When it comes to connecting pipes in plumbing systems, choosing the right method is crucial for ensuring a long-lasting and efficient installation. Two popular techniques for making these connections are compression fitting vs solder.
In this article, we will compare these two methods in-depth, examining their structures, working principles, advantages, disadvantages, and real-world applications. If you have any questions about the content, feel free to reach out to us.
Compression Fitting:
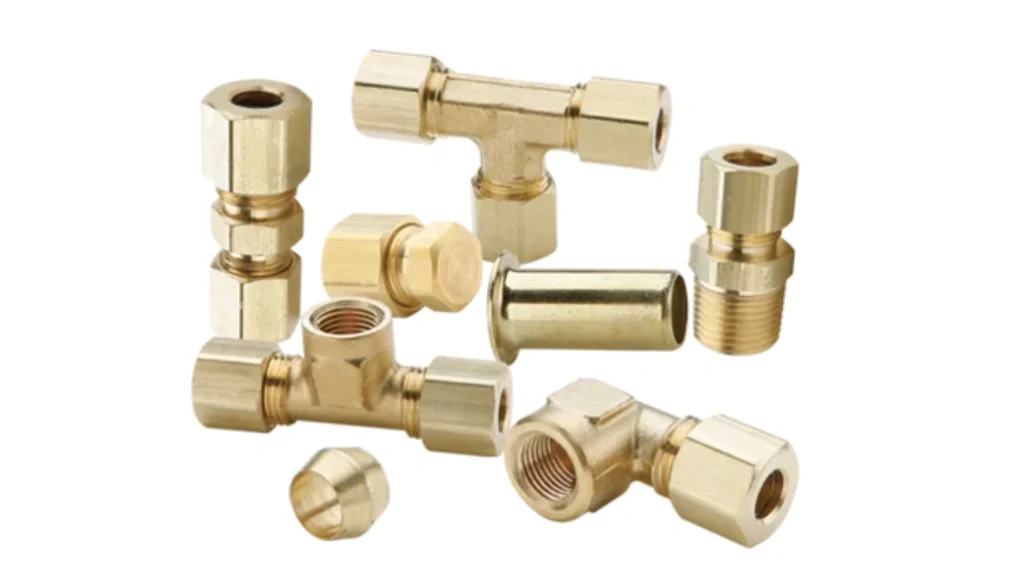
Structure and Working Principle:
A compression fitting is a mechanical device used to join two pipes together. It consists of several key components:
- Fitting Body: A hollow component that houses the pipe.
- Compression Nut: A threaded nut that tightens onto the fitting body.
- Compression Ring (or Olive): A small, usually brass ring that fits between the pipe and the fitting body to create a tight seal when compressed.
Working Principle:
The fitting works by tightening the compression nut, which forces the compression ring against the pipe and the fitting body, creating a watertight seal. The force of the nut tightening compresses the ring, ensuring a secure connection.
Common Sizes:
The most common sizes for compression fittings are:
Pipe Material | Common Sizes (inches) |
---|---|
Copper | 1/4, 3/8, 1/2, 3/4, 1 |
Plastic (PVC, CPVC) | 1/2, 3/4, 1, 1 1/4, 1 1/2 |
PEX | 1/2, 3/4, 1 |
How to Install Compression Fitting
Step 1: Prepare the Pipe
- First, measure and mark the pipe to the desired length. I usually use a measuring tape and a marker for this. Then, using a pipe cutter or a hacksaw, cut the pipe. If using a hacksaw, make sure to use a fine – tooth blade to get a clean cut.
- After cutting, use a deburring tool to remove any sharp edges or burrs from the cut end of the pipe. This is important as burrs can prevent the ferrule from making a proper seal.
Step 2: Assemble the Fitting
Slide the compression nut onto the pipe first. The nut should be oriented with the open end facing away from the cut end of the pipe.
Then, slide the ferrule onto the pipe. The ferrule should be placed with its tapered end facing the cut end of the pipe. I find it helpful to hold the pipe firmly while sliding these components on to ensure they are properly positioned.
