Hydraulic systems, especially those operating under high pressure, demand precision and reliability. The choice of hydraulic hose end fittings is critical, impacting system performance and safety. This blog post delves into the various hydraulic hose end fitting types, focusing on their suitability for high-pressure applications.
We’ll explore the key factors to consider when selecting fittings, including material, thread type, and pressure ratings. Understanding these elements ensures you choose the right fittings, minimizing risks and maximizing efficiency in your high-pressure hydraulic systems.
What Are Hydraulic End Fittings
Hydraulic end fittings are essential components in hydraulic systems, serving as the connection points between hydraulic hoses, tubes, pipes, and other hydraulic components like pumps, valves, and cylinders. Their primary function is to create secure, leak-free connections that can withstand the high pressures and demanding conditions inherent in hydraulic applications. These fittings ensure the efficient transfer of hydraulic fluid, enabling the system to perform its intended tasks.
These fittings come in a wide variety of designs, materials, and sizes to accommodate different hydraulic system requirements. They are critical for maintaining system integrity and preventing fluid loss, which can lead to reduced performance, equipment damage, and safety hazards. The selection of appropriate hydraulic end fittings is crucial for ensuring the reliability and longevity of any hydraulic system.
Hydraulic Hose End Fitting Types
Recommended products
Types of hydraulic end fittings are the crucial components that ensure these connections are secure, leak-proof, and capable of withstanding extreme pressures. Understanding the diverse range of fittings available is essential for engineers, technicians, and anyone working with hydraulic equipment.
This guide delves into the six primary types of hydraulic end fittings, exploring their designs, applications, and benefits, to help you make informed choices for your hydraulic systems.
Crimp Hydraulic End Fittings
Design: Crimp Hydraulic End Fittings are a staple in hydraulic systems, providing a permanent and robust connection between a hose and a fitting. The design involves inserting the hose end onto the fitting’s barb and then compressing a metal sleeve (the ferrule or crimp sleeve) around the hose using a specialized crimping machine. This process creates a mechanical bond that is highly resistant to pressure and pull-out forces. The precision of the crimping process ensures a consistent and reliable connection, making it a preferred choice for high-pressure applications.
Application: These fittings find widespread use in various industries, including construction, agriculture, and manufacturing, where hydraulic systems operate under demanding conditions. They are commonly used in applications such as heavy machinery, hydraulic presses, and fluid transfer systems. The permanent nature of the crimped connection is particularly beneficial in situations where frequent disconnection is not required, and long-term reliability is paramount. The strength and durability of crimped fittings make them ideal for high-pressure environments, reducing the risk of leaks and failures.
Benefits: The benefits of Crimp Hydraulic End Fittings include their high-pressure rating, secure and permanent connection, and cost-effectiveness for mass production. They are relatively simple to install with the proper equipment, and the resulting connection is highly resistant to vibration and mechanical stress. The consistency of the crimped connection minimizes the risk of leaks, contributing to the overall efficiency and safety of the hydraulic system.
