Swivel joints are integral components in fluid transfer systems, enabling rotational movement while maintaining a secure connection. This guide explores their diverse applications and functionalities, offering insights into their design and selection. These joints facilitate flexible hose or pipe connections, preventing twisting and kinking, thus enhancing system efficiency and longevity.
Understanding swivel joints is crucial for various industries, from manufacturing to oil and gas. This guide provides a comprehensive overview of their types, materials, and operational principles. By delving into their specifications and applications, you’ll gain the knowledge to choose the right swivel joint for your specific needs.
What is a Swivel Joint
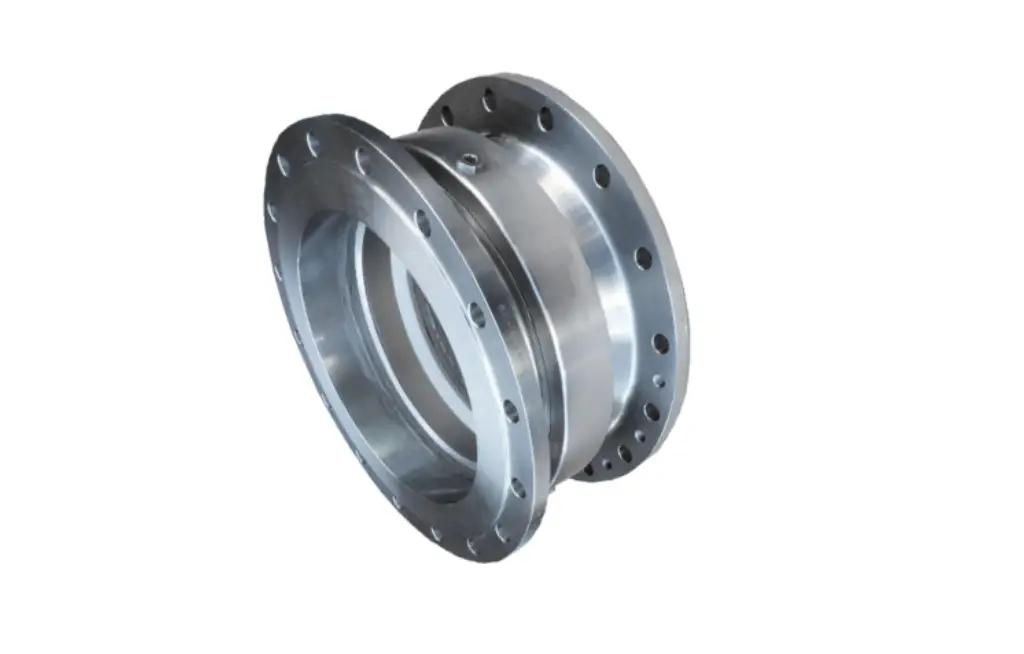
A swivel joint is a mechanical connection that allows for rotational movement between two components in a fluid transfer system. It’s designed to prevent twisting and kinking of hoses or pipes, enabling flexibility and maneuverability in applications where fluid or gas is conveyed under pressure. These joints are critical in industries ranging from chemical processing and oil and gas to hydraulic systems and manufacturing, where rotational movement is essential.
Swivel joints typically consist of an inner and outer race with a bearing system that facilitates rotation. They are engineered to maintain a leak-free seal while allowing for varying degrees of rotation, from 360 degrees continuous rotation to limited angular movement. The materials and design of swivel joints are selected based on the specific application requirements, including the type of fluid or gas being conveyed, the operating pressure and temperature, and the degree of rotational freedom needed.
What is a Swivel Joint Made of
Swivel joints are constructed from a variety of materials, carefully selected to withstand the specific operating conditions and fluid types they encounter. Common materials include carbon steel, stainless steel, brass, and aluminum.
The choice of material depends on factors such as corrosion resistance, pressure ratings, temperature tolerances, and the compatibility with the fluid being transferred. For corrosive environments or applications involving aggressive chemicals, stainless steel or specialized alloys are preferred.
The internal components of a swivel joint, such as bearings and seals, are also made from specific materials to ensure smooth rotation and leak-free operation. Bearings are often made from hardened steel or stainless steel, while seals can be made from elastomers like Viton, PTFE, or nitrile rubber, depending on the fluid and temperature requirements. Each component’s material is chosen to contribute to the joint’s overall durability and reliability.
- Carbon Steel: For general industrial applications with non-corrosive fluids.
- Stainless Steel: For corrosive environments and high-purity applications.
- Brass: For low-pressure applications and compatibility with certain fluids.
- Aluminum: For lightweight applications and reduced system weight.
- Viton, PTFE, Nitrile Rubber: Seal materials for various fluid and temperature compatibilities.