Step 3: Insert the Pipe into the Fitting
Insert the prepared pipe into the fitting body until it reaches the bottom of the socket.
Make sure the pipe is fully inserted to ensure a proper fit.
Step 4: Tighten the Nut
Start by hand – tightening the compression nut as much as possible. This initial hand-tightening helps to align the components.
Then, use an adjustable wrench to give the nut an additional 1/4 to 1/2 turn. Be careful not to over- tighten, as this can damage the ferrule or the pipe. In my experience, over-tightening has led to leaks in some cases. After tightening, check the connection for any signs of looseness.
Applicable Scenarios of Compression Fitting
Residential Plumbing:
Compression fittings are commonly used in residential plumbing for connecting faucet supply lines, toilet water supply lines, and small-diameter pipes in the bathroom and kitchen. Their ease of installation makes them a popular choice for DIYers and professional plumbers alike.
For example, when I was renovating my own kitchen, I used compression fittings to connect the new faucet supply lines, and the process was quick and straightforward.
Small-scale Industrial Applications:
In small-scale industrial settings, such as workshops or light manufacturing facilities, compression fittings can be used for low-pressure air or water systems. They are suitable for applications where quick assembly and disassembly may be required, like in some portable equipment or temporary piping setups.
Advantages and Disadvantages of Compression Fitting
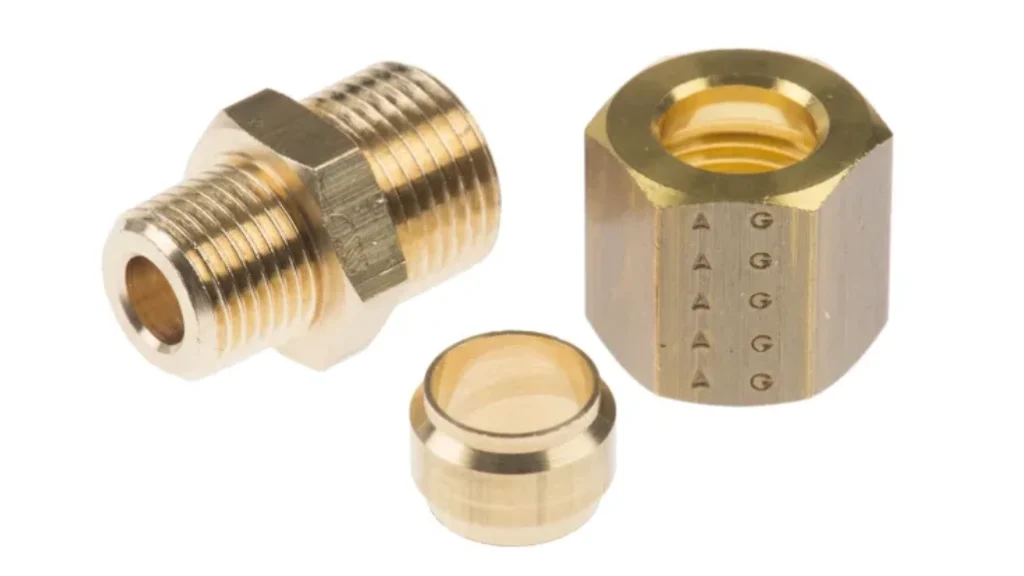
Advantages
- Ease of Installation: As mentioned earlier, compression fittings are relatively easy to install. They do not require specialized skills like soldering, which makes them accessible to a wider range of people. This also means that installation time can be significantly reduced, especially in projects with multiple connections.
- Reusability: In many cases, compression fittings can be reused. If the components are in good condition, they can be disassembled and reinstalled in another location. I’ve reused compression fittings in some of my plumbing projects where I needed to make adjustments or changes to the piping layout.
- Versatility: They can be used with a variety of pipe materials, including copper, plastic, and PEX. This versatility makes them a convenient option for different types of plumbing and piping systems.
Disadvantages
- Sealing Under Extreme Conditions: Compression fittings may not provide a reliable seal under extreme conditions such as high temperatures, high pressures, or in the presence of certain corrosive substances. For example, I’ve seen compression fittings fail in high-pressure steam systems due to the inability to maintain the required seal.
