Flange fittings are essential components in various industries, including plumbing, construction, and manufacturing. They are crucial for connecting pipes, valves, and other equipment in a secure and reliable manner. This guide will delve into the world of flange fittings, exploring their types, applications, and key considerations for their selection and installation.
We will cover a wide range of topics, from understanding different flange types such as slip-on flanges, weld neck flanges, and blind flanges to exploring the materials used in their construction, including carbon steel, stainless steel, and other alloys.
This comprehensive guide will provide valuable insights for engineers, technicians, and anyone involved in the design, installation, and maintenance of piping systems.
What is a Flange Fitting
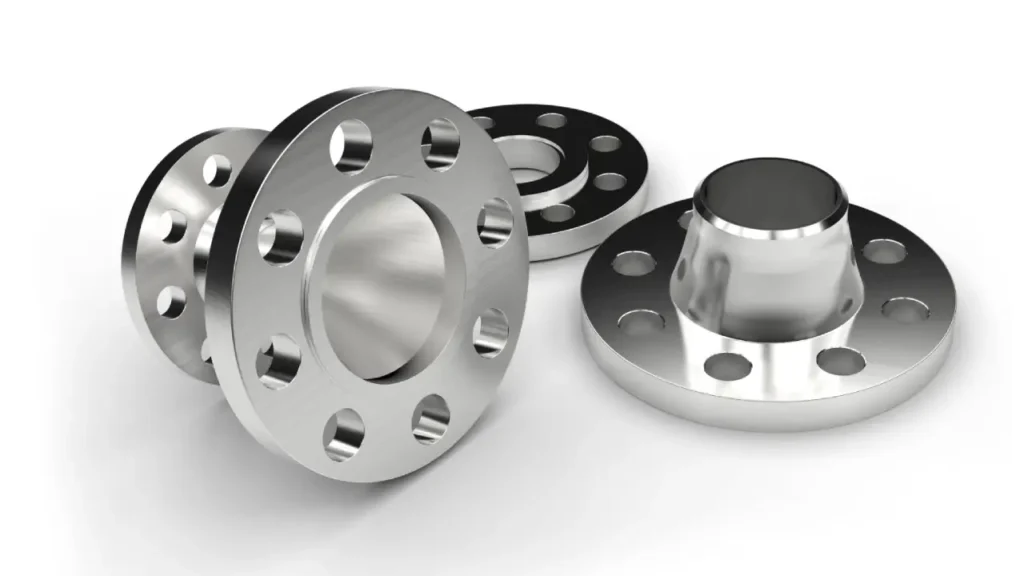
Flange fittings, also named flange pipe fittings are essential components in piping systems, serving as the crucial connection points between pipes, valves, pumps, and other equipment. They essentially consist of a pipe with a protruding rim or flange at one end. This flange, typically circular in shape, allows for a secure and easily assembled connection.
What Does a Good Flange Fit Look Like
A good flange fit for a breast pump is crucial for comfort and effective milk expression. Ideally, the nipple should move freely within the flange’s tunnel without touching the sides. This prevents friction and potential damage.
The flange should be large enough to accommodate the nipple comfortably without pinching or squeezing. However, it shouldn’t be too large, as this can draw in too much of the areola, which can be uncomfortable and may reduce milk flow.
A proper fit should allow for complete milk drainage without any areas of the breast feeling engorged or uncomfortable after pumping. If you experience nipple pain, redness, or blistering, or if your milk supply seems low, it’s essential to re-evaluate the flange size and consult with a lactation consultant for guidance.