How Do Swivel Joints Work
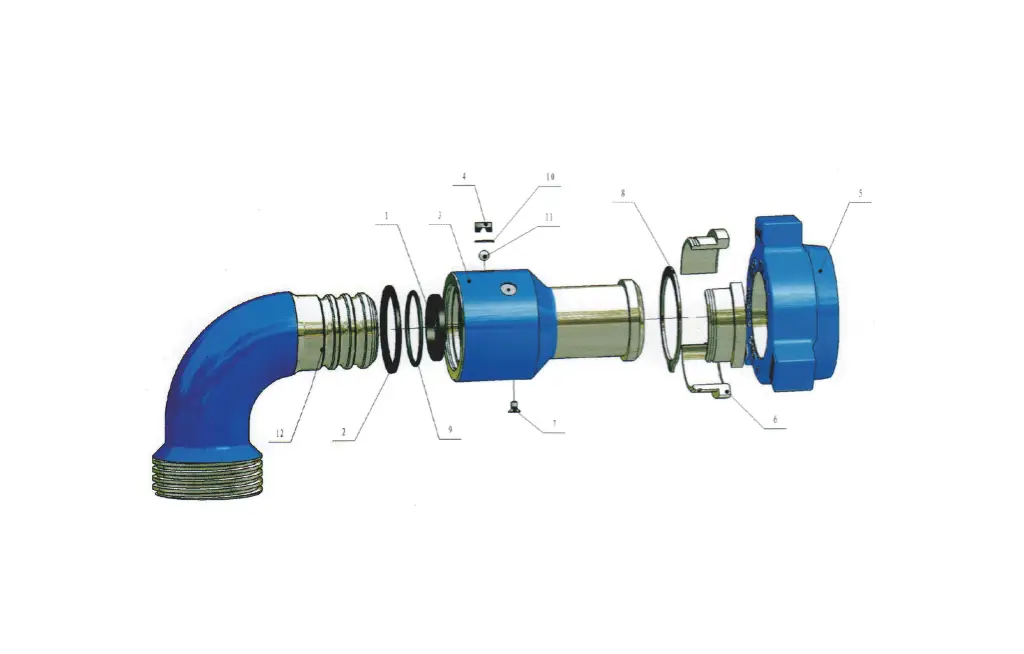
Swivel joints function by allowing rotational movement between two connected components while maintaining a fluid-tight seal. This is typically achieved through an inner and outer race, with bearings positioned between them to facilitate smooth rotation.
The design minimizes friction and wear, ensuring long-term reliability. The sealing mechanism, often involving O-rings or other specialized seals, prevents leaks under varying pressures and temperatures.
The joint’s ability to rotate is crucial in applications where hoses or pipes are subjected to twisting or bending forces. By allowing rotation, swivel joints prevent damage and extend the lifespan of connected components. The internal design also accommodates different degrees of rotation, from limited angular movement to continuous 360-degree rotation, depending on the application’s requirements.
- Inner and outer race design for smooth rotation
- Bearing system to minimize friction
- Sealing mechanism (O-rings, specialized seals) to prevent leaks
- Accommodation of varying degrees of rotation
- Prevention of hose or pipe damage from twisting and bending
Swivel Joint Types

Swivel joints are integral components in fluid transfer systems, designed to accommodate rotational movement while maintaining a secure connection. Understanding their various types is crucial for selecting the appropriate joint for specific applications.
Here are common swivel joint types in the following:
In-Line Swivel Joints
In-line swivel joints are designed for applications where rotational movement is required along a straight axis. They are typically used to prevent twisting of hoses or pipes that run in a linear direction. These joints are often found in hydraulic systems, where they allow hoses to rotate without kinking or becoming damaged under pressure. Their compact design and ease of installation make them suitable for various industrial applications where space is limited and linear rotation is essential.
Elbow Swivel Joints
Elbow swivel joints incorporate an angled connection, typically 90 degrees, in addition to rotational movement. They are ideal for applications where fluid transfer requires both a change in direction and rotational flexibility. These joints are commonly used in robotic systems, spray equipment, and other applications where hoses or pipes need to move around obstacles or in confined spaces. The angled design allows for efficient routing and prevents stress on connections.
Rotary Swivel Joints
Rotary swivel joints are designed for continuous, 360-degree rotation. They are used in applications where constant rotation is required, such as in rotary tables, winding machines, and continuous casting processes. These joints are engineered to maintain a reliable seal under continuous rotation, ensuring uninterrupted fluid or gas transfer. They are often equipped with multiple bearings and advanced sealing mechanisms to withstand the demands of continuous operation.