Hose Barb Hydraulic End Fittings

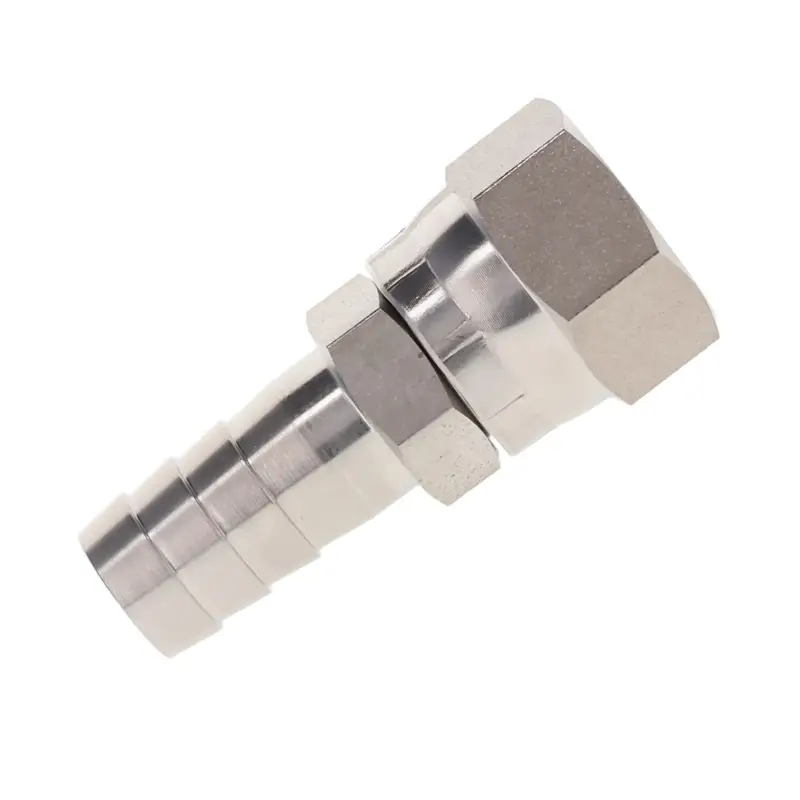
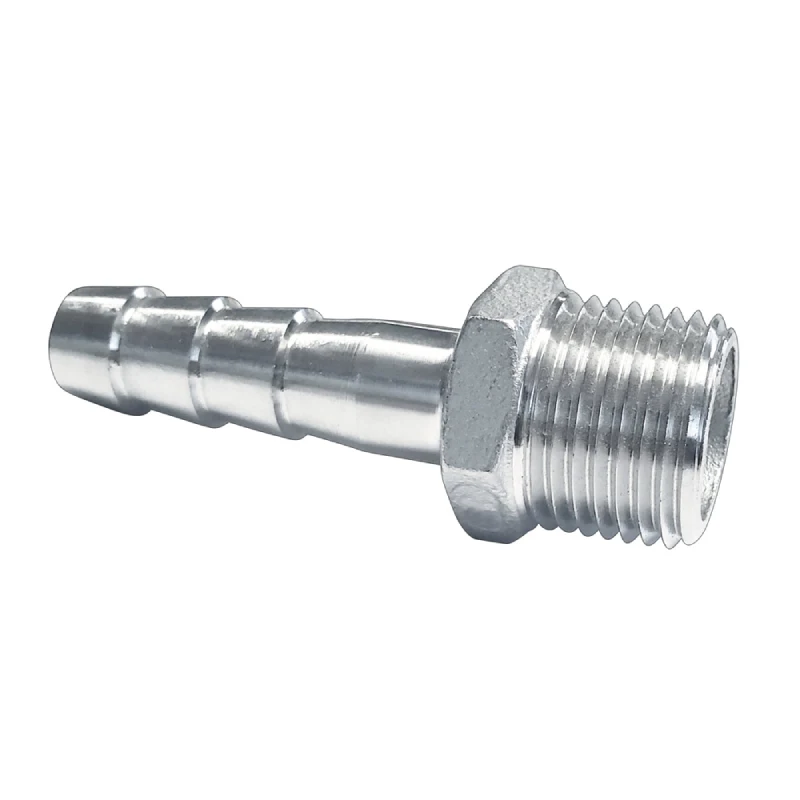
Design: Hose Barb Hydraulic End Fittings are designed for lower-pressure applications and are characterized by their barbed design, which provides a simple and effective method for securing a hose to a fitting. The barb consists of a series of ridges or serrations that grip the inner wall of the hose, preventing it from slipping off. These fittings are typically made from materials like brass, steel, or plastic, depending on the application and fluid compatibility.
Application: These fittings are commonly used in applications such as pneumatic systems, low-pressure fluid transfer, and general-purpose hose connections. They are particularly popular in situations where quick and easy assembly is required, and the operating pressures are relatively low. The simplicity of the design makes them ideal for DIY projects and applications where specialized tools are not readily available. Their ease of use makes them a favorite for many general purpose applications.
