for pipelines, drilling equipment, and pressure vessels. These fittings help prevent leaks and maintain safe fluid transport.
Industrial Manufacturing:
Many factories use NPT fittings in machinery and equipment that require durable connections for fluid transfer. They can be found in everything from compressors to air tools.
How to Use NPT Fittings Correctly?
Using NPT fittings correctly is essential to ensuring a safe and effective connection. Here are some key guidelines to follow:
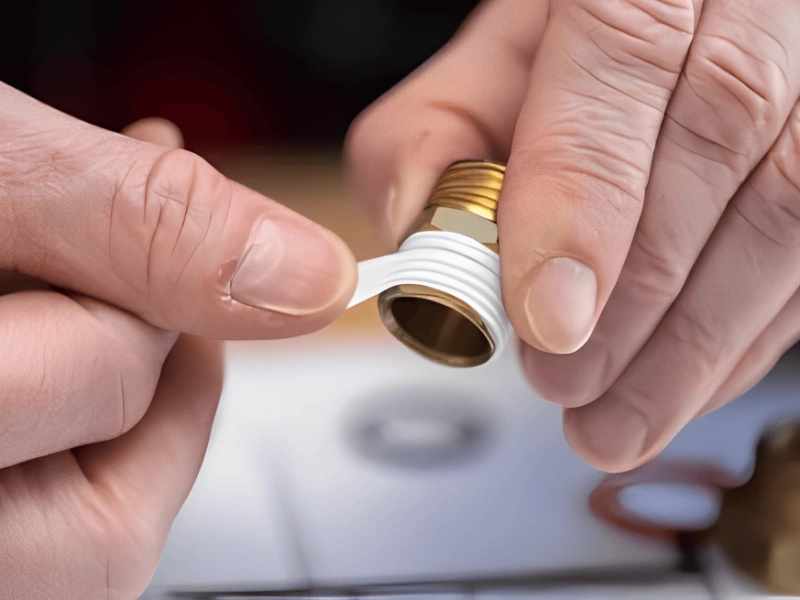
1. Check Compatibility:
Before using NPT fittings, make sure they are compatible with the pipes or equipment you intend to connect. Ensure the sizes and thread types match.
2. Use Thread Sealant:
While NPT threads create a tight seal, it’s often a good idea to apply a thread sealant, such as Teflon tape or pipe dope, to enhance the sealing and prevent leaks, especially in high-pressure systems.
3. Proper Torque:
When connecting male and female NPT fittings, it’s essential to apply the correct amount of torque. Over-tightening can cause damage, while under-tightening can result in leaks.
4. Inspect Regularly:
NPT fittings should be regularly inspected for wear and tear. Look for signs of corrosion, cracks, or thread damage. Replace any fittings that are damaged or worn.
Conclusion
Understanding what NPT fittings are and how they work is crucial for selecting the right components for your industrial systems. These fittings offer reliable, leak-proof connections that are essential in a wide range of applications, from plumbing to high-pressure hydraulic systems. By following proper installation practices and choosing the right fittings for your needs, you can ensure the longevity and safety of your systems.
FAQs
What is the difference between NPT and BSP fittings?
NPT (National Pipe Thread) and BSP (British Standard Pipe) are two different thread standards. NPT fittings have tapered threads, while BSP fittings can have either tapered or parallel threads. It’s important to match the correct fitting type to avoid leaks.
what is the difference between mip and npt copper fittings?
When it comes to plumbing and piping systems, understanding the differences between MIP (Male Iron Pipe) and NPT (National Pipe Thread Tapered) copper fittings is crucial for ensuring proper connections. Both types of fittings are designed to connect pipes, but they have distinct characteristics that set them apart.
Thread Design
NPT Fittings: The key feature of an NPT fitting is its tapered thread. This means that the diameter of the threads decreases as you move from the base to the tip of the male thread or from the opening inward on the female thread. The tapering creates a tighter seal as the components are screwed together, which is especially important in applications requiring high pressure or where liquids or gases must not leak.
MIP Fittings: MIP refers to a straight, non-tapered male thread that is intended to screw into a female iron pipe (FIP) fitting with parallel threads. Unlike NPT, MIP threads do not tighten further upon continued turning; instead, they rely on the initial engagement for sealing, often augmented by a washer or other sealing materials.
Material and Application
NPT Fittings: While NPT can be made from various materials including brass, steel, stainless steel, and plastic, when discussing copper specifically, NPT copper fittings are used widely in gas and liquid applications where a tight seal is necessary. They are common in industrial settings such as oil refineries, chemical plants, and hydraulic systems.
MIP Fittings: Copper MIP fittings are less common than NPT ones because copper is more typically associated with water supply lines and heating systems. MIP threads on copper fittings are usually found in residential plumbing, where lower pressures and temperatures are encountered, and sometimes in conjunction with other types of pipe like PVC or PEX.
Sealing Method
NPT Fittings: The tapered nature of NPT threads means that the seal is created by the interference fit between the male and female threads. Sealant, such as Teflon tape or pipe dope, is often applied to the threads to ensure a watertight or airtight seal.
MIP Fittings: Since MIP threads are straight, they do not create a self-sealing connection. Therefore, a separate sealing mechanism is required, such as a rubber O-ring, neoprene washer, or thread sealant.
Installation Considerations
NPT Fittings: When installing NPT fittings, care must be taken not to over-tighten, as this can cause damage to the threads and compromise the seal. A torque wrench may be used to apply the correct amount of force.
MIP Fittings: Installation of MIP fittings is generally straightforward, but it’s important to ensure that the mating FIP component has the corresponding internal straight thread. Over-tightening is also a concern here, as it can lead to stripping of the threads.
In summary, while both MIP and NPT copper fittings serve to connect pipes, their differences lie in thread design, sealing method, material choice, and typical applications. Selecting the right type of fitting depends on the specific requirements of the system being assembled.
Can NPT fittings be used for gas lines?
Yes, NPT fittings are commonly used in gas lines. The tapered threads provide a tight, secure seal that prevents gas leaks, making them suitable for both water and gas systems.
How do I choose the right NPT fitting for my system?
To choose the right NPT fitting, consider factors like the size of the pipe, the type of fluid being transported, the pressure rating, and whether you need additional features like corrosion resistance.
Can NPT fittings be reused?
While NPT fittings can technically be reused, it’s not always advisable. Over time, the threads may wear down, leading to a weaker seal. Always inspect fittings before reusing them.
Are NPT fittings pressure rated?
Yes, NPT fittings are rated for various pressure levels. Always ensure that the NPT fittings you choose are rated for the maximum pressure in your system.