High-Pressure Swivel Joints
High-pressure swivel joints are specifically designed to handle extreme pressures, often found in hydraulic and oil and gas applications. They are constructed from high-strength materials and incorporate robust sealing mechanisms to prevent leaks under high-pressure conditions. These joints are critical in applications where safety and reliability are paramount, such as in drilling equipment, hydraulic presses, and heavy-duty industrial machinery.
How to Build a Swivel Joint
Constructing a swivel joint requires precision and careful selection of materials to ensure reliable performance. The process involves several key steps, from component selection to assembly and testing. Each stage is crucial for creating a joint that can withstand the demands of its intended application. Here’s a breakdown of the construction process:
Step 1. Component Selection
The first step involves selecting appropriate materials and components based on the application’s requirements. This includes choosing the right materials for the inner and outer races, bearings, and seals. Material selection depends on factors such as operating pressure, temperature, fluid type, and environmental conditions. Bearings must be chosen to handle the load and rotational speed, while seals must provide a leak-free barrier.
Step 2. Machining and Fabrication
Once materials are selected, the components are machined and fabricated to precise dimensions. This includes turning, milling, and drilling the inner and outer races to ensure proper fit and alignment. Bearing seats are machined to tight tolerances to minimize play and ensure smooth rotation. Seal grooves are also machined to precise specifications to prevent leaks. The precision of these machining operations is critical for the joint’s performance.
Step 3. Bearing and Seal Installation
After machining, the bearings and seals are installed into the races. Bearings are carefully pressed or inserted into their seats, ensuring proper alignment and fit. Seals are installed into their grooves, ensuring a tight seal against the rotating components. Lubrication is applied to bearings and seals to reduce friction and wear. The installation process requires careful attention to detail to prevent damage to the bearings and seals.
Step 4. Assembly and Testing
The final step involves assembling the inner and outer races, bearings, and seals into a complete swivel joint. The assembly is then tested to ensure it meets performance specifications. Testing includes pressure testing to verify leak-free operation, rotational torque testing to ensure smooth rotation, and durability testing to assess long-term reliability. Any necessary adjustments or modifications are made based on the test results.
How to Fix Loose Swivel Joints
Loose swivel joints can compromise system integrity and lead to leaks or failures. Addressing these issues promptly is essential to maintain operational efficiency and safety. The repair process typically involves inspection, disassembly, component replacement, and reassembly. Here’s a step-by-step guide on how to fix loose swivel joints:
Step 1. Inspection and Diagnosis
The first step is to thoroughly inspect the swivel joint to identify the cause of the looseness. This involves checking for visible damage, excessive wear, or any signs of leakage. Assess the rotational movement to determine if it’s smooth or if there’s any binding or excessive play. A detailed inspection will help pinpoint the specific components that need attention or replacement.
Step 2. Disassembly
Once the problem is diagnosed, carefully disassemble the swivel joint. This typically involves removing retaining rings, bolts, or other fasteners that hold the components together. It’s crucial to document the disassembly process to ensure proper reassembly. Clean all components thoroughly to remove any debris or contaminants that may have contributed to the looseness. Pay attention to the condition of seals and bearings during disassembly.
Step 3. Component Replacement
After disassembly, inspect the bearings, seals, and races for wear or damage. Replace any worn or damaged components with new ones that meet the original specifications. Ensure that the new bearings and seals are properly lubricated before installation. If the races are damaged, they may also need to be replaced. Proper component selection is crucial for restoring the swivel joint’s performance.
Step 4. Reassembly and Testing
Reassemble the swivel joint in the reverse order of disassembly, ensuring that all components are properly aligned and secured. Apply appropriate torque to fasteners to prevent loosening during operation. After reassembly, conduct thorough testing to verify the joint’s performance. This includes pressure testing to check for leaks, rotational torque testing to ensure smooth movement, and visual inspection to confirm proper assembly. Perform operational testing under simulated working conditions, if possible, to verify the fix.
Conclusion
In conclusion, swivel joints are critical components enabling rotational movement in fluid transfer systems. Their versatility and durability make them indispensable across diverse industries, from chemical processing to hydraulic applications. Understanding their types, materials, and applications ensures optimal system performance. Proper selection and maintenance are paramount for longevity and safety.
Swivel joints offer flexibility and prevent hose twisting, enhancing operational efficiency. They accommodate various fluids and pressures, adapting to demanding environments. Regular inspections and timely replacements are essential to prevent leaks and system failures. Their design minimizes stress on hoses and pipes, extending equipment lifespan.
For high-quality wholesale swivel joints, contact DF Hydraulics today. We offer a comprehensive range of customizable solutions tailored to your specific needs. Partner with us for reliable and efficient fluid transfer systems. Get in touch to discuss your requirements and benefit from our expert services.