- Vibration Sensitivity: Over time, vibrations in the piping system can cause the compression nut to loosen, potentially leading to leaks. This is a common issue in industrial settings where machinery vibrations can affect the stability of the connections.
Solder
Structure and Working Principle of Solder:
Soldering is a method where two pipes are joined by melting a filler material (solder) between them. Unlike compression fittings, soldering requires the use of heat to bond the components together.
- Filler Material (Solder): Typically made of lead-free alloys such as tin and copper.
- Flux: A substance used to clean and prepare the metal surfaces for bonding.
Working Principle:
The pipe and fitting are heated with a torch until they reach a temperature where the solder melts and flows into the joint. Once the solder cools and hardens, it forms a strong, leak-proof connection.
How to Install Soldered Joints:
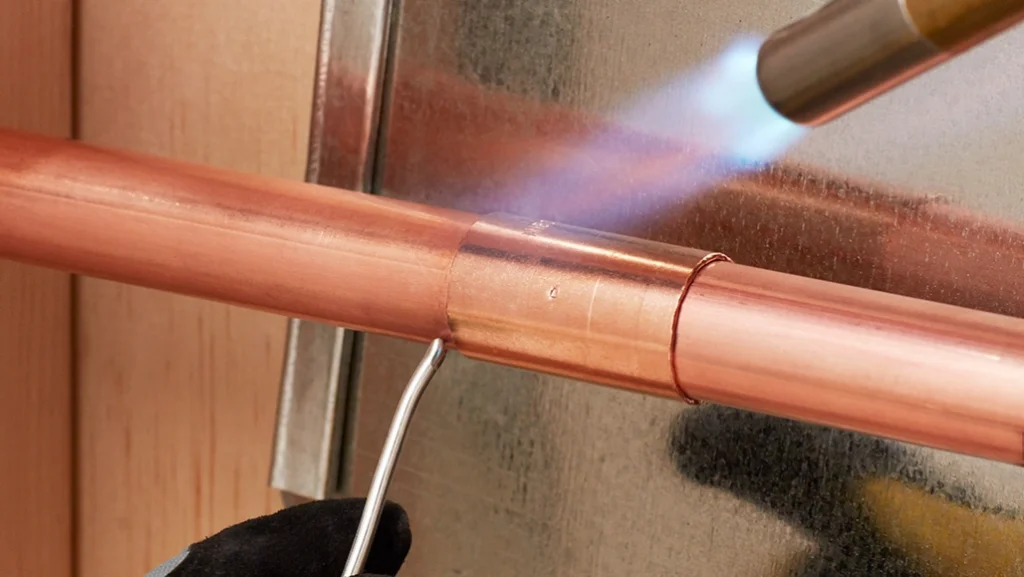
Step 1: Cut the pipes to the correct length and clean the ends thoroughly.
Step 2: Apply flux to the pipe ends and inside the fitting.
Step 3: Heat the joint with a torch until the metal is hot enough to melt the solder.
Step 4: Feed the solder into the joint, allowing it to flow into the gap between the pipe and fitting.
Step 5: Allow the joint to cool before testing for leaks.
Suitable Applications of Solder:
Soldering is commonly used in:
- Copper piping systems (water supply, HVAC)
- Refrigeration systems (for joining copper tubing)
- Electrical wiring (for certain connections)
Advantages and Disadvantages of Solder
Advantages:
- Provides a strong, permanent bond.
- Soldered joints are generally more durable over time.
- Works well for high-pressure applications.
Disadvantages:
- Requires a heat source, which can be dangerous if not handled properly.
- Time-consuming compared to compression fittings.
- Requires more skill and experience to ensure a good seal.
