Flared and flareless fittings are two common methods for connecting tubing in various systems, each with distinct advantages and disadvantages. Flared fittings utilize a conical flare on the end of the tubing that creates a seal when inserted into a mating fitting.
This method is known for its strength and reliability, making it suitable for high-pressure applications. In contrast, flareless fittings, also known as compression fittings, use a compression ring (ferrule) to create a seal around the tubing. This design eliminates the need for flaring, simplifying installation and making them suitable for a wider range of applications.
This blog post will delve deeper into the key differences between flared and flareless fittings, exploring their respective strengths and weaknesses to help you make informed decisions for your specific project needs.
What Are Flared Fittings

Flare fittings are a type of mechanical connector used to join metal tubing in various applications, such as automotive, hydraulic, and refrigeration systems. They are characterized by a unique sealing mechanism: the end of the tubing is “flared,” or expanded and deformed, into a conical shape. This flared end is then inserted into a matching tapered fitting and secured with a nut, creating a tight and leak-proof seal.
Flare fittings offer several advantages, including their ability to withstand high pressures and vibrations, making them suitable for demanding applications. They are also relatively easy to assemble and disassemble, which is beneficial for maintenance and repairs. However, it’s crucial to properly flare the tubing and ensure correct installation to achieve a reliable and leak-free connection.
What Are Flareless Fittings
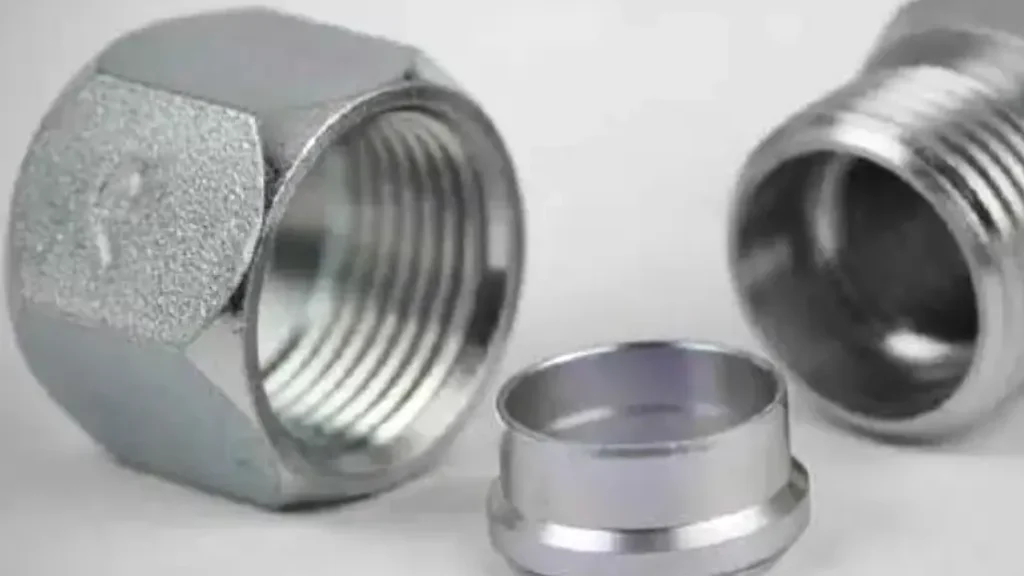
Flareless fittings, also known as compression fittings, are another type of connector used to join metal tubing in fluid systems. Unlike flared fittings, they do not rely on a flared end on the tubing for sealing. Instead, they utilize a compression ring (ferrule) that deforms the tubing slightly when tightened, creating a leak-proof seal between the tubing and the fitting.
Flareless fittings offer several advantages, including easier and quicker installation compared to flared fittings, as they do not require specialized flaring tools. This makes them a more convenient option for many applications. However, they may have limitations in extremely high-pressure applications or those with significant vibration, where flared fittings might offer superior performance.