Flanged Fitting Types and Functions
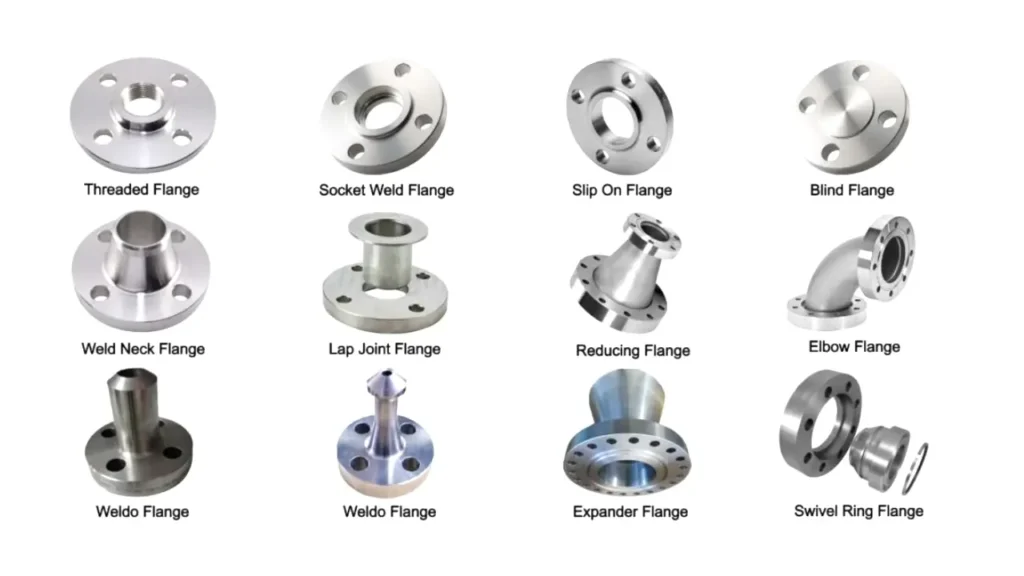
Certainly, let’s delve deeper into the types of flanged fittings:
1. Flanged Elbows
Function: As the name suggests, flanged elbows are used to introduce bends or changes in direction within a piping system. This is crucial for navigating obstacles, altering flow paths, and optimizing system layout.
Types:
45-degree elbows: These provide a gradual change in direction, often used when space constraints are less of an issue.
90-degree elbows: Offer a sharp change in direction, ideal for tight spaces or when a more abrupt turn is required.
Considerations:
- The elbow’s radius (measured from the center of the elbow) influences flow characteristics and pressure drop.
- Long-radius elbows generally minimize turbulence and pressure loss compared to short-radius elbows.
- Material selection (e.g., carbon steel, stainless steel) is critical based on the fluid being transported and the operating environment (temperature, pressure, corrosive conditions).
2. Flanged Tees
Function: Flanged tees serve as junctions in a piping system, allowing for:
- Branching: Introducing a new line or branch from the main pipeline.
- Splitting Flow: Dividing the flow of fluid into two or more directions.
- Combining Flow: Merging the flow from two or more branches into a single line.
Types:
- Straight Tees: All three openings have the same diameter.
- Reducing Tees: One opening has a smaller diameter than the other two.
Applications: Widely used in various industries, including:
- Oil and gas
- Chemical processing
- Water and wastewater treatment
- HVAC systems
3. Flanged Reducers
Function: These fittings are essential for connecting pipes with different diameters. They facilitate a smooth transition between sections of varying sizes.
Applications:
- Used in situations where the flow rate changes or where pipe sizes need to be adjusted to accommodate equipment or valves.
- Common in systems where fluid velocity needs to be controlled.
4. Flanged Crosses
Function: Flanged crosses provide a four-way connection point, allowing for:
- The intersection of four pipes.
- The introduction of a branch line at a 90-degree angle to the main line.
Applications:
Often used in complex piping networks where multiple lines need to converge. Found in applications such as:
- Fire sprinkler systems
- Gas distribution networks
- Industrial process plants
5. Flanged Adapters
Function: Adapters bridge the gap between different types of pipe connections. This flexibility is crucial when integrating components with varying end connections into a single system.
Common Types:
- Flanged to Threaded: Connects a flanged pipe to a threaded pipe or fitting.
- Flanged to Butt-Weld: Connects a flanged pipe to a pipe with a butt-welded end.
Applications:
Used extensively in piping systems where different types of valves, pumps, or instruments need to be integrated.
6. Flanged Valves
Function: Flanged valves provide control over the flow of fluid within a piping system.