Comparison of Compression Fitting and Solder in Multiple Dimensions
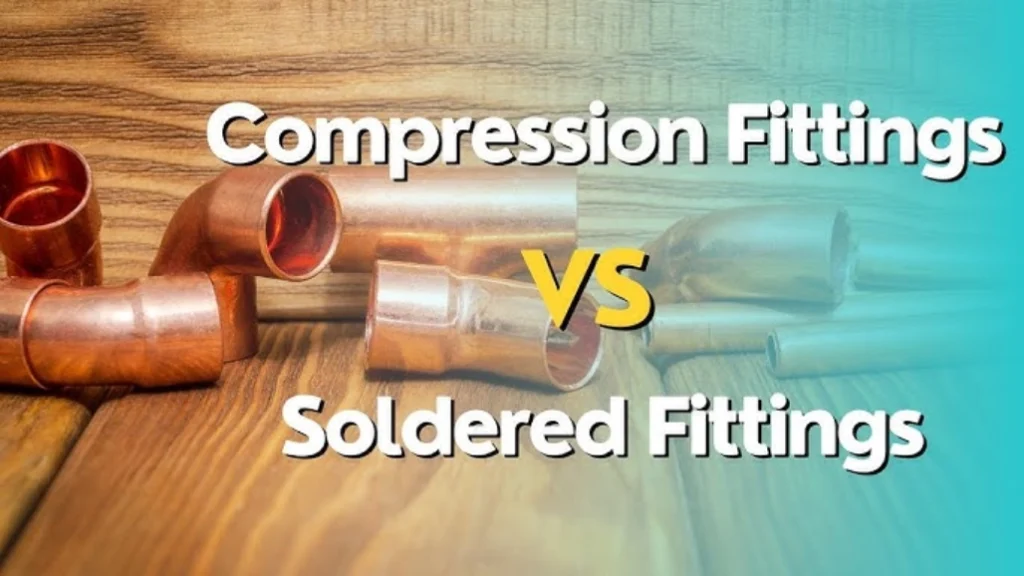
Sealing Performance
- Low-Pressure Systems: In low-pressure systems, both compression fittings and soldering can provide a reliable seal. However, compression fittings may be more convenient as they can be installed quickly. For example, in a residential water supply system with relatively low pressure, compression fittings have proven to be a cost-effective and efficient option.
- High-Pressure Systems: Soldering clearly has an advantage in high-pressure systems. The strong bond formed by soldering can withstand high pressures without leaking, while compression fittings may struggle to maintain the seal under extreme pressure. In an industrial high-pressure steam pipeline, soldering is the standard method for ensuring a leak-tight connection.
Installation Time
- Small-Scale Projects: For small-scale projects with only a few connections, compression fittings are much faster to install. The simple assembly process of compression fittings allows for quick completion of the job. When I was installing a new faucet in a bathroom, using compression fittings took me only a fraction of the time it would have taken to solder the connections.
- Large-Scale Projects: In large-scale projects, the time difference becomes more significant. While soldering may be more time-consuming for each individual joint, if the project requires a high-quality, long-lasting connection throughout the system, the extra time invested in soldering can be worth it. In a large commercial building’s plumbing installation, although soldering takes longer, it ensures the long-term reliability of the system.
Cost
- Material Cost: Compression fittings generally have a lower initial material cost, especially when considering the cost of the fitting components alone. However, when including the cost of tools for installation, the cost difference may be narrow. Soldering requires additional materials such as solder and flux, which can add to the overall cost.
- Labor Cost: Labor costs can vary depending on the skill level required. Compression fittings can be installed by less-skilled workers, resulting in lower labor costs. On the other hand, soldering requires a skilled plumber or welder, which may increase the labor cost. In a small DIY project, the cost of using compression fittings is often more appealing due to the lower labor requirements.
Durability
- Normal Conditions: Under normal operating conditions, both compression fittings and soldered joints can be durable. However, compression fittings may be more prone to loosening over time due to vibrations or thermal expansion and contraction. Soldered joints, once properly made, are more likely to maintain their integrity over the long term.
- Harsh Conditions: In harsh conditions, such as high-temperature, high-pressure, or corrosive environments, soldered joints are more durable. The strong bond and corrosion-resistant properties of soldered joints make them better suited for these challenging conditions.
Reusability
- Compression Fittings: As mentioned earlier, compression fittings can often be reused if the components are in good condition. This can be an advantage in situations where the piping system may need to be modified or relocated.