Benefits: The benefits of Hose Barb Hydraulic End Fittings include their ease of installation, low cost, and availability in a wide range of sizes and materials. They are suitable for applications where flexibility and quick assembly are important. However, they are not recommended for high-pressure or critical applications where a more robust connection is required.
Push-Lock Hydraulic End Fittings
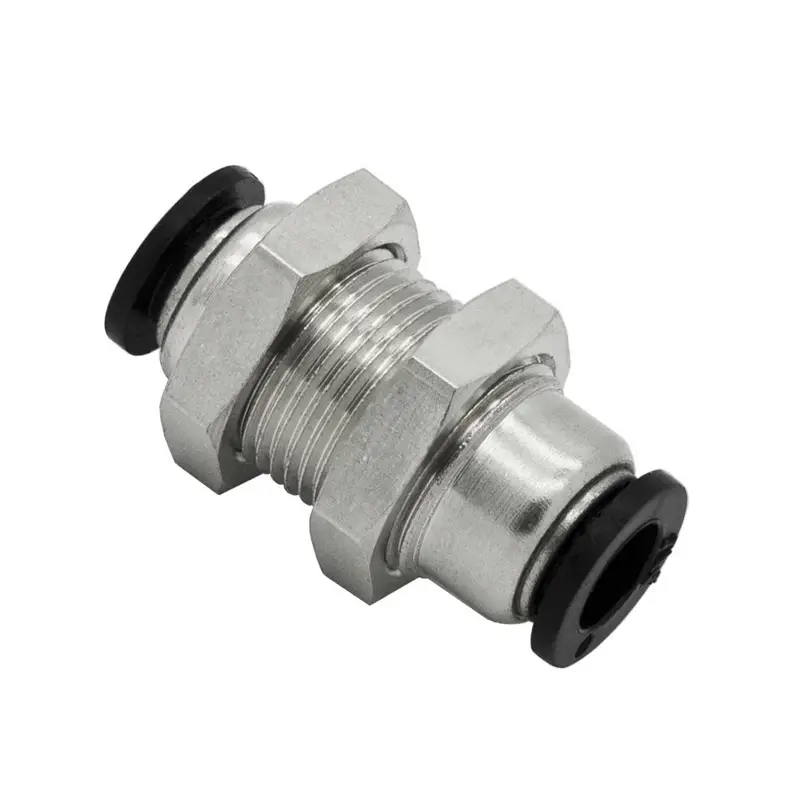


Design: Push-Lock Barb Hydraulic End Fittings offer a tool-free method for connecting hoses in low-pressure applications. They feature a barbed design similar to traditional hose barbs but incorporate a locking mechanism that secures the hose to the fitting. This design allows for quick and easy installation without the need for clamps or crimping tools. The locking mechanism ensures a secure connection, preventing the hose from slipping off under pressure.
Application: These fittings are commonly used in pneumatic systems, air tools, and low-pressure fluid transfer applications where speed and convenience are essential. They are particularly popular in environments where frequent hose changes or adjustments are required. The push-lock design simplifies maintenance and reduces downtime, making them ideal for applications where efficiency is critical.
Benefits: The benefits of Push-Lock Barb Hydraulic End Fittings include their tool-free installation, quick connection and disconnection, and ease of use. They are ideal for low-pressure applications where speed and convenience are paramount. However, they are not suitable for high-pressure or critical applications where a more robust connection is required.