Common Types:
- Gate Valves: Used for on/off service, allowing for complete shut-off of flow.
- Globe Valves: Used for throttling flow and regulating pressure.
- Check Valves: Prevent backflow of fluid in the system.
- Ball Valves: Provide quick on/off service and can be used for throttling in some cases.
- Butterfly Valves: Offer a compact design and are suitable for high-flow applications.
Advantages of Flanged Valves:
- Easy to install and maintain.
- Allow for easier inspection and repair compared to welded valves.
- Can be used in high-pressure and high-temperature applications.
7. Flanged Strainers and Filters
Function: These fittings are essential for protecting downstream equipment by removing particulate matter from the fluid flow.
Applications:
Used in various industries, including:
- Oil and gas production
- Chemical processing
- Water treatment
- Power generation
8. Flanged Expansion Joints
Function:
- Compensate for thermal expansion and contraction within the piping system.
- Absorb vibrations and movements caused by equipment operation or ground settling.
- Improve system flexibility and reduce stress on connected components.
Applications:
- Critical in applications where significant temperature fluctuations occur, such as:
- Steam lines
- Power plants
- HVAC systems
Fitting Type | Function | Key Characteristics | Applications |
---|---|---|---|
Flanged Elbows | Change direction of flow | 45°, 90° angles, various radii | General piping systems, HVAC |
Flanged Tees | Branching, splitting, combining flow | Straight tees, reducing tees | Oil & gas, chemical processing, water treatment |
Flanged Reducers | Connect pipes of different diameters | Smooth transition between sizes | Flow rate control, system adjustments |
Flanged Crosses | Four-way connection | Intersection of multiple lines | Fire sprinkler systems, gas distribution |
Flanged Adapters | Connect different pipe end connections | Flanged to threaded, flanged to butt-weld | Integrating components with varying connections |
Flanged Valves | Control fluid flow | Gate, globe, check, ball, butterfly valves | On/off service, throttling, pressure regulation |
Flanged Strainers/Filters | Remove particulate matter | Protect downstream equipment | Oil & gas, chemical processing, water treatment |
Flanged Expansion Joints | Absorb thermal expansion/contraction | Compensate for movement, reduce stress | Steam lines, power plants, HVAC |
How Do Flange Fittings Work
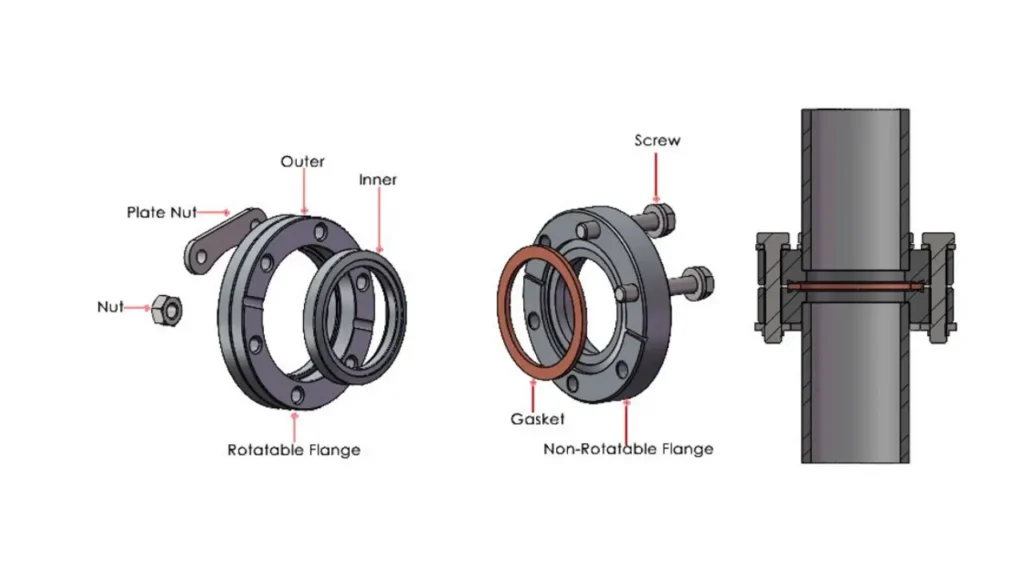
Flange fittings are essential components in piping systems. They essentially work by providing a secure and reliable connection point between different sections of pipe, valves, pumps, and other equipment.