- Soldered Joints: Soldered joints are generally not reusable. Once the solder has cooled and solidified, disassembling the joint without damaging the pipe and fitting is difficult. In most cases, if a soldered joint needs to be removed, the pipe and fitting may need to be cut and new components installed.
Comparison Dimensions | Compression Fittings | Soldering |
Sealing Performance | Reliable in low-pressure systems; sealing performance may be poor in high-pressure systems | Obvious advantages in high-pressure systems, with excellent sealing performance |
Installation Time | Fast in both small – scale and large-scale projects, with simple assembly | Slow in both small – scale and large-scale projects, involving multiple steps such as preparation, heating, and cooling |
Cost | Low material cost and the difference narrows when tool costs are included; low labor cost | High material cost, requiring solder and flux; high labor cost |
Durability | Durable under normal conditions, but prone to loosening due to vibration, thermal expansion, and contraction; poor durability under harsh conditions | Durable under both normal and harsh conditions, capable of maintaining integrity over the long term |
Reusability | Reusable when components are in good condition | Generally not reusable, and disassembly is likely to damage pipes and fittings |
How to Choose Between Compression Fitting vs Soldering
When deciding between compression fittings and soldering, the decision largely depends on the following factors:
- Ease of Installation: If you need a quick, hassle-free connection, compression fittings are the better choice.
- Strength and Durability: For a long-lasting, strong joint, soldering is typically more reliable.
- Skill Level: If you lack experience with soldering, compression fittings are much easier to install.
- Type of Installation: For permanent installations, soldering is usually preferred. For repairs or temporary fixes, compression fittings are ideal.
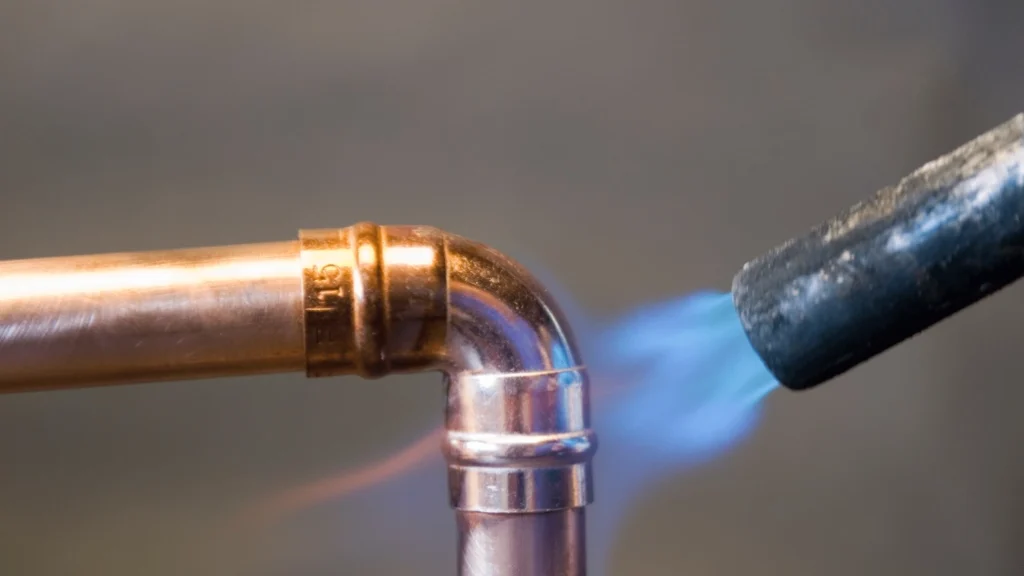
Compression Fittings vs Solder Joints
Compression fittings and soldered joints are both methods for connecting pipes, but they offer distinct advantages and disadvantages:
Compression Fittings
Pros:
- Easy Installation: Generally quicker and easier to install, requiring fewer specialized tools.
- Reusability: Can be easily disassembled and reassembled, allowing for adjustments or repairs.
- Versatility: Suitable for a wider range of materials, including plastic pipes.
Cons:
- Lower Pressure Capability: May not be as suitable for high-pressure applications as soldered joints.