Flared vs Flareless Fittings
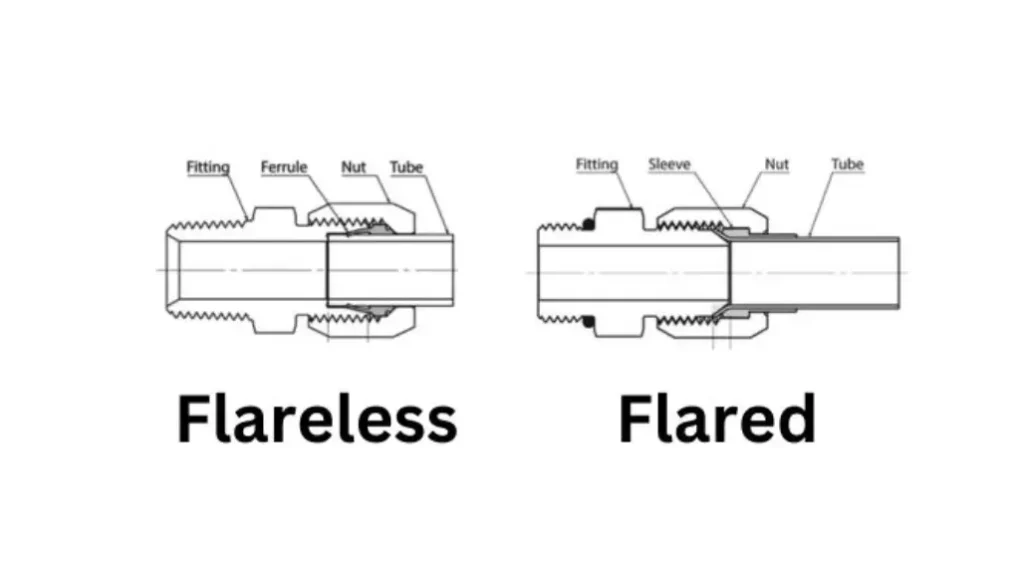
Flared and flareless fittings are both crucial components in fluid systems, each with distinct advantages and disadvantages.
Flared Fittings
Flared fittings utilize a unique sealing mechanism where the end of the tubing is carefully shaped into a specific angle, typically 37 degrees for common standards like AN (Army-Navy) and JIC (Joint Industry Conference). This flared end is then inserted into the fitting body, creating a tight seal through metal-to-metal contact.
Strengths:
- Exceptional Pressure Handling: Flared fittings excel in high-pressure applications due to the robust nature of the metal-to-metal seal. They can withstand significant pressure fluctuations without compromising integrity.
- Vibration Resistance: The strong mechanical connection provided by the flared joint offers excellent resistance to vibration and shock, crucial in applications where these factors are prevalent, such as in automotive and aerospace industries.
- Proven Reliability: Flared fittings have a long history of reliable performance in demanding environments and are widely recognized for their durability and longevity.
Weaknesses:
- Installation Complexity: Preparing the tubing for flaring requires specialized tools and precise techniques. This adds complexity to the installation process and may require skilled technicians.
- Potential for Leaks: Improper flaring techniques or damage to the flared end can lead to leaks, compromising system integrity and potentially causing safety hazards.
Flareless Fittings (Compression Fittings)
Flareless fittings, also known as compression fittings, employ a different approach to sealing. They utilize a compression ring (ferrule) that deforms the tubing slightly when tightened, creating a leak-tight seal between the tubing and the fitting body.
Strengths:
- Ease of Installation: Flareless fittings eliminate the need for specialized flaring tools, making them significantly easier and faster to install. This simplifies installation, reduces labor costs, and can be advantageous in field applications.
- Versatility: They are compatible with a wide range of tubing materials and sizes, offering flexibility in system design.
- Cost-Effectiveness: In many cases, flareless fittings can be more cost-effective than flared fittings due to the simplified installation process and potentially lower material costs.
Weaknesses:
- Pressure Limitations: While capable of handling moderate pressures, they may not be suitable for extremely high-pressure applications where flared fittings are typically preferred.
- Vibration Sensitivity: In applications with high levels of vibration, the seal created by the compression ring may be less robust compared to the metal-to-metal contact of a flared fitting.