Here’s how they function:
Joining Mechanism: Flanges are typically joined together using bolts and a gasket. The gasket, placed between the two flange faces, creates a seal to prevent leaks.
Bolting: Tightening the bolts applies compressive force to the gasket, ensuring a tight seal against the internal pressure within the piping system.
Versatility: Flange fittings offer a high degree of versatility. They can be easily disassembled for maintenance, inspection, or replacement of components.
Applications: Flange fittings are widely used in various industries, including:
- Oil and gas
- Chemical processing
- Water and wastewater treatment
- Power generation
- HVAC systems
In essence, flange fittings facilitate the construction of robust and reliable piping systems by providing a strong, leak-proof, and easily maintainable connection method.
Flange Facing Types
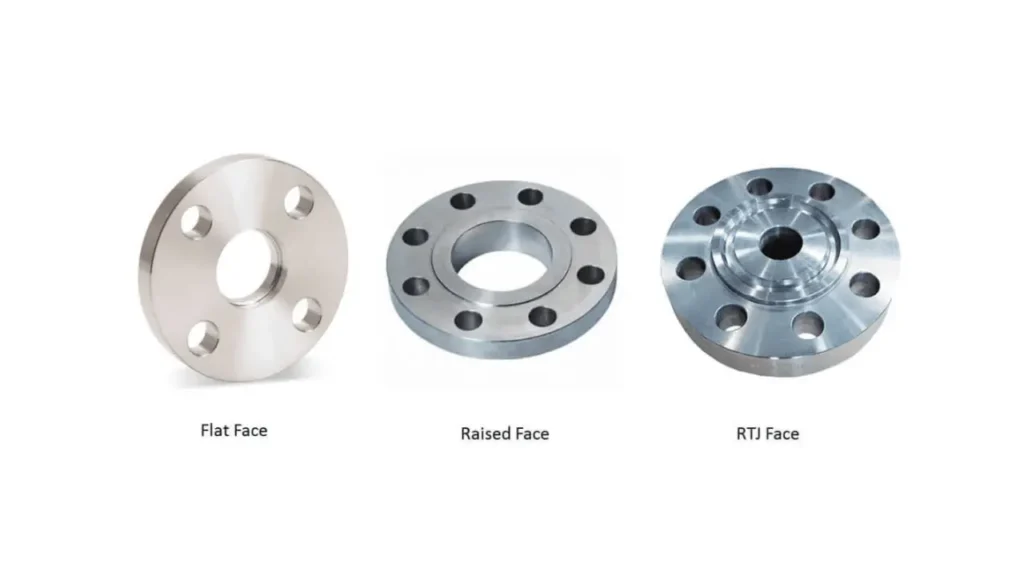
Flange facing types refer to the specific configuration of the surface where the flange contacts the gasket and the mating flange. The choice of facing type significantly impacts the seal integrity, gasket selection, and overall performance of the piping system.
Here are some common flange facing types:
1. Flat Face (FF)
- Description: The simplest type, with a flat, unmachined surface.
- Gasket: Typically uses full-face gaskets (e.g., spiral wound, rubber) to provide a complete seal.
- Advantages: Cost-effective, easy to machine.
- Disadvantages: Can be susceptible to gasket extrusion at high pressures.
2. Raised Face (RF)
- Description: Features a raised surface around the bolt circle, creating a narrower contact area for the gasket.
- Gasket: Uses ring-type gaskets (e.g., metal ring, spiral wound with metal inner ring) to concentrate the sealing force.
- Advantages: Better suited for high-pressure applications, reduces the risk of gasket extrusion.
- Disadvantages: Can be more expensive to manufacture.
3. Ring Joint (RTJ)
- Description: Employs a metal ring (typically oval-shaped) that fits into a groove on each flange face.