- Potential for Leaks: The seal relies on a mechanical compression, which can loosen over time or with vibrations.
- Less Durable: May not be as durable as soldered joints in some applications.
Soldered Joints
Pros:
- High Pressure Capability: Well-suited for high-pressure applications.
- Strong and Durable: Create a strong, permanent, and leak-resistant connection.
- Suitable for High Temperatures: Can withstand higher temperatures than some compression fittings.
Cons:
- Difficult to Install: Requires specialized tools (soldering iron, flux, etc.) and more technical skill.
- Not Reusable: Once soldered, disassembly is difficult and may damage the pipe or fitting.
- Less Flexible: Less adaptable to changes or adjustments after installation.
Choosing the Right Method:
Compression fittings are often preferred for:
- Low-pressure applications: Such as household water supply lines, air lines, and some refrigeration systems.
- DIY projects: Due to their ease of installation.
- Situations where future adjustments or repairs may be necessary.
Soldered joints are typically used for:
- High-pressure applications: Such as industrial systems, some plumbing applications, and heating systems.
- Permanent installations: Where disassembly is not expected.
- Applications requiring maximum strength and durability.
Important Note: This information is for general guidance only. The best choice depends on the specific application, pressure requirements, materials used, and individual preferences. It’s always recommended to consult with a qualified plumber or engineer for specific projects and to ensure proper installation and safety.
Conclusion
Both compression fittings and soldering have their pros and cons, and the choice ultimately depends on your specific needs. Compression fittings offer convenience and speed, while soldering provides strength and durability for permanent installations.
If you need a reliable and quick connection, compression fittings might be the way to go. However, if you are looking for a long-lasting and robust solution, soldering could be your best option. If you’re still unsure or need more guidance, feel free to visit our homepage or contact us for a product catalog.
FAQs About Compression Fitting vs Solder
Do compression fittings last?
Yes, compression fittings can last for many years if installed properly and maintained. However, they may require periodic re-tightening, especially in high-pressure systems. Over-tightening or poor installation can cause leaks over time.
Do professional plumbers use compression fittings?
Yes, professional plumbers often use compression fittings in situations where quick installation is necessary or when heat is not an option. Compression fittings are commonly used in residential plumbing and repair jobs.
Are compression fittings better than soldering?
It depends on the application. Compression fittings are faster and easier to install, but soldering offers a stronger, more permanent bond. For high-pressure or permanent systems, soldering is typically better. For repairs and easy installations, compression fittings are preferred.
What are the disadvantages of compression fittings?
Compression fittings can sometimes loosen over time, requiring re-tightening. They may also not be as strong as soldered joints, especially in high-pressure systems. Additionally, over-tightening can cause damage to the pipe or fitting.
Barb vs Compression Fittings: What’s the Difference?
Barb fittings are typically used for flexible tubing and involve inserting the tubing over the barbed end. Compression fittings, on the other hand, use a compression ring and nut to secure the pipe. Barb fittings are less secure than compression fittings, making compression fittings better for permanent connections.
Where can I buy fittings?
You can find high-quality compression fittings and other plumbing supplies through Dingfeng. We offer a full range of fittings, from copper pipe compression fittings to specialty connectors. Contact us for custom orders or browse our extensive catalog for the best prices.
Can you solder a compression fitting?
No, you should not solder a compression fitting.
Compression fittings rely on a mechanical seal created by a compression nut and ferrule. Soldering would interfere with this mechanism, potentially damaging the fitting and compromising the seal.
Is Compression Fitting Better Than Solder?
Compression fittings and soldering are both methods for connecting pipes, but they offer distinct advantages and disadvantages. Compression fittings are generally easier to install, requiring no specialized tools or heat. They are also reusable, allowing for easier disassembly and reassembly. However, they may not be suitable for all applications, particularly those involving high pressures or extreme temperatures.
Soldering, on the other hand, creates a more permanent and robust connection. It is often preferred for high-pressure applications and in situations where a leak-proof seal is crucial. However, soldering requires specialized tools and skills, and it is not as easily reversible as a compression fitting. The best choice between the two methods depends on the specific requirements of the application.