Quick Connect Hydraulic End Fittings
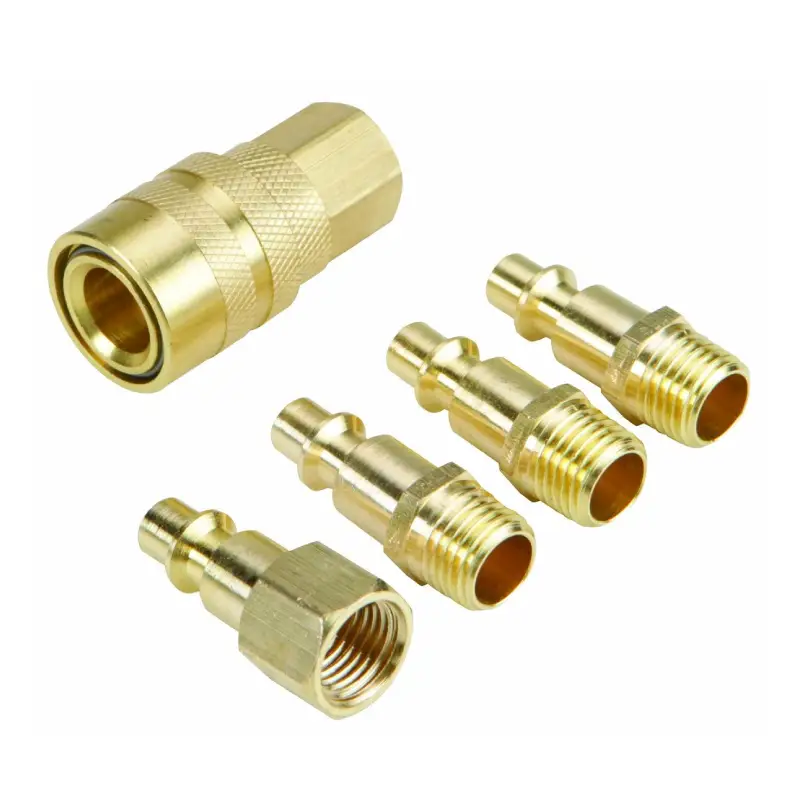
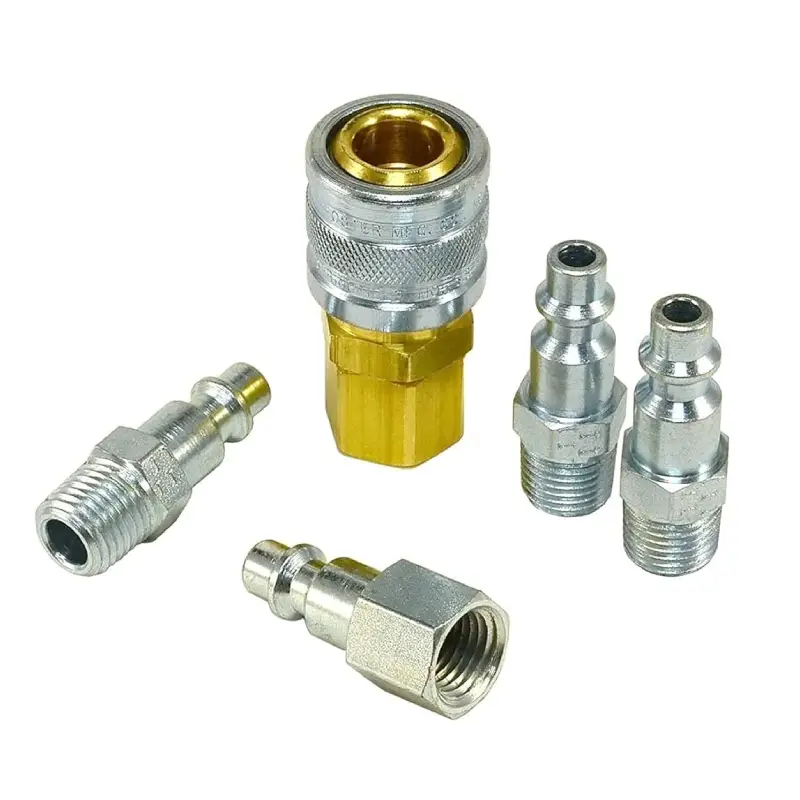
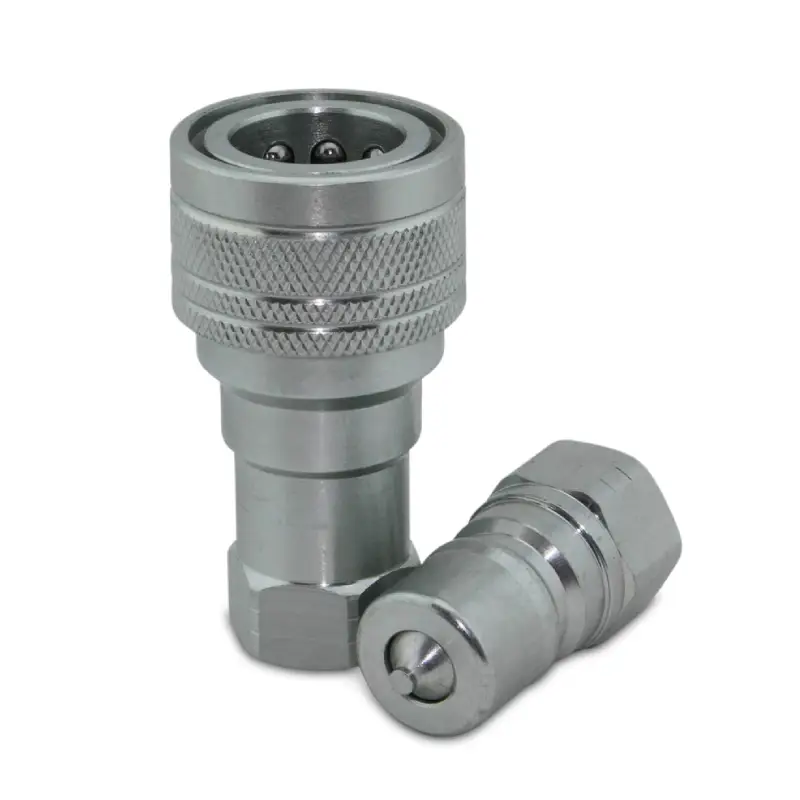
Design: Quick Connect Hydraulic End Fittings are designed for applications requiring frequent connection and disconnection of hydraulic lines. They feature a two-part design consisting of a male and female connector, which lock together with a simple push-and-twist or push-to-connect mechanism. This design allows for rapid connection and disconnection without the need for tools, making them ideal for applications where efficiency and speed are critical.
Application: These fittings are commonly used in applications such as hydraulic tools, test equipment, and mobile hydraulic systems where frequent changes are required. They are also used in applications where space is limited, and quick disconnection is essential for maintenance or troubleshooting. The quick-connect design minimizes downtime and simplifies maintenance, making them ideal for demanding environments.