- Gasket: Uses the metal ring itself as the sealing element.
- Advantages: Excellent sealing performance at high pressures and temperatures, suitable for corrosive environments.
- Disadvantages: Requires precise machining and assembly, can be more expensive.
4. Tongue and Groove (T&G)
- Description: One flange has a tongue, and the other has a corresponding groove.
- Gasket: Typically uses a resilient gasket to fill the gap between the tongue and groove.
- Advantages: Provides a good seal, suitable for high-pressure applications.
- Disadvantages: Requires precise machining and alignment.
5. Male and Female (M&F)
- Description: One flange has a raised male surface, and the other has a recessed female surface.
- Gasket: Uses a resilient gasket to fill the gap between the male and female surfaces.
- Advantages: Provides a good seal, suitable for high-pressure applications.
- Disadvantages: Requires precise machining and alignment.
Factors influencing flange face selection:
- Operating pressure and temperature
- Fluid properties (corrosivity, viscosity)
- Gasket material compatibility
- Cost considerations
- Maintenance requirements
Flange Fitting Dimensions
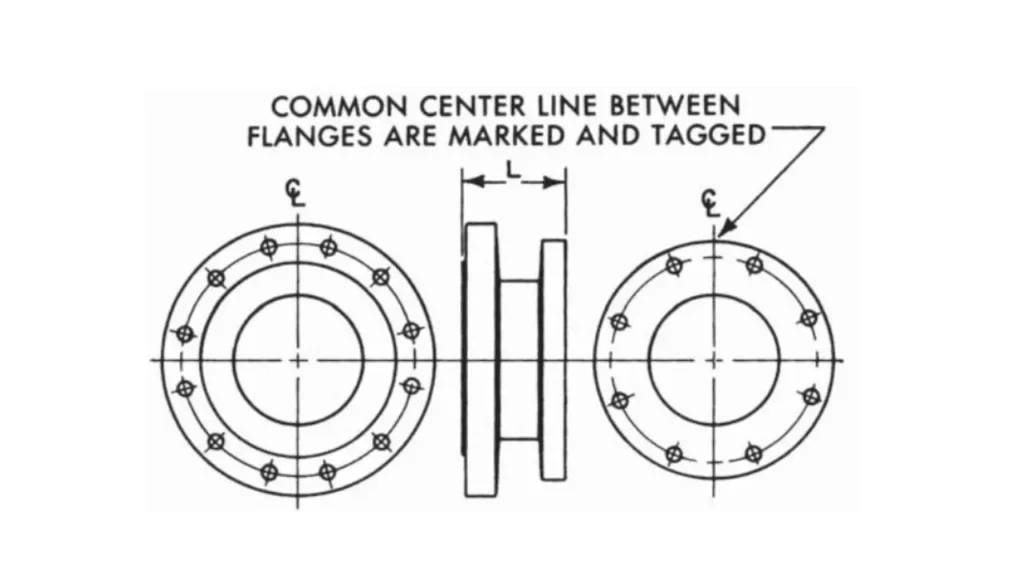
Flange fitting dimensions are crucial for proper installation and compatibility within a piping system. These dimensions vary depending on several factors, including:
- Nominal Pipe Size (NPS): This refers to the standard pipe size designation, not the actual inside diameter.
- Flange Standard: Different standards (e.g., ANSI, ASME, DIN) have specific dimensional requirements.
- Pressure Class: Higher pressure classes require thicker flanges and larger bolt circles to withstand greater internal forces.
- Flange Facing Type: As discussed earlier, different facing types have unique dimensional characteristics.
Key Dimensions of a Flange:
- Outside Diameter (OD): The overall diameter of the flange.
- Bolt Circle Diameter (BCD): The diameter of the circle passing through the centers of the bolt holes.
- Bolt Hole Diameter: The diameter of the holes for the bolts.
- Flange Thickness: The thickness of the flange material.
- Number of Bolt Holes: Varies depending on the flange size and pressure class.
Where to Find Flange Dimensions:
- Flange Standards: Refer to the relevant standard documents (e.g., ANSI B16.5, ASME B16.47) for detailed dimensional specifications.