Here’s the table showing the key differences between flared and flareless fittings:
Feature | Flared Fittings | Flareless Fittings |
---|---|---|
Sealing Mechanism | Flared tubing end | Compression ring (ferrule) |
Installation | Requires flaring tools | Easier to install, no flaring required |
Pressure Capability | Generally higher pressure capability | May have limitations in very high-pressure applications |
Vibration Resistance | Generally higher vibration resistance | May have limitations in high-vibration environments |
Ease of Installation | More complex installation | Easier and quicker installation |
By carefully evaluating these factors, engineers and technicians can select the most suitable fitting type for each specific application, ensuring system reliability, safety, and optimal performance.
Flared vs Flareless, Which Fitting Is Right for You
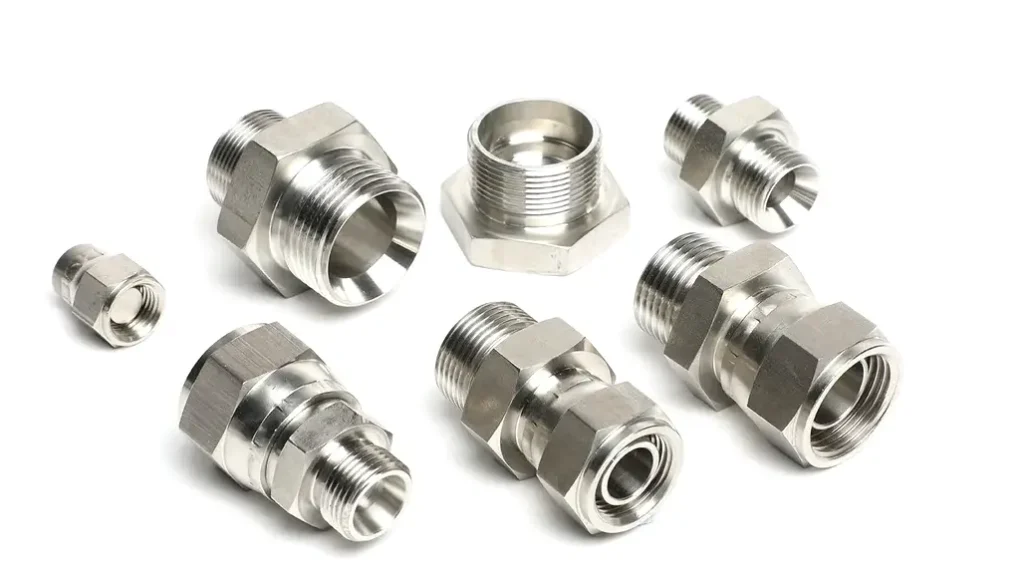
Choosing the Right Fitting: Flared vs. Flareless
Selecting the appropriate fitting type is crucial for the success of any fluid system. Here’s a breakdown to help you decide:
Choose Flared Fittings When:
- High Pressure is a Concern: Flared fittings excel in high-pressure applications, such as those found in aerospace, racing, and heavy-duty machinery.
- Vibration Resistance is Critical: The robust metal-to-metal seal of flared fittings provides superior resistance to vibration and shock, making them ideal for applications where these factors are prevalent.
- Durability is Paramount: Flared fittings are known for their long-lasting durability and can withstand demanding environments.
Choose Flareless Fittings When:
- Ease of Installation is Key: Flareless fittings are significantly easier and faster to install, eliminating the need for specialized flaring tools. This simplifies installation and reduces labor costs.
- Cost-Effectiveness is a Priority: In many cases, flareless fittings can be more cost-effective due to the simplified installation process and potentially lower material costs.
- Moderate Pressure Applications: They are suitable for a wide range of applications, including automotive, industrial, and general plumbing, where the pressure requirements are moderate.
Consider These Factors:
- Application: The specific application (e.g., automotive, aerospace, hydraulics) and its associated pressure, temperature, and vibration requirements.
- System Design: Factors like space constraints, accessibility for maintenance, and ease of installation.
- Budgetary Considerations: The overall cost of the fittings, including installation costs, maintenance requirements, and potential for long-term durability.
By carefully evaluating these factors, you can select the most suitable fitting type for your specific needs, ensuring system reliability, safety, and optimal performance.
AN vs MS Fittings
Understanding the distinctions between AN and MS fittings is crucial for selecting the right components for your hydraulic systems.