Benefits: The benefits of Quick Connect Hydraulic End Fittings include their rapid connection and disconnection, tool-free operation, and ease of use. They are ideal for applications where speed and convenience are paramount. However, they are not suitable for all high-pressure or critical applications, and proper selection is essential to ensure compatibility and performance.
Compression Hydraulic End Fittings
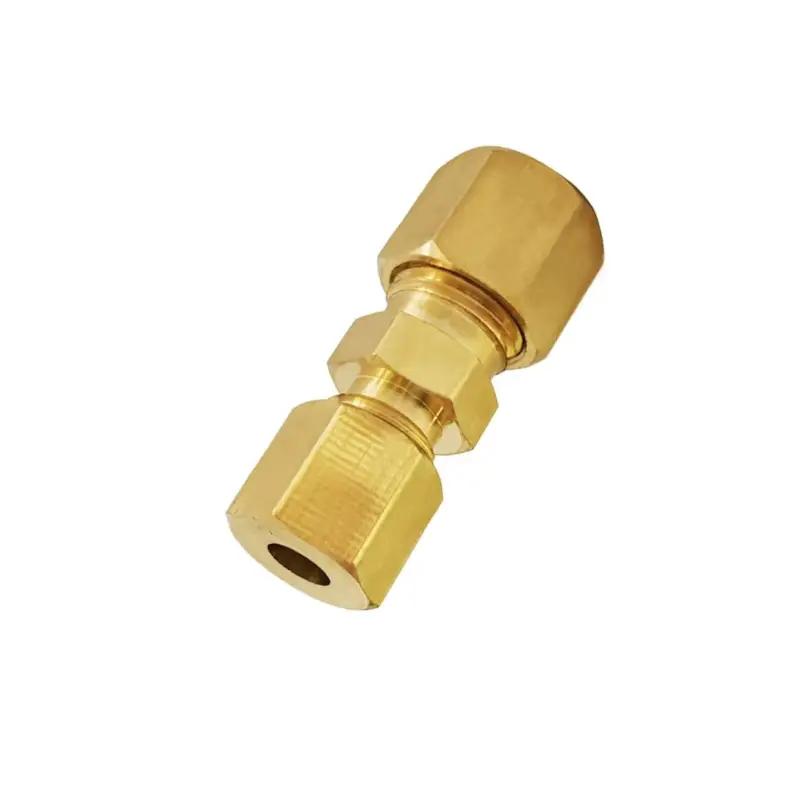
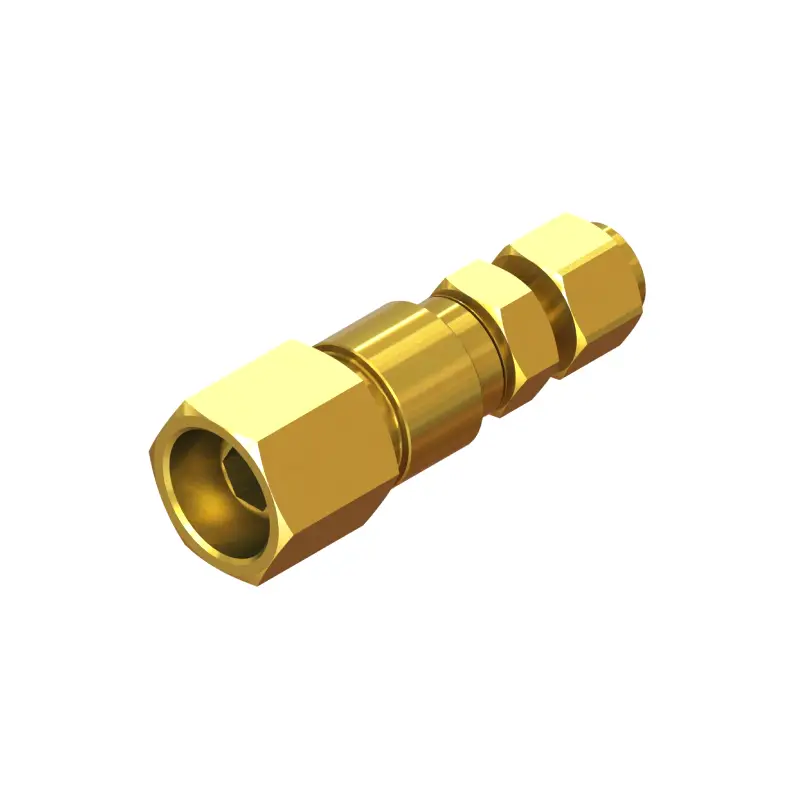

Design: Compression Hydraulic End Fittings are designed for connecting tubes or pipes in hydraulic systems. They feature a compression nut, a compression ring (ferrule), and a fitting body. When the nut is tightened, the compression ring deforms and grips the tube, creating a leak-proof seal. This design allows for a secure and reliable connection without the need for welding or threading.
Application: These fittings are commonly used in applications such as instrumentation, process control, and high-pressure fluid transfer systems. They are particularly popular in environments where vibration and temperature fluctuations are common, as the compression design provides a robust and reliable connection. Compression fittings are also used in situations where welded or threaded connections are not feasible or desirable.
Benefits: The benefits of Compression Hydraulic End Fittings include their ease of installation, reliability in high-pressure applications, and resistance to vibration and temperature fluctuations. They are ideal for applications where a secure and leak-proof connection is essential. However, they require careful installation to ensure proper sealing, and they are not suitable for all hose types.
Reusable Hose Hydraulic End Fittings
Design: Reusable Hose Hydraulic End Fittings are designed to be disassembled and reassembled, allowing for repeated use with different hoses. They feature a multi-part design that includes a fitting body, a ferrule or clamp, and a nut or collar. This design allows for easy replacement of damaged hoses without discarding the entire fitting.