- Manufacturer‘s Catalogs: Manufacturers of flanges and fittings provide detailed dimensional drawings and specifications in their catalogs.
- Engineering Handbooks: Engineering handbooks and reference materials often contain tables and charts with flange dimensions.
Importance of Accurate Dimensions:
- Proper Alignment: Accurate dimensions ensure proper alignment of flanges during installation, minimizing stress and potential leaks.
- Bolt Selection: Correct bolt size and length are crucial for proper tightening and maintaining seal integrity.
- Gasket Selection: Gasket dimensions must be compatible with the flange face dimensions.
- System Integrity: Inaccurate dimensions can lead to leaks, structural failures, and potential safety hazards.
Always refer to the specific standards and manufacturer‘s documentation for the most accurate and up-to-date dimensional information for the flanges you are using.
Flange Fitting Standards and Markings
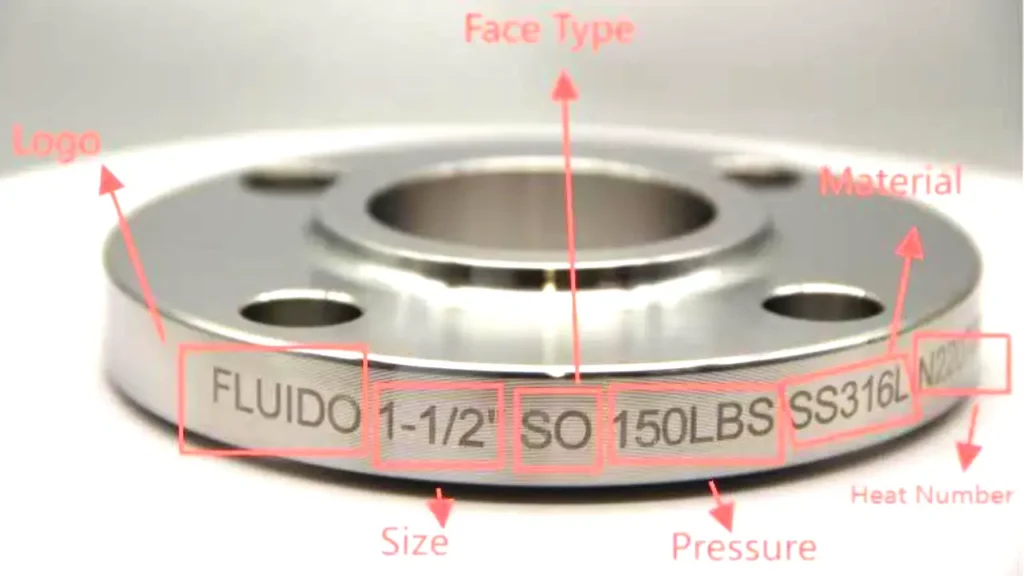
Flange fittings adhere to various international and national standards that ensure compatibility, safety, and quality. These standards outline dimensional specifications, pressure ratings, material requirements, and testing procedures.
Common Flange Fitting Standards:
- ANSI/ASME B16.5: A widely used standard in North America, covering steel pipe flanges and flanged fittings in various pressure classes.
- ISO: International Organization for Standardization, provides a set of international standards for flanges, including ISO 7005-1.
- DIN: German Institute for Standardization, offers specific standards for flanges and fittings used in Germany and other European countries.
- BS: British Standards, provides standards for flanges used in the United Kingdom.
- JIS: Japanese Industrial Standards, covers flanges and fittings manufactured in Japan.
Flange Fitting Markings
Flange markings are crucial for identifying key information about the fitting, ensuring proper selection and installation. Common markings include:
- Manufacturer‘s Name or Trademark: Identifies the manufacturer of the flange.
- Material Grade: Indicates the material used (e.g., ASTM A105, A350 LF2).
- Pressure Class: Indicates the maximum allowable pressure for the flange (e.g., Class 150, 300, 600).
- Size: Indicates the nominal pipe size (NPS) of the flange.
- Facing Type: Indicates the type of flange face (e.g., RF, RTJ, FF).