Here’s a detailed comparison between AN fittings and MS fittings.:
AN Fittings: Precision and Performance

Military-Grade Standards:
- AN (Army-Navy) fittings are manufactured to strict military specifications, ensuring consistent quality and performance. This standardization guarantees interchangeability and reliability in critical applications.
High-Pressure Capabilities:
AN fittings are designed to withstand high pressures and extreme temperatures, making them ideal for demanding applications like aerospace, motorsports, and heavy-duty hydraulics. Their 37-degree flared connection provides a robust, leak-free seal.
Material and Construction:
Typically made from high-grade materials like aluminum or stainless steel, AN fittings offer excellent corrosion resistance and durability. Their precise construction and tight tolerances contribute to their superior performance.
MS Fittings: Versatility and Economy
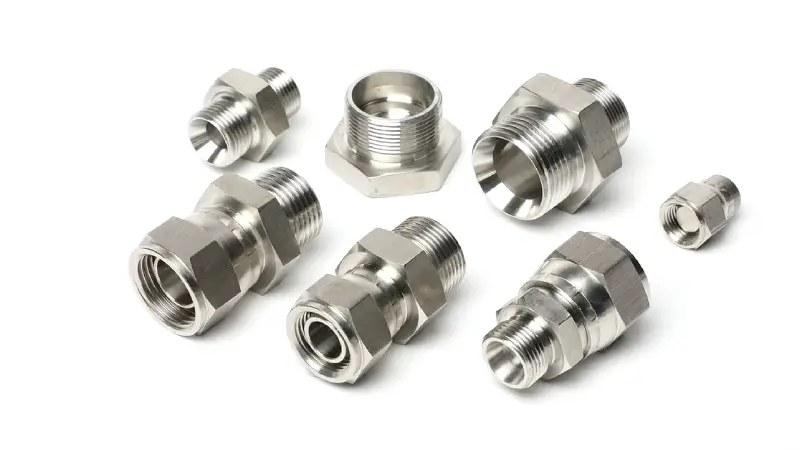
Military Standard, Broader Application:
MS (Military Standard) fittings encompass a wider range of specifications and applications compared to AN fittings. While they adhere to military standards, they are often used in general-purpose hydraulic systems.
Varied Designs and Connections:
MS fittings can include various connection types, such as threaded, flared, and compression fittings. This versatility makes them suitable for diverse applications.
Cost-Effectiveness:
MS fittings generally offer a more economical solution compared to AN fittings, making them a practical choice for applications where high-pressure capabilities are not the primary concern. They are often used in commercial and industrial hydraulic systems.
Here are the differences between AN and MS fittings in the following:
Feature | AN Fittings | MS Fittings |
---|---|---|
Standards | Strict military specifications | Broader military standards, wider application |
Pressure Rating | High | Variable, generally lower to medium |
Applications | Aerospace, motorsports, high-pressure hydraulics | General-purpose hydraulics, industrial applications |
Materials | High-grade aluminum, stainless steel | Various materials, including steel, brass, and aluminum |
Connection Type | 37-degree flared | Varied, including threaded, flared, and compression |
Cost | Higher | Lower |
When choosing between AN and MS fittings, consider the specific requirements of your hydraulic system. If high pressure and reliability are critical, AN fittings are the preferred choice. For general-purpose applications where cost is a factor, MS fittings offer a viable alternative.
Conclusion
Choosing between flared and flareless fittings depends on a variety of factors, including the specific application, pressure requirements, vibration levels, and ease of installation. Flared fittings offer superior performance in high-pressure and high-vibration environments, while flareless fittings provide a more convenient and cost-effective solution for many applications.
By carefully considering the advantages and limitations of each type, you can select the most appropriate fittings for your specific needs, ensuring optimal performance, safety, and reliability in your fluid system.
Ready to upgrade your hydraulic systems with high-quality fittings? Contact DF Hydraulics today to explore our extensive inventory of flared and flareless fittings. As a leading manufacturer and supplier, we offer a wide range of options to meet the diverse needs of your projects. Benefit from competitive wholesale pricing and expert support from our knowledgeable team.