Application: These fittings are commonly used in applications such as industrial maintenance, field repairs, and applications where frequent hose changes are required. They are particularly popular in environments where downtime is critical, and quick repairs are essential. The reusable design minimizes waste and reduces costs associated with replacing entire hose assemblies.
Benefits: The benefits of Reusable Hose Hydraulic End Fittings include their cost-effectiveness, ease of maintenance, and reduced downtime. They are ideal for applications where frequent hose changes are required or where field repairs are common. However, they require proper assembly and maintenance to ensure reliable performance, and they are not suitable for all high-pressure or critical applications.
How to Choose the Best Hydraulic End Fittings
Choosing the best hydraulic end fittings involves considering several critical factors to ensure system reliability, safety, and efficiency. Here’s a comprehensive guide to help you make informed decisions to select the best hydraulic end fittings:
1. Application Requirements:
Pressure Rating:
Determine the maximum operating pressure of your hydraulic system. Select fittings with a pressure rating that exceeds this value to ensure safety and prevent failures.
Fluid Compatibility:
Consider the type of hydraulic fluid used. Ensure the fitting material is compatible with the fluid to prevent corrosion or degradation.
Temperature Range:
Evaluate the operating temperature range of your system. Choose fittings that can withstand the extreme temperatures encountered in your application.
Environmental Conditions:
Assess the environment where the fittings will be used. Consider factors like exposure to chemicals, moisture, or extreme weather conditions.
2. Fitting Type and Design:
Connection Type:
Choose the appropriate connection type based on your application needs. Options include crimp, hose barb, push-lock, quick connect, compression, and reusable fittings.
Size and Thread Type:
Ensure the fittings match the hose and component sizes. Select the correct thread type (e.g., NPT, JIC, SAE) for compatibility.
Material Selection:
Choose fitting materials based on corrosion resistance, strength, and durability. Stainless steel, brass, and carbon steel are common choices.
3. Quality and Reliability:
Manufacturer Reputation:
Select fittings from reputable manufacturers known for producing high-quality products.
Standards Compliance:
Ensure the fittings comply with relevant industry standards (e.g., SAE, ISO) to guarantee quality and performance.
Testing and Certification:
Look for fittings that have been tested and certified to meet industry standards.
4. Installation and Maintenance:
Ease of Installation:
- Consider the ease of installation, especially for applications where frequent changes or repairs are required.
Maintenance Requirements:
Evaluate the maintenance requirements of the fittings. Reusable fittings, for example, may require more frequent inspections.
Tooling:
Make sure you have the proper tools for installation. Crimp fittings for instance, require a crimping machine.
5. Cost Considerations:
Initial Cost:
- Balance the initial cost of the fittings with their long-term performance and reliability.
Long-Term Costs:
Consider the potential costs associated with leaks, failures, and downtime. High-quality fittings can save money in the long run.
Key Considerations:
Leak Prevention:
- Prioritize fittings that provide a secure and leak-proof seal.
Safety:
- Always prioritize safety when selecting hydraulic fittings. Ensure the fittings can withstand the pressures and conditions of your application.
Expert Consultation:
- If you are unsure about which fittings to choose, consult with a hydraulic system expert or a reputable fitting supplier.
By carefully considering these factors, you can choose the best hydraulic end fittings for your specific application, ensuring optimal performance, safety, and longevity of your hydraulic system.
Conclusion
Understanding hydraulic hose end fitting types is crucial for ensuring the integrity and efficiency of high-pressure systems. Correct selection prevents costly leaks and failures, safeguarding operations. By considering factors like thread type, sealing method, and material compatibility, engineers can optimize system performance.
Choosing the right fittings demands careful evaluation of application-specific requirements. High-pressure environments necessitate robust, reliable connections that withstand demanding conditions. Knowledge of fitting standards and industry best practices is paramount for safe and effective hydraulic system design.
For expert guidance and a comprehensive selection of high-quality hydraulic end fittings, contact DF Hydraulics. We offer tailored solutions to meet your specific needs. Get a quote for your hydraulic end fittings from DF Hydraulics today and experience superior performance and reliability.