Accurate measurement is crucial when working with pneumatic fittings to ensure proper connections and prevent leaks. This blog post aims to demystify the process of measuring these essential components, providing clear guidelines for identifying sizes and thread types. We’ll explore the tools and techniques needed to measure various types of pneumatic fittings.
Understanding the nuances of thread sizes, diameters, and fitting types is essential for selecting the correct components for your pneumatic system. This guide will cover the common measurements and thread standards, empowering you to confidently choose and install the right fittings.
What Are Pneumatic Fittings?
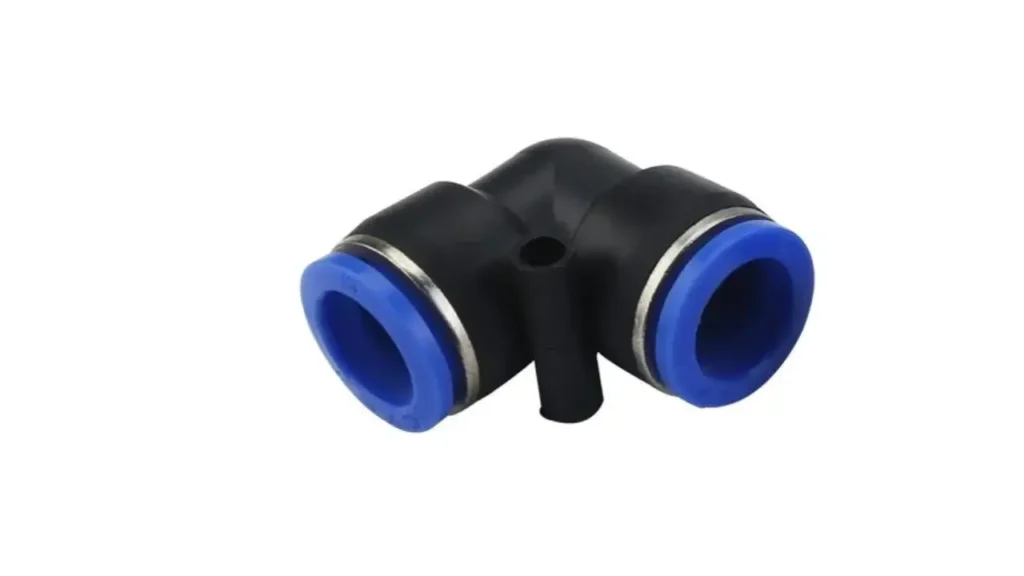
Pneumatic fittings are components designed to connect sections of tubing, hoses, or pipes in systems that utilize compressed air or gases. They provide secure, leak-free connections between various parts of a pneumatic system, such as valves, cylinders, and tools. These fittings come in a variety of shapes, sizes, and materials, like brass, stainless steel, and plastics, to accommodate different pressure ratings and application requirements.
How to Measure Pneumatic Fittings?

Accurately measuring pneumatic fittings is key to avoiding leaks and ensuring your system works smoothly. We’ll walk you through the process step-by-step, making it easy to understand.
Tools Needed
Before we begin measuring, let’s gather the necessary tools. Having the right tools makes the process smoother and more accurate.
- Caliper: A digital or vernier caliper is essential for precise measurements of diameters, lengths, and depths.
- Thread Gauge: For threaded fittings, a thread gauge is crucial for determining thread size and pitch accurately.
- Measuring Tape or Ruler: For general length measurements and quick estimations.
- Thread Size Chart: A thread size chart is invaluable when using a caliper for thread measurement, as it helps identify nominal thread sizes.
- Lighting: Good lighting is essential for clear visibility, especially when measuring small or intricate fittings.
Step 1: Identifying the Fitting Type
First, we need to figure out what type of fitting we’re dealing with. Common pneumatic fitting types include threaded, push-to-connect, and barbed fittings. Threaded fittings have screw threads, push-to-connect fittings allow for quick tubing insertion, and barbed fittings have ridges to grip hoses. Visually inspecting the fitting and comparing it to diagrams will help us identify it correctly.
Knowing the fitting type is crucial because it tells us where and how to measure. For example, we’ll measure thread size and pitch for threaded fittings, but tubing outer diameter for push-to-connect fittings. Getting this right prevents mismatched components and system failures.
Step 2: Measuring Threaded Fittings
For threaded fittings, we’ll use a thread gauge to determine the thread size and pitch. A thread gauge has blades with different thread pitches. We match the blades against the fitting’s threads until we find a perfect fit. Thread size is usually in inches (like 1/4″ or 1/2″) or metric units (like M10 or M12). The pitch, the distance between threads, is measured in threads per inch (TPI) for imperial or millimeters for metric.
If we don’t have a thread gauge, we can use a caliper to measure the outside diameter of the threads. Then, we compare this measurement to a thread size chart. We can also use the caliper to measure the distance between threads for the pitch. Keep in mind this method is less accurate, so a good thread chart is essential.
Step 3: Measuring Push-to-Connect Fittings
To measure push-to-connect fittings, we’ll focus on the tubing’s outer diameter (OD). We use a caliper to measure the OD of the tubing that will go into the fitting. This ensures a proper seal. We also measure the fitting’s bore, the internal diameter where the tubing goes.
If the fitting has a threaded connection, we’ll measure the thread size and pitch using a thread gauge or caliper. We need to ensure the tubing and fitting dimensions match the manufacturer’s specs. Mismatched sizes lead to leaks or connection failures.
Step 4: Measuring Barbed Fittings
For barbed fittings, we’ll determine the inner diameter (ID) of the hose or tubing we’ll use. We measure the hose ID with a caliper. We also measure the outer diameter of the barbs on the fitting. The barbs must be slightly larger than the hose ID for a secure grip.
We should also note the length and number of barbs. Longer and more barbs provide a more secure connection. When matching barbs to tubing, always check the manufacturer’s documentation for compatibility, as material tolerances differ.
How to Choose the Best Pneumatic Fittings?
Selecting the right pneumatic fittings is crucial for ensuring the efficiency and reliability of your compressed air system. With a wide array of options available, it’s essential to consider several key factors to make an informed decision.
Here’s what you should keep in mind:
Material Compatibility:
- Consider the environment and the type of gas or air being used.
- Choose materials like brass, stainless steel, or appropriate plastics that resist corrosion and degradation.
Pressure and Temperature Ratings:
- Ensure the fittings can handle the maximum pressure and temperature of your system.
- Exceeding these ratings can lead to leaks or failures.
Connection Type and Size:
- Select the appropriate connection type (threaded, push-to-connect, barbed) for your application.
- Match the fitting size to the tubing or hose diameter for a secure fit.
Application-Specific Requirements:
- Consider if the application needs any specific certifications, such as food grade or potable water certifications.
- Consider any vibration, or other environmental factors that may impact the fitting.
By carefully evaluating these aspects, you can choose pneumatic fittings that provide optimal performance and longevity, minimizing downtime and maintenance costs.
Conclusion
Accurate measurement of pneumatic fittings is vital for system integrity. Understanding thread types, sizes, and connection styles ensures compatibility and prevents leaks. Whether using calipers for precise dimensions or referencing manufacturer charts, precision is key. This knowledge empowers you to select the correct fittings, optimizing system performance and safety.
By mastering the measurement techniques outlined, you can confidently navigate pneumatic system maintenance and upgrades. This skill reduces downtime and ensures efficient operations. Remember, proper fitting selection is the cornerstone of reliable pneumatic systems.
For high-quality pneumatic fittings at wholesale prices, contact DF Hydraulics. We offer a wide range of fittings to meet your specific needs. Visit our website or contact our sales team today to learn more and place your order.