- Heat Number or Lot Number: Used for traceability and quality control purposes.
Marking | Description |
---|---|
ASME B16.5 | Conforms to the ASME B16.5 standard |
Class 150 | Pressure rating of the flange |
ASTM A105 | Material grade of the flange |
RF | Raised Face flange type |
12″ | Nominal pipe size (NPS) |
Heat No. 12345 | Heat number for traceability |
Manufacturer‘s Logo | Identifies the manufacturer |
Noted in the table:
- Specific marking requirements may vary depending on the applicable standard and the manufacturer‘s practices.
- Always refer to the relevant standards and manufacturer‘s documentation for complete and accurate marking information.
By understanding flange standards and markings, engineers and technicians can ensure the selection and installation of appropriate flanges for any given application, ensuring system safety and reliability.
Flange Fitting Classification & Service Ratings
Flange Fitting Classification
Flanges are classified based on several factors, including:
Material:
- Carbon Steel: Common and cost-effective, suitable for various applications.
- Stainless Steel: Resistant to corrosion, ideal for harsh environments and high-purity fluids.
- Alloy Steel: Offers high strength and resistance to extreme temperatures and pressures.
- Cast Iron: Used in lower-pressure applications.
- Ductile Iron: Offers improved strength and ductility compared to cast iron.
Type:
- Slip-on: Simple and economical, suitable for lower pressures.
- Weld Neck: Provides a strong, leak-tight joint, ideal for high-pressure applications.
- Threaded: Easy to assemble and disassemble, but limited in pressure and temperature range.
- Blind: Used to isolate sections of the pipeline.
- Lap Joint: Used with loose flanges and studs.
- Facing Type: As discussed earlier, different facing types (flat face, raised face, ring joint, etc.) have distinct characteristics that influence sealing performance and gasket selection.
Flange Fitting Service Ratings
Flange service ratings define the maximum allowable pressure and temperature that a flange can withstand under specific operating conditions. These ratings are crucial for ensuring the safety and integrity of the piping system.
Pressure Class:
- Designated by numbers (e.g., Class 150, 300, 600, 900, 1500, 2500).
- Higher class numbers indicate higher pressure ratings.
Temperature Rating:
- Flange ratings are typically specified for a range of temperatures.
- The allowable pressure decreases as the temperature increases.
Key Standards
- ANSI/ASME B16.5: Covers pipe flanges and flanged fittings in steel, stainless steel, and alloy steel.
- ANSI/ASME B16.47: Covers ductile iron pipe flanges.
- ANSI/ASME B16.1: Covers cast iron pipe flanges.
Selecting the Right Flange
When selecting flanges for a particular application, it’s crucial to consider:
- Operating pressure and temperature
- Fluid properties (corrosivity, viscosity)
- Piping material
- Application requirements (e.g., vibration, shock loads)
- Maintenance and inspection considerations
By carefully selecting flanges with appropriate classifications and service ratings, engineers can ensure the safe and reliable operation of piping systems in various industries.
Machining Process of Flange Parts
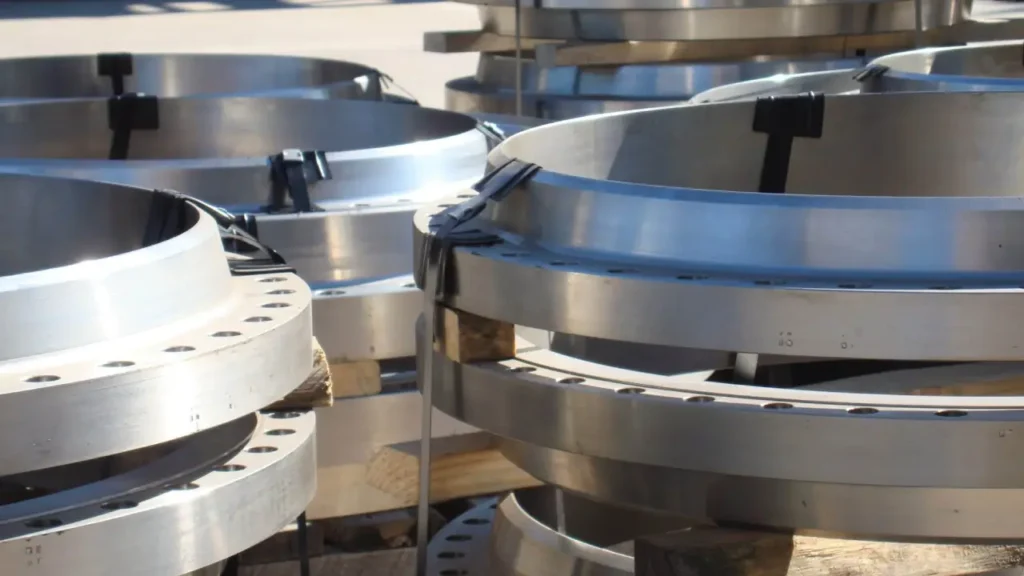
Here’s the machining process of flange parts step by step in the following:
Step 1: Material Selection
This is the foundational step.
The choice of material is crucial, as it directly impacts the flange’s performance in the intended application.
Common choices include carbon steel, alloy steel, and stainless steel.
Factors such as temperature, pressure, and the presence of corrosive substances significantly influence the material selection.
Step 2: Material Cutting and Shaping
Large metal plates or billets are cut into smaller pieces according to the required flange dimensions.
This may involve processes like sawing, shearing, or plasma cutting.
The cut pieces are then often heated to a suitable temperature to facilitate subsequent shaping processes.
Step 3: Heat Treatment
Depending on the specific material and the desired properties, the flanges may undergo various heat treatment processes:
- Annealing: To relieve internal stresses and improve machinability.
- Quenching and Tempering: To enhance strength, hardness, and toughness.
- Heat treatment significantly improves the mechanical properties of the flange, making it more resistant to wear, tear, and corrosion.
Step 4: Forming and Forging
This stage involves shaping the material into the desired flange profile.
Common methods include:
- Hot Forging: The metal is heated to a high temperature and then shaped under pressure. This allows for greater flexibility in forming complex shapes.
- Cold Forging: The metal is shaped at room temperature, which can result in higher strength and improved surface finish.
Step 5: Machining
This is a critical step where the flange is precisely machined to achieve the desired dimensions, tolerances, and surface finishes.
Common machining operations include:
- Facing: Creating flat and smooth surfaces for sealing.
- Chamfering: Creating beveled edges to facilitate assembly.
- Drilling: Creating holes for bolt connections.
CNC machines are often employed for automated and precise machining, ensuring high accuracy and repeatability.
Step 6: Surface Finish
To improve the appearance, enhance corrosion resistance, and remove any surface imperfections, the flanges may undergo surface finishing operations such as:
- Grinding: To achieve a smooth and precise surface.
- Polishing: To obtain a highly polished and reflective surface.
Step 7: Inspection and Quality Control
This is a crucial final step to ensure the quality and reliability of the finished flanges.
Rigorous inspection procedures are conducted, including:
- Dimensional inspection: To verify that the flange dimensions meet the specified tolerances.
- Visual inspection: To check for any surface defects or imperfections.
- Non-destructive testing: Techniques such as ultrasonic testing and magnetic particle inspection may be used to detect internal flaws.
This ensures that the flanges meet the required standards and are suitable for their intended applications.
This multi-step process ensures the production of high-quality flanges that meet the demanding requirements of various industries.
Conclusion
Flange fittings are essential components in various industries, providing secure and reliable connections for piping systems. Understanding their types, applications, and installation procedures is crucial for ensuring system integrity and preventing leaks. By carefully selecting the appropriate flange fitting for your specific needs, you can optimize system performance and minimize maintenance requirements.
Ready to enhance your hydraulic systems with high-quality flange fittings? Contact us today to explore our extensive inventory of wholesale hydraulic fittings. Our team of experts can assist you in selecting the ideal solutions for your unique project requirements. Experience the difference that premium-quality fittings can make in system efficiency